Plasma treatment speeds spoiler production
Problem: A process to apply an adhesive tape to a part was smelly, labor-intensive and unpleasant.
Solution: Plasma treatment replaced the need for an adhesive promoter and allowed the molder of the part to automate much of the process.
By Karen Hanna
Molder Jeff Ignatowski knew with his nose that the process his company had undertaken to finish parts for a General Motors (GM) supplier wasn’t going to fly.
It stunk.
As he applied a liquid adhesive promoter from 3M to a vehicle spoiler, he thought back to a job he’d had at another company, which specialized in painting.
“I said [to] myself, ‘This is just miserable, I can’t do this to these people day in and day out. There’s got to be a better way,’” recalled Ignatowski, who became president of Champion Plastics, an Auburn Hills, Mich., injection molder, in January after a two-year stint as its director of sales and marketing.
Ions proved the answer — and led to a prestigious Innovation Award last year from the Manufacturers Association for Plastics Processors.
More than a year ago, Ignatowski and his co-workers were focused on an “all-hands-on-deck" situation — delivering the GM parts to meet the need for a customer in Champion Plastics’ biggest end-market. While satisfying the customer’s initial demand was paramount, Ignatowski already was considering how to improve the process.
The adhesive promoter — required for sealing a pressure-sensitive adhesive tape to the spoiler’s thermoplastic vulcanizate (TPV) surface — wasn’t pleasant to handle, and the application process was labor-intensive and vulnerable to variability.
“It’s very smelly. ... It’s got a paint-fume type of smell to it, and so it’s not very user-friendly. It’s recommended that you wear masks, and then we generally have fans that blow the fumes away from the operator,” Ignatowski said. “So, it wasn’t environmentally very friendly for the operators. Not to mention, we had two full-time people, that’s all they did, is apply [this] every day, day in and day out.”
The dilemma reminded Ignatowski how a former employer had used plasma treatment to prepare the substrates of products it painted.
That insight led Champion Plastics to reach out to Enercon, which makes plasma treaters.
L. Wilson Lee, director of sales and business development for Enercon, said knowledge of the advantages of plasma treatment is growing among the manufacturers of plastic and aluminum parts — his company’s biggest end-markets.
“Anytime they want to have a better bond, or printing or coding or painting, or cleaning, anytime they need to do any of those to the surface, plasma is a good option,” Lee said.
Effective with most types of plastics, plasma treatment increases surface energy by creating an ablation effect that can remove contaminants from the surface of an object.
“If it’s a low surface energy, like a plastic, everybody’s taken a Sharpie or something and written on something that was plastic, and it just wipes right off. The reason that happened is that surface energy is very, very low,” Lee explained. “So, what we do is, when we treat something we’re increasing that surface energy, so when you write on it with a Sharpie or something like that, now it sticks.”
Champion Plastics, which employs about 25 people and has around 10 injection molding machines, needed about four months to explore plasma treatment and make tweaks to develop a process to replace manual application of the adhesive promoter.
To be sure that plasma treatment could work with the TPV parts Champion Plastics makes, Enercon performed some experiments, Ignatowski said.
The molder also worked with its automation partner JH Automation, Port Huron, Mich., to explore how to handle the parts so they could be molded, then presented to a plasma treater without human interaction.
“We had to invent an environment that would flip the parts, essentially, and [hand them] to itself, which then allows for the plasma treating,” Ignatowski said.
Initially, Champion Plastics wasn’t convinced plasma treatment would do the trick. One weekend — when parts were plasma-treated but left unfinished — was enough to show that Enercon’s solution would stick.
“When we were first applying the tape, immediately after plasma treating, we were actually disappointed in the results. And it was almost by accident, that … we ran some parts on Friday, and, by Monday, they actually had improved,” Ignatowski said.
Typically, Lee said, parts should be finished with products like paint or labels immediately following plasma treatment.
“As long as they handle it properly, they can be assured that they’re still above [the] surface energy they need to get the bond they need,” he said.
Ignatowski said Enercon has shown Champion Plastics how to test the surface energy, or dyne level, of parts so that the molder is able to optimize the timing between plasma treatment and tape application.
Meanwhile, Champion Plastics also worked with the Tier 1 supplier to be sure GM was comfortable with the changes.
Working together, the partners developed a new setup — incorporating a blown-ion plasma treater from Enercon, along with custom automation from JH Automation — that Champion Plastics has been using for about a year.
It’s provided benefits to Champion Plastics, its customer and GM, Ignatowski said.
“Part of it was some cost drivers that helped sell the concept because we were seeing increases in material costs. From the way we originally quoted the program, we didn’t have as much labor as the actual execution of it [required]. So, we were actually also approaching [Champion Plastics’ customer] with a price increase, but said, as a Plan B, ‘We took the initiative to come up with a cost-avoidance solution.’ And that’s what the plasma treating was,” he said.
The two employees who formerly worked full time applying the adhesive promoter have been redeployed, as has a person who was needed at the cell before Champion Plastics and JH Automation developed end-of-arm tooling for the robot now stationed there, Ignatowski said.
“It freed up labor to allow us to do other things. I mean, it was literally over-consuming our facility before we made the change,” he said.
Initially expected to last 6 years, the program involving the GM parts might be extended, he said.
According to a case study provided by Enercon, the plasma treater and additional automation cost Champion Plastics $45,000. But the reduction in labor needs, as well as other ancillary costs, will save the company $850,000 over the duration of the original project.
Automating the process has had the collateral effect of eliminating variability, and the setup has increased throughput, Ignatowski said.
“Now that we’ve got this running smoothly, we’re looking at, ‘OK, now, how do we automate the actual tape application itself?’ Because we still have labor on a daily basis that’s applying tape,” he said. “So, we’re thinking about transferring the technology from our existing three-axis cell over to one of our six-axis cells and then potentially having a six-axis robot not only plasma the parts, but then, once they’re plasma’d, immediately then automate the tape application as well, which essentially then would let us do a lights-out solution to this whole project.”
When he first started working with plasma about a decade ago, Lee said, very few people knew about its benefits. But that’s changing, and about 30 or 40 percent of Enercon’s customers have made more than one purchase of the technology.
According to Ignatowski, based on its recent experience, Champion Plastics might become part of that repeat traffic. Its first foray into plasma treatment likely won’t be its last.
"We haven’t really bothered trying to go back; there aren’t programs that are big enough to justify that. But on new programs, we’ve essentially said, ‘Parts will not be using adhesive promoter; they will be plasma-treated,’ ” Ignatowski said.
Karen Hanna, senior staff reporter
Contact:
Enercon Industries Corp., Menomonee Falls, Wis., 262-255-6070, www.enerconind.com
JH Automation, Port Huron, Mich., 810-985-9960, www.jhautomation.com
Karen Hanna | Senior Staff Reporter
Senior Staff Reporter Karen Hanna covers injection molding, molds and tooling, processors, workforce and other topics, and writes features including In Other Words and Problem Solved for Plastics Machinery & Manufacturing, Plastics Recycling and The Journal of Blow Molding. She has more than 15 years of experience in daily and magazine journalism.
Request More Information
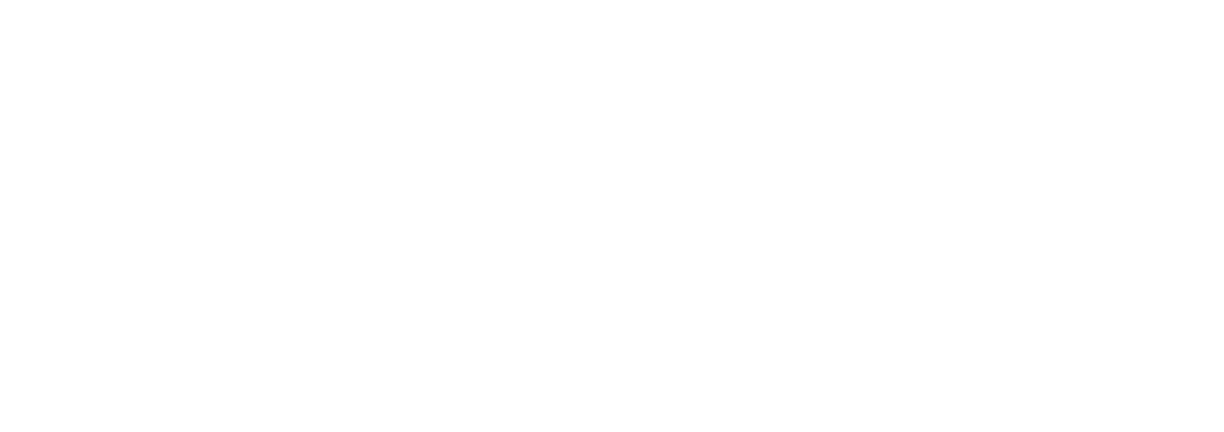