Sustainability initiatives drive interest in thin-wall packaging
By Bruce Geiselman
As governments and corporations embrace sustainability initiatives, their efforts are helping fuel interest in thin-wall containers and thin-wall packaging, said Michael Sansoucy, VP of business development and turnkey solutions at Arburg Inc.
“There is a lot of pressure to reduce the amount of plastics used in packaging,” Sansoucy said. “That is a global phenomenon, and it is certainly much more evident in Europe. Since we can’t simply stop using plastics, thin-wall designs are increasingly preferred.”
Thin-wall packaging benefits sustainability efforts because it requires less plastic, but thin-walling also makes the packaging lighter, and that means it takes less energy to transport it.
“It’s important to remember that plastic packaging, in general, has many benefits over paper, glass or aluminum, and thin-walled packaging just takes that to another level,” Sansoucy said.
The market for thin-wall packaging is projected to continue growing, particularly relative to the overall packaging market, Sansoucy said.
“But I don’t anticipate a significant expansion of production capacity in the immediate future, as the industry rebounds from the COVID pandemic and deals with increasing pressures on single-use plastics.”
Companies wanting to transition to thin-wall molding face some technical challenges.
“You certainly need a capable molding machine for starters,” Sansoucy said. “You can’t just use any general-purpose machine for these applications. You need a high-quality, high-performance mold and most of the time, you need automation. Running as fast as these machines do, you need to be able to automatically capture these parts as they come out of the mold, and you need to package them very efficiently for shipment to the end-user.”
Arburg is not only known for manufacturing high-quality injection molding machines, but also for offering turnkey systems.
“In a process where tenths of a second are important, you can’t just put together a machine, mold and robot and expect to be successful,” Sansoucy said. “Every little detail in the way these elements come together is important, so having an optimized cell is critically important.”
Arburg looks at manufacturing operations holistically, he said.
Injection molding machines used for thin-wall molding need to be precise and fast, with cycles in the range of 5-8 seconds, Sansoucy said.
“You can’t have any process drift if you are trying to make a high-quality product consistently,” he said. “You need a fast and accurate clamp that can move very quickly to the exact positions set for that application. In the injection unit, you need something that can inject the material fast and the unit needs to be very responsive. Speed and power need to be nearly instantaneous.”
In addition, a robust frame is essential for durability given the fast cycles taking place millions of times per year, Sansoucy said.
Arburg also strives to produce a machine with a smaller carbon footprint both during operation and during its manufacture, he said.
At K 2022 and the Arburg Anniversary Days 2023, Arburg demonstrated how injection-compression thin-wall molding can provide an alternative to thermoforming.
The demonstration involved an electric Allrounder 720 A with a clamping force of 326 tons and a size 1300 injection unit. The machine, thanks to the company’s new “Ultimate” performance level variant, achieved very high injection volume flows and injection speeds of up to 400mm per second, according to Arburg.
Brink, a molds and automation company based in the Netherlands, provided a four-cavity mold that produced thin-walled in-mold-labeled round cups from polypropylene. The flow path/wall thickness ratio was 380:1, Sansoucy said.
“The application required precision positioning and high-level reproducibility,” Sansoucy said. “To ensure absolute parallel compression, the mold was fitted with four compression path sensors and the entire process was monitored by the Gestica control system.”
Each of the four molded cups weighed just 12 grams and had a wall thickness of only 0.37 millimeters. Cycle time was 3.95 seconds.
Brink also provided the production cell with a side-entry robot that inserted the labels and removed the finished cups and stacked them on a conveyor belt.
“The demonstration illustrated many of the sustainability benefits of thin-wall molding,” Sansoucy said. “The all-electric machine is very energy efficient, and that efficiency is heightened by using the injection compression process. The high-flow path/wall-thickness ratio would normally require very high injection pressure, achieved at the expense of energy consumption. Instead, plastic is injected into a partially open cavity using comparatively low pressure and final compression is achieved when the mold is fully closed.
“Compared to similar thermoformed and labeled containers, injection-compression plus IML eliminates the backing film required with conventional foil labels, and there is none of the waste associated with thermoforming skeletons.”
The K-Show demonstration used a biomass-balanced and ISCC (International Sustainability and Carbon Certification)-certified PP containing bio-derived feedstocks.
Contact
Arburg Inc., Rocky Hill, Conn., 860-667-6500, www.arburg.com/en
Bruce Geiselman, senior staff reporter
Bruce Geiselman
Senior Staff Reporter Bruce Geiselman covers extrusion, blow molding, additive manufacturing, automation and end markets including automotive and packaging. He also writes features, including In Other Words and Problem Solved, for Plastics Machinery & Manufacturing, Plastics Recycling and The Journal of Blow Molding. He has extensive experience in daily and magazine journalism.
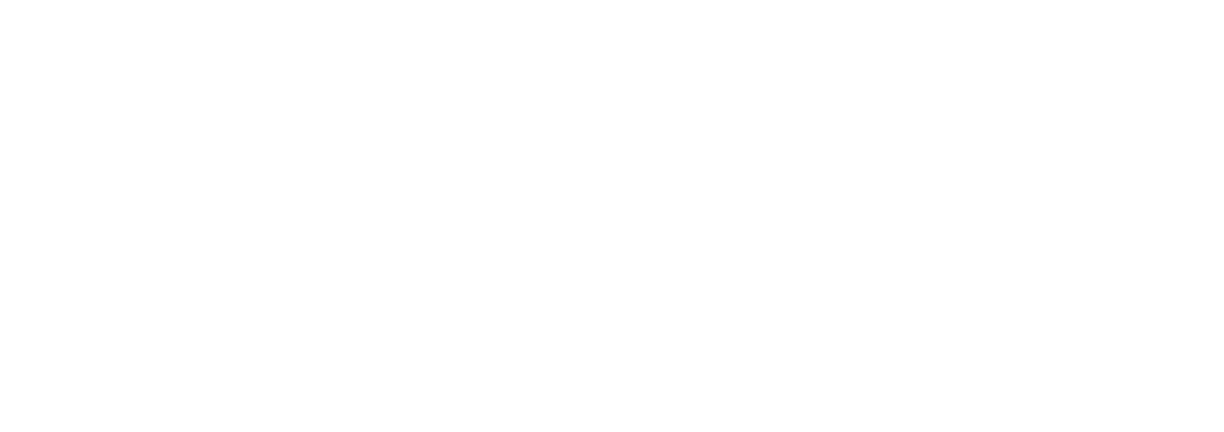