By Ron Shinn
Creating a lean manufacturing culture may seem like a complex and daunting goal at the beginning, but Viking Plastics proves you can accomplish it in 2-second increments.
The Corry, Pa., injection molder asks every employee, from company president and CEO Kelly Goodsel down, to make a 2-second improvement in their workspace every day and share it in daily meetings.
“We’ve been on a journey for the past 11 years now,” said Shawn Gross, VP of culture and business development. “We got really focused on growing our workforce along the lines of continuous improvement and a particular brand of lean manufacturing.”
By the book
The company follows a book by Paul A. Akers titled 2 Second Lean. “It is basically a boiling down of the Toyota production system into some very basic and simple elements,” Gross said. “We want everybody here to be able to know and see the eight forms of waste and be able to identify them in their workspaces and make small daily improvements.”
Everyone shares their 2-second improvement at drumbeat meetings held four times per day at shift changes. “Turning people into process engineers, looking at what they do and assessing the waste that might be present and just making small things better makes us better,” Gross said.
Viking has more than 100 molding machines in six plants around the world. In addition to injection molding, it has an extensive value-added assembly business. The company started with a proprietary line of plastic and rubber sealing closures for under-the-hood automotive and HVAC applications. Today, approximately 60 percent of Viking’s total business is automotive and the rest is in a wide range of industries. Annual sales were approximately $70 million in 2020.
There are 35 presses in the Corry headquarters plant, which opened in 1972. It has 120 employees working three shifts a day, five days a week.
“Turnover has been minimal in our skilled groups such as processors, maintenance, tool room and set-up people,” said Rob Elchynski, operations manager. “The operator side and direct labor has been more difficult to find and keep.” Viking has raised its starting wages to stay competitive.
Elchynski said a couple of the job openings are due to retirements and three are to replace people expected to retire soon.
Corry, which is about 33 miles southeast of Erie, Pa., is in a heavy manufacturing area. “Manufacturing plants are starting to compete against each other for people, which we didn’t in the past,” Elchynski said.
The Corry plant covers 64,000 square feet, split evenly between manufacturing and warehouse space. Approximately 85 percent of the parts made at the Corry plant are for the automotive market.
“Ford, General Motors, Stellantis, we’re direct to them,” said Gross. “Then you can look at any of their Tier suppliers for under-the-hood, molded, black functional parts and we are supplying them.”
Viking has taken reduced vehicle production in stride. “I think we are seeing odd ordering patterns in fits and starts,” said Gross. “The industry can’t continue to make 12 to 13 million vehicles a year when the market says it needs 15 to 16 million. We expect that to come back. For us, it has just been having to forecast what they are going to want.”
A new press planned for later this year will give Viking 36 presses in Corry. The additional press will be a Nissei with 197 tons of clamping force. Sizes of the presses range from 55 tons to 671 tons of clamping force.
There is one Sodick plunger-style press that was acquired to run a 16-cavity mold with a 1.2-gram shot weight.
“Prior to 2012, the company would buy used presses,” said Gross. “In 2012 we decided to start buying new presses and started working to minimize the average age of our machines. We started buying Haitians because they offered a competitive price and technology options.”
Gross said that Viking now standardizes on Nissei and Haitian presses, and its experience has shown the Haitians to be great general-purpose machines. He said the clamp position accuracy of the Nissei presses make them better at insert molding.
Elchynski said Viking has no specific criteria for replacing a molding machine. Age, capacity required for specific jobs, and maintenance history are all considered. “If you have an older machine that just runs, and it only runs one thing, we are not going to replace it even if it is 30 years old as long as it is still operational,” he said. “On the other side, if it’s a 25-year-old machine and we are running 100 hours a week on some high-precision parts, those are the ones we are going to look at.”
Viking views good part quality as coming through a series of systems. Its external defective parts rate is currently under 0.5 defective parts per million.
Quality is baked in
New projects are carefully planned to maximize the amount of automation that can be used. Trials are run until the part can be made perfectly. All of the conditions that went into that part are entered in a tablet that processors carry. The perfect part is awarded GBC distinction — a Good Batch of Cookies.
“Making cookies is no different than making a part,” said Elchynski. “You have to have all the right ingredients. You have to mix them correctly. Everything has to be done at the right temperature. If you turn the temperature up on the oven 20 degrees this time compared with last time, the cookies aren’t going to come out the same.”
Gross said Viking uses its molding machines to discern product quality. “A decade ago, we had a lot more people directly looking at products to inspect the quality. Now the machines are either putting the part into the good box or the scrap box, based on the output from that shot.” Viking has RJG cavity pressure monitoring technology on 10 presses.
All new Viking employees must complete training programs from Routsis Training. Some plant floor employees also attend courses at Penn State Behrend and the American Injection Molding Institute, both in Erie.
The 50-year-old plant does not have overhead cranes, so it uses forklifts for an average of 15 mold changes per 24-hour shift.
Boosting productivity
Some proprietary, under-the-hood caps run in highly automated cells built mostly in-house. Parts come out of the press and go into box indexing units. Once boxes are filled, elevators move them to a part counting or weight measuring station. Once every four hours or so a person moves the filled boxes away from the machine and loads empty containers. Scrap is ground and goes into a central, closed-loop material handling system.
Millions of caps have a seal inserted in a similar, automated system.
The automated boxing units mean only one operator is needed to run five or six presses.
“We want to do everything in-process that we can,” said Elchynski. “We have a lot of value-added processes. It is very important to us to be able to automate that and not do it with a human.”
The plant’s material handling system was built by Conair and AEC. There are two silos for higher-use resin, but most material comes in gaylords.
A wide range of robot brands are used — Ranger, Yushin, Wittmann, Epson and Universal Robots. Most end-of-arm-tooling is 3D printed in-house using a Stratasys Fortus 250mc fused deposition modeling system printer.
Dryers are primarily from Dri-Air. Most of the blenders in the plant are from Plastrac. Welding machinery is from Dukane and Branson.
EVs spark growth
Gross said the transition to hybrid and electric vehicles will be a significant one for Viking Plastics.
“We deal a lot with air conditioning and heating components under the hood,” Gross said. “With no internal combustion engine, we need to keep up with transitions of designs of the HVAC and other under-hood components.” Gross pointed out one electric vehicle where a significant number of components dealing with thermal management of the battery system are already being made by Viking.
“Trying to apply the high-temperature resins we deal with, such as [polyphenylene sulfide] and glass-filled nylons, to those market spaces, is a big push for us,” he said.
Has Viking’s 2-second approach to lean manufacturing been successful?
“I’ll start with what it is not,” Gross said. “It is not meant to be an austerity program to slice things away. We really take a different view. In 2011 we had half the sales as we do now and ran seven days a week in this plant with the same number of machines. Now we are double the sales and run five days a week. Viking Plastics strives to achieve 100 percent on-time delivery.
“We do big improvement projects, but it is really about the small daily things we do to eliminate frustrations and eliminate waste,” Gross said. “Our team’s journey is about just making daily small improvements, and over time you move mountains that way. We don’t want to overcomplicate it.”
Ron Shinn, editor
JUST THE FACTS
Company: Viking Plastics
Established: 1972
Headquarters: Corry, Pa.
Total plants: Six
Ownership: Spell Capital Partners LLC
Top official: Kelly Goodsel, president and CEO
Process: Injection molding
Employees: (Corry plant) 120
Ron Shinn | Editor
Editor Ron Shinn is a co-founder of Plastics Machinery & Manufacturing and has been covering the plastics industry for more than 35 years. He leads the editorial team, directs coverage and sets the editorial calendar. He also writes features, including the Talking Points column and On the Factory Floor, and covers recycling and sustainability for PMM and Plastics Recycling.
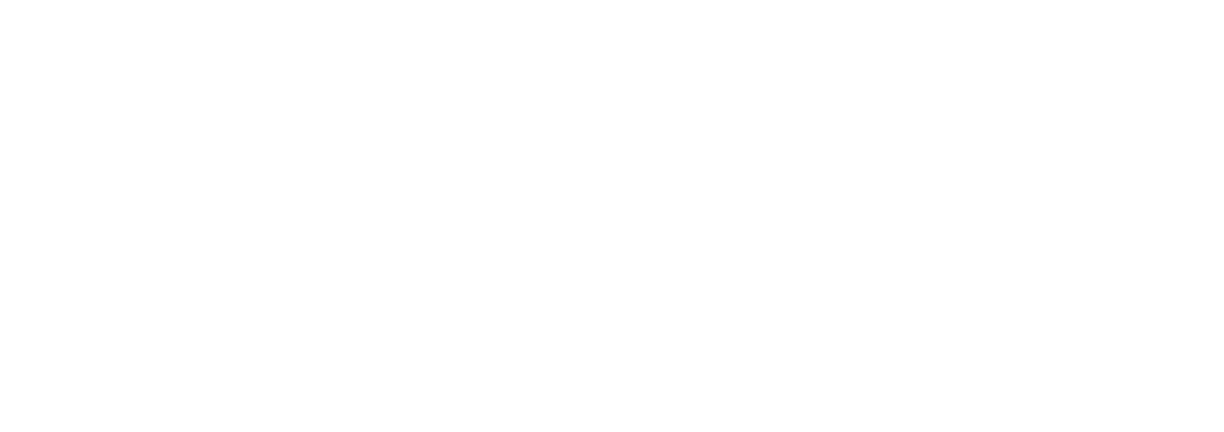