LS Mtron expands line of vertical injection molding machines
By Karen Hanna
LS Mtron’s injection molding machines (IMMs) are looking up.
The Anyang, South Korea-based company, which in recent years has made moves to amplify its presence in the U.S., announced in July it is expanding its line of vertical presses to include 10 new models.
Equipped with Industry 4.0 capabilities, the hybrid presses are designed for sustainability, according to the company.
Peter Gardner, who was named president of LS Injection Molding Machine USA in January, said the company’s launch of its newly named LSG-V line — which also includes three existing presses — comes as the automotive industry looks to expand offerings of electric vehicles (EVs).
“Specifically,” he said, “we see interest for EV battery applications. As Korean EV battery manufacturers, including our founding company, LG, are increasing production and research, it is a driving force for vertical IMM demand. Being a Korean manufacturer, we quite naturally are working closely to fulfill the anticipated needs.”
Ten new presses, with clamping forces ranging from 35 tons to 660 tons, join three existing IMMs, with clamping forces ranging from 100 tons to 350 tons, in the LSG-V portfolio. The three existing presses originally were available only in a rotary configuration, but users can spec out presses in the new line in a variety of ways, with options for vertical or horizontal injection, and rotary-table, shuttle or single-station designs.
“Previously, we offered a limited range of three models ranging between 100 tons and 350 tons, and only vertical rotary,” Gardner said in a press release. “With the addition of the newly expanded LSG-V series, we can now provide customers with a wider array of sizes and features, all of which is designed to meet and exceed their expectations.”
The IMMs can perform according to a wide range of injection specifications, such as speed and pressure, and they have support for up to four injection fixtures.
According to the company, they are designed for energy efficiency, ease of use, operator safety and relatively low operating and maintenance costs.
For molders, finding space for new IMMs can be a challenge.
“Space is always a concern in many facilities, so compact size is important,” Gardner said. “And more importantly, the lower table height is desired, to avoid the customer needing to install large space-consuming operator or robotic platforms."
For durability and stability, the LSG-V IMMs have a four-post tie-bar structure. A slide-type guide bar design minimizes transfer resistance, making the IMMs appropriate for precision molding.
The use of servo motors and drivers minimizes product defects.
For enhanced productivity, users of the presses can simultaneously perform product take-out and insertion processes during injection.
LS Mtron will show off one of the newest machines, a 170-ton LSG-V molding an EV component for sister company LS Automotive, at NPE2024.
Contact:
LS Injection Molding Machine USA, Duluth, Ga., 470-724-2263, www.lsinjectionusa.com
Karen Hanna | Senior Staff Reporter
Senior Staff Reporter Karen Hanna covers injection molding, molds and tooling, processors, workforce and other topics, and writes features including In Other Words and Problem Solved for Plastics Machinery & Manufacturing, Plastics Recycling and The Journal of Blow Molding. She has more than 15 years of experience in daily and magazine journalism.
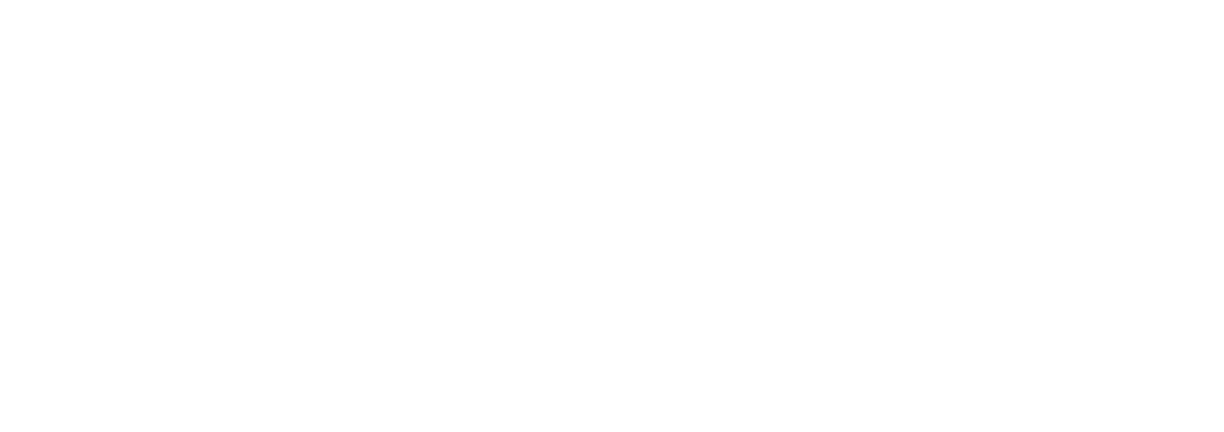