By Karen Hanna
Traditional manufacturers account for the biggest market segment interested in a large new 3D printer from Voxeljet.
Currently used only in a beta version, the VX1000 HSS is appropriate for small and medium-sized batches. It employs a high-speed sintering process to apply and selectively wet plastic powder in thin layers, fusing them by means of energy input. The company anticipates going commercial with the new printer in November, depending on factors involving the still-recovering supply chain, said James Reeves, the company’s global director of polymer sintering.
“With our HSS technology, we are relatively new to the polymers market, but are much more established in other materials, such as sand, for example, which we print to create molds and cores for the metal casting industry. There, we have customers using our printers to produce over 100,000 of the same part per year,” he said. “We are in discussions with polymer customers about similar production volumes.”
According to its manufacturer, the VX1000 HSS boasts fast and consistent layer times and produces high-quality parts. It can be used to make parts that are otherwise difficult to manufacture.
“The VX1000 HSS enables the cost-efficient production of plastic components that can hardly, or not economically, be manufactured on an industrial scale using conventional injection molding. Without limits — around the clock,” the company’s website states.
According to Reeves, the printers come with a tray, called a jobbox, in which the material being printed is inserted. The design of the jobbox maximizes the dimensions of the parts the VX1000 HSS can handle.
As Reeves explained in an email, “The jobbox is literally a box that is pushed in theThe printer is fully automated and comes equipped with a large number of sensors, making it a good fit for smart production chains and applications that require traceability.
It is easy to integrate into the entire manufacturing chain, Voxeljet says.
Designed for processing polyamide 12, it can handle many other resins, according to Voxeljet.
While Voxeljet calls the printer “an economically viable alternative to conventional plastic injection molding,” Reeves doesn’t view 3D printing and injection molding as rivals. Instead, the processes are complementary.
“We don’t look at it as competing with injection molding — if a part can be injection molded, then it should be injection molded. 3D printing should be used when it adds value to the component; this is usually when the design becomes more complex and difficult to mold. Part consolidation, lightweight organic structures and mass customization are some of the leading design elements that can make 3D printing viable in production volumes.”
Traditional manufacturers account for more than 60 percent of machine sales for Voxeljet, which has been supplying additive manufacturing technologies to metal foundries for over 20 years.
“There is a significant opportunity for contract manufacturers. A 3D printed part has a higher value than a molded part of a similar size, so revenues are higher per part, which leads to higher productivity and greater profits,” Reeves said.
Karen Hanna, senior staff reporter
Contact:
Voxeljet America Inc., Canton, Mich., 734-808-0025, www.voxeljet.com
Vital Statistics
Dimensions of the jobbox, or tray, in which parts are printed | 3.2 feet by 1.7 feet by 0.59 feet |
Maximum length of products | 3.2 feet |
Resolution | 360 dots per inch |
Build volume | 216 liters |
Materials | Polyamide 12 as standard and other polymers, such as PP, TPU, polyether block amide and ethylene-vinyl acetate, on request |
Karen Hanna | Senior Staff Reporter
Senior Staff Reporter Karen Hanna covers injection molding, molds and tooling, processors, workforce and other topics, and writes features including In Other Words and Problem Solved for Plastics Machinery & Manufacturing, Plastics Recycling and The Journal of Blow Molding. She has more than 15 years of experience in daily and magazine journalism.
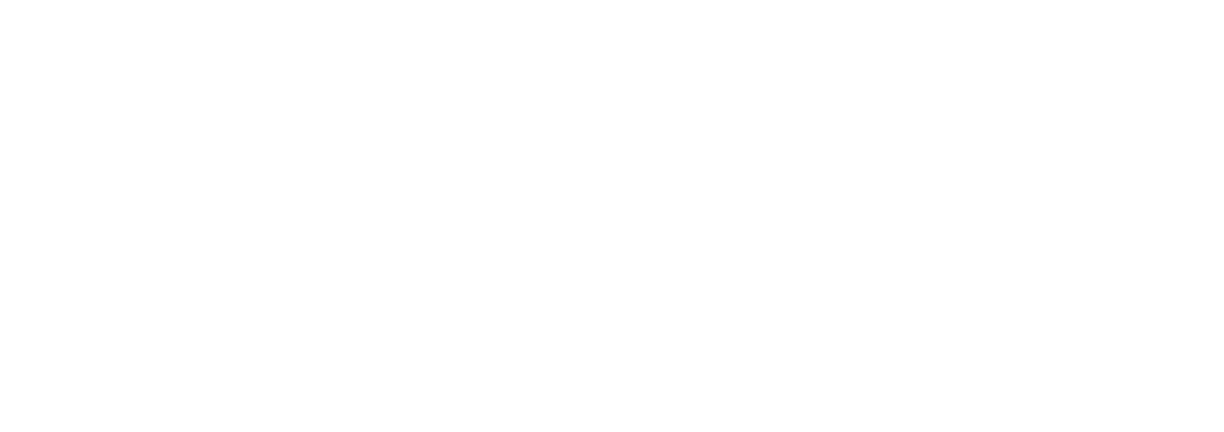