3D printers provide tailored fit to meet mass-customization demand
By Karen Hanna
If you’re an adult of a certain age and wore braces as a kid, you might have heard the insults: “Metal mouth!” “Brace face!” “Train tracks!”
Fortunately, while bullies’ insults are stuck in sixth grade, technology is forging ahead.
“Probably the highest-volume application is in the aligner moldmaking. It's one-offs; every treatment has around seven to 10 molds that are then transferred into an invisible aligner,” said Fabian Krauss, head of the polymer systems business for EOS. “And customization, it's a one-off; it's directly from a scan to a print. Fantastic.”
Align Technology has been one of the beneficiaries. Since 1999, it’s used stereolithography 3D printers from 3D Systems Corp., Rock Hill, S.C., to make dental aligners for 15 million patients,.
“This dramatic shift allows dental professionals to straighten teeth with Invisalign clear aligners and achieve what others never thought possible: changing someone’s smile and offering them the opportunity to do so more comfortably and discreetly, and conveniently than wires and brackets,” said Srini Kaza, senior VP for product research and development for Align Technology.
Formlabs — which makes 3D printers used to manufacture clear aligners for another company, Modern Clear — has seen customers in multiple industries exploit the technologies’ mass-customization capabilities, according to Derek Vilim, product hardware manager.
As an example, he pointed to a collaboration between Formlabs and toymaker Hasbro.
“Together, the companies created a revolutionary new personalization platform, the Hasbro Selfie series, which uses the power of Formlabs 3D printers to enable fans to create a collector-grade, 6-inch action figure in their likeness,” he said. “For the first time ever, action fans can scan their face with a smartphone device and have a custom-made, look-alike action figure delivered directly to their door. This project has proven that any company can develop a scalable manufacturing workflow for mass customization with 3D printing.”
Custom products, made en masse
Its flexibility sets additive manufacturing (AM) apart, said Francois Minec, global head of 3D polymers for HP's Personalization and 3D Printing business, which supplies printers used in a variety of applications, including making shoes and orthotics. He predicted brands in other industries are likely to cash in, too.
Related: See innovative parts produced using 3D printing technology
“In an industry where patient personalization is essential, the ability to quickly make adjustments to hearing aids, insoles, and even prosthetics and orthotics can be life-altering for patients,” Minec said. “This is one area where 3D printing truly shines and can potentially take over traditional plastic processing methods and become the primary tool.”
Like many 3D printing projects, the development of medical devices via 3D printing often starts with a scan.
In the offices of the 243,000 Invisalign-trained dentists and orthodontists, patients first get an iTero intraoral scan. The doctors then use proprietary software to map out a custom treatment plan and create a virtual 3D model for each stage of treatment.
Typically, patients get new aligners every week or two, to accommodate changes to their mouth structure. The entire process can take 12-18 months, Kaza said.
“Medical and dental 3D printing has proven to be more cost-effective compared to traditional production methods,” Vilim said. “Each patient has specific anatomy, and 3D printing is an accessible method enabling providers, facilities and manufacturers to create custom devices, guides, models and more to suit each patient without high production costs.”
Formlabs customer Modern Clear has served more than 150,000 patients around the world, he said.
In addition to its work in the dental field, Formlabs also has seen success with the use of 3D printers to treat serious medical conditions. For example, Vilim cited the production of FDA-registered, Medicare-covered upper-limb prosthetics by San Diego-based Psyonic, the creator of the Ability Hand.
In another case, health-care providers at Romans Ferrari, a pediatric rehabilitation center in Miribel, France, use a 3D scanner, CAD software and a Formlabs 3D printer to create a mold to thermoform compressive masks for patients dealing with trauma or severe burns.
The process is more comfortable for patients than a traditional plaster cast, Vilim said.
“3D printing is enabling companies like Romans Ferrari to reimagine their approach, delivering improved patient outcomes without raising costs,” he said.
For some providers, the process has become essential.
“If you were in the aligners business ... and you didn’t adopt 3D printing, you lost the game,” said Tali Rosman, an AM expert who advises early-stage companies on strategy, product roadmap and corporate development.
Kaza, Vilim and Minec see further, untapped potential for 3D printing’s mass-customization capabilities.
3D printer makers can smile thinking the demand can only grow, as industries beyond the medical and dental fields turn to their technologies.
“Mass customization and personalization will also soon become mainstream once companies understand the value it can provide for their business initiatives,” Vilim said.
Karen Hanna, senior staff reporter
Contact:
EOS, Pflugerville, Texas, 512-388-7916; Novi, Mich., 248-306-0143, www.eos.info/en
Formlabs Inc., Somerville, Mass., 617-702-8476, www.formlabs.com
Tali Rosman, [email protected], via Linkedin at www.linkedin.com/in/talirosman
Karen Hanna | Senior Staff Reporter
Senior Staff Reporter Karen Hanna covers injection molding, molds and tooling, processors, workforce and other topics, and writes features including In Other Words and Problem Solved for Plastics Machinery & Manufacturing, Plastics Recycling and The Journal of Blow Molding. She has more than 15 years of experience in daily and magazine journalism.
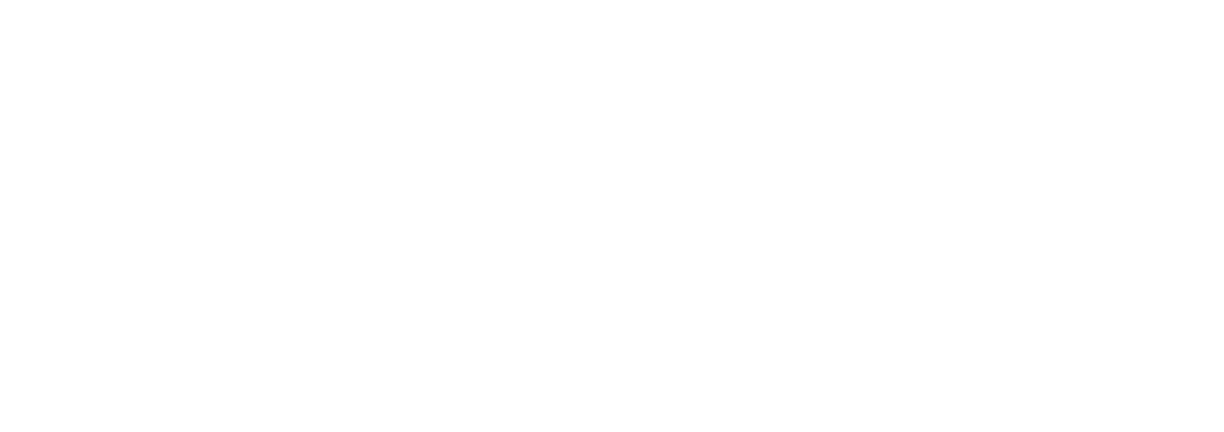