By Karen Hanna
Supply chain disruptions — punctuated most recently by a blockade of the Ambassador Bridge, where protesters had gathered between Windsor, Ontario, and Detroit — have become the latest challenge for the automotive industry, as it navigates through an unprecedented era.
At automotive parts maker Team 1 Plastics, re-assessing material availability has become a daily occurrence. Given the chaos the industry has experienced over the last two years, experts say the ability to take supply chain difficulties in stride is essential.
Team 1 is growing — it just purchased a new injection molding machine — but, like other suppliers, the Tier 2 manufacturer of under-the-hood components had to cope with a host of challenges since the COVID-19 pandemic began, said Dave Sanford, plant manager for the Albion, Mich., custom molder.
“We bring in quite a few materials from overseas that are imported, so you deal with shortages with that. And then you couple that with increased freight or shipping times, and it can just become a real nasty battle to deal with,” he said.
On Feb. 14, the automotive industry experienced some relief, after Canadian authorities cleared the Ambassador Bridge of vehicles and people protesting vaccine mandates and other pandemic restrictions; the bridge — a key artery for automotive-parts suppliers — had been impassable for nearly a week.
Even before the so-called trucker convoy protests, auto-parts makers like Team 1 have struggled.
“We had some shortage situations where we had to go through brokers for electronic components, in order to procure the parts that we normally were getting directly from the suppliers. By going through the brokers, we had to pay some extra costs,” Stephane Vedie said in January, just a few months after being named the company’s CEO in September 2021.
Last year, the automotive industry’s global production levels fell by 10 million vehicles due to shortages involving raw materials and computer chips, said Vedie, who believes his 25 years of experience navigating crises in the automotive industry appealed to his new employer.
Supplier, beware
Bindiya Vakil, the CEO and co-founder of Resilinc, a subscription service that tracks supply chain disruptions, calls the last two years “a black-swan event.”
With clients in more than 130 countries, Resilinc's 100,000-plus constituents make it a nerve center for more than 25 industries, as they report the outages they're experiencing.
For the automotive industry, computer chips were the canary in the coal mine. With a runup in demand for electronic devices that made life in quarantine bearable, electronics makers squeezed out automakers, and suppliers at every step of the supply chain paid the price.
Compared with the semiconductors in personal devices, chips in cars aren’t as sophisticated, said Glenn Jones, senior VP of product management for Blume Global, which provides digital supply chain solutions to Tier 1 auto-parts suppliers. Automakers prefer the tried-and-true.
“The value prop[osition] isn’t quite as high,” Jones said of vehicle semiconductors, “... So, if you look at iPhones, there’s not really a shortage of iPhones because the volume of that product is super-high.”
Semiconductor demand soared, but car makers didn’t get first dibs.
With his company’s customers unable to procure the electronic components they needed, Vedie said Luxit was sometimes left holding the bag.
“We ended up being stuck with inventory, being stuck with parts that we are not immediately able to sell,” he said.
Headed in the wrong direction
But the computer chip shortage was just one problem.
Blume maintains a web of customers and transportation providers, playing logistics matchmaker for companies looking to move goods or receiveLately, finding carriers and locations where goods can be quickly loaded or emptied is a struggle.
“Whenever a vessel comes into the port, there’s kind of two options for getting it to where it needs to go,” Jones explained. “The bigger option for automotive parts is railroad because [they have] to go to Detroit or Kentucky or wherever the big manufacturing plants are. And, so, railroads are also backed up. So, when you look at what’s happening on the ocean, that’s one angle on the backup. ... Ocean [transportation] was backed up 13 to 15 days, and then railroad [transportation] was backed up an additional 10 days on top of that.”
Jones thinks some problems might last through the summer.
Speaking in late December, Jones said 80 to 120 vessels were sitting at port, just on the West Coast, waiting to be unloaded — with containers waiting to be refilled elsewhere.
“It’s a disaster trying to get imports in any kind of a [transit] mode back into the U.S. and actually into a lot of Europe, too,” he said at the time. By late January, according to Blume, the West Coast backups were down to a couple dozen vessels.
Luxit CEO Vedie said port backups have reverberated through the vehicle-lighting maker’s supply chain.
“The cost of a container has increased tremendously, and then the increase of lead time also. We used to be able to [move] a container between China and the U.S. [in] about six to eight weeks. Now, it takes us sometimes 12 to 14 weeks to get this container, so you can imagine the extra inventory that you need to carry,” he said.
Many eggs, one basket
Made mostly in East Asia, semiconductors were grounded early in the pandemic — when passenger plane travel plummeted, cutting cargo capacity drastically, Jones said.
Those problems illustrate another weakness — over-reliance on too few suppliers, from locations or companies that might not merit that level of trust.
“If you’re an OEM, typically, about 60 to 75 percent of what you buy is sole-source. … At Tier 1 level, it’s pretty similar; it’s 50 to 60 percent of what a Tier 1 supplier buys ... they have no other vendor,” Vakil said.
For example, of all the products that entered the U.S. by ship in 2020, 12 percent came from just three ports near Shenzhen, China — a 67 percent increase from 2019, Resilinc said in a report last year, citing other sources.
Cost — rather than concerns over the robustness of the supply chain — has often dictated sourcing, especially in the automotive industry, said Peter Bolstorff, executive VP for the Association for Supply Chain Management (ASCM), which represents 185 companies in the U.S., include Tier 1 and Tier 2 suppliers.
“Automotive has had to do a shift there because, in the past, having been on the supply side of that, prior to my current role, they beat you up a lot. It’s more cost-oriented,” said Bolstorff, who formerly worked as a plant manager. “... Now, we’re thinking about supplier relationships. How do we share inventory positions, so that you can respond up or down to disruption?”
Making waves
As manufacturers like Luxit and Team 1 have experienced, issues that take place thousands of miles away can send shockwaves through the supply chain, even weeks and months later.
“The further you are down the supply chain, the more you’re subject to the variability in orders, in demand, so a small spike in orders from an OEM to a Tier 1 can lead to a very large and dramatic increase in orders by the time you get lower in the supply chain,” said Sig Huber, senior managing director for Riveron, a national business advisory firm specializing in accounting, finance, technology, and operations. "That’s called the ‘bullwhip effect.’ ”
The smaller the company, the more urgency to be attuned and responsive to change, Bolstorff said.
“I would [say] the Tier 2 folks that have 100 people that work for them, they have to be 10 times more supply-chain-effective than the automotive suppliers because they’re oftentimes stuck between two big giants, a huge supplier that’s multiple times bigger than them, and then a supplier or customer that’s multiple times bigger than them,” he said.
Talking it out
As a lean manufacturing consultant, Rick Bohan, president of Chagrin River Consulting, believes leaders can improve their customer service by doing a deep dive into their processes.
“We, as customers and folks in business, kind of thought, ‘Well, the supply chain just works like the sun rises in the morning and sets in the evening. Stuff gets put on boats in China, and three months later, it gets here, and everything’s working,’ ” he said.
Not anymore.
Recent experiences suggests the price of being caught off guard is high.
“What we’re starting to see more in the supply chain is companies trying to build in more early-warning systems or more market intelligence, in terms of raw materials and supplier issues,” said Linda Watson, an attorney with the Clark Hill commercial law firm, which has dealt with disputes involving auto OEMs and suppliers.
Experts say manufacturers have to monitor their suppliers, as well as the sub-suppliers that keep production running, and remain in constant communication with their customers and vendors.
“You have to be able to react every single day. You’ve got to meet every day and talk about where you’re at. What are you going to build today? What can you build today? What can’t you build today? 'And how do I adapt?'
“The ones who manage flexibility well are the ones who are going to get the work,” said Laurie Harbour, president and CEO of Harbour Results, a consulting firm that works with manufacturing companies, including injection molders and mold shops.
Role of Industry 4.0
Supply chain experts like Riveron's Huber stress the importance of tools that illuminate what is happening along the supply chain. To keep each other abreast of any issues that might affect production, supply chain partners can provide data on a need-to-know basis.
“If you think about an OEM, they know who they’re buying their parts from, but they don’t necessarily know who the subcomponent suppliers are. And I think they’re realizing now that there’s potential risk in the lower tiers that they want to be able to have visibility,” Huber said.
Developing insights into the whole supply chain — including what's happening outside the plant walls — is where companies like disruption-tracking firm Resilinc and transportation agent Blume come in. Both companies have networks of constituents that share data with each other. Resilinc, for example, maps supply chains for OEMs, which, in turn, identify their suppliers and locations down to the site and part level.
With Resilinc’s webs, companies have a near-real-time look into the perils and opportunities in their supply chains. The data sharing provides transparency about where components and subcomponents are actually sourced — and what's going on in those places that might put supplies in jeopardy.
“That’s the first thing is, ‘Where is my supply chain actually located, and then what is happening in these regions of the world that could have an impact to my deliveries?’ ” Vakil said. “... On our platform, the customers and suppliers come together during these disruptions and help solve the problem together.”
When an event such as bad weather or a labor strike derails production at any location, Resilinc notifies affected parties right away, so they can strategize a way forward by shifting to another supplier, re-prioritizing production schedules or taking other steps.
Resilinc also informs its users if it discovers that their suppliers are violating environmental or labor standards.
“Customers are using the information that suppliers provide for emergency response, disruption response, crisis management and to protect supply continuity. And to the extent that customers limit their usage of this information to these use-cases, certainly suppliers are very willing to; they understand that our futures are entwined,” Vakil said.
Digital tools make a difference, said Terry Onica, the director for the automotive segment for software supplier QAD, which offers a portfolio of options, including cloud-based enterprise resource planning (ERP), digital supply chain planning, global trade and transportation execution, and strategic sourcing and supplier management packages.
With a fully integrated ERP system, she said, manufacturers can provide insights to members into their supply chain within a day; a manual approach might take a week — per tier. She said she worked with a Tier 1 supplier with 52 locations that saved $1 million a year by investing in electronic data interchange (EDI) software, in addition to ERP..“Once the process and data is in place in ERP (versus spreadsheets) through automation, then there will be increased supply chain visibility and faster reaction time,” Onica wrote in an email.
Room for improvement
While experts said such transparency is essential, not enough companies have bought in — yet.
“If you had full visibility and you understood where your risk points were in your supply chain, you’d be able to protect for those, and so I do think, absolutely, that it would have blunted some of the impact” of recent crises, said Greg Alonso, a consultant with Plante Moran, a professional services firm that provides services to middle-market businesses in a variety of industries, including manufacturing.
Frustration over supply chain difficulties is giving way to a sense that greater collaboration is necessary, said Watson, a self-described optimist who, as an attorney, dealt with a slew of issues stemming from force majeure notices early in the pandemic.
“I think that I see more people being reasonable and realizing that it’s going to take a supply chain that works together to solve these problems,” she said.
One hurdle, as ASCM’s Bolstorff sees it, is that while most companies have access to Industry 4.0 tools, they are not exploiting all the data at their disposal. He believes companies are split into three camps — 20 percent are leading the way, 20 percent are falling behind, and the middle group is just trying to keep pace.
“The first step in all digital transformation is, ‘How do I use more of what I’ve got?’ ” Bolstorff said.
Leaders will not only invest in the appropriate tools, they also will make strategic decisions around long-term issues, such as sustainability, climate change and the changing automotive market, he said.
To be successful, managers and executives will strive for improvement in every aspect of their businesses, said Jade Rodysill, EY Americas chemicals and advanced materials industry leader, who supports clients in the chemicals, advanced manufacturing and mobility industries.
“It’s a realization that you can’t stop. You can’t stop your digital transformation. You can’t stop your push towards a more circular business model and meet your sustainability requirements. You can’t stop and think your customer-satisfaction levels are where they need to be and that you’re OK. You have to push in all those dimensions.”
Homeward bound
Some experts are eyeing an even bigger change — the ultimate redesign of the supply chain.
Ron Jacques is a Lean Six Sigma consultant to businesses, including manufacturers.
“I am a strong proponent of make where you sell. For cars sold in America, all parts should be produced here.” His advice is succinct: “Bring … plastic injection molding back to the U.S. to avoid supply chain issues tied to foreign sourcing.”
“Today, we take an important step toward our goal to rebalance global chipmaking capacity and help boost production to meet the surging demand for advanced semiconductors, powering a new generation of innovative products,” Intel CEO Pat Gelsinger said. “The new factories we’ll build in Ohio are part of our strategy to increase semiconductor R&D and global manufacturing capacity and restore U.S. semi[conductor] manufacturing leadership.”
Just as the chip shortage has had consequences up and down the supply chain, more-reliable access to the components could spawn a constellation of benefits. Chris Spear, American Trucking Associations president and CEO, said that with more available chips, truck manufacturers and maintenance shops could address a backlog of orders — freeing more trucks to fill the country’s shipping needs.
“This is how we climb out from these COVID-induced shortages — by investing in our nation’s supply chain,” he said.
With manufacturers currently dealing with unprecedented problems finding workers, Resilinc’s Vakil believes in casting an even bigger net — to a young, ready workforce eager for jobs elsewhere in the Americas.
“Look at that regionalized approach. I mean, we’re connected by land to Central America. The labor force, their average age is 26 years. It’s cheaper than China; the cost of labor in Central America and parts of Mexico is now cheaper than China. And it is no ocean dependency. And there’s plenty [of people] that [are] needy, desperate for legal employment opportunities,” she said.
Closer to home, Luxit already is doing its part.
Between plants in Michigan and Tennessee, the company recently has created at least 100 positions.
“We made investments in automation ... we made some serious commitments, with the investment that we made, and this allows us to be competitive manufacturing in the U.S., and this will stay,” Vedie said.
Luxit’s flexibility and relationships with customers give him confidence.
“I don’t know any more what ‘normal’ means. … I don’t think there will ever be ‘normal,’ but we need to adapt to a new normal, and this is what I think our industry is good at, at the end,” he said.
Karen Hanna, senior staff reporter
Contact:
Association for Supply Chain Management, Chicago, 773-867-17,77, www.ascm.org
Blume Global, Pleasanton, Calif., 781-263-0200, www.blumeglobal.com
Chagrin River Consulting, Akron, Ohio, 216-409-9046, www.chagrinriverconsulting.com
Clark Hill PLC, Birmingham, Mich., 248-642-9692, [email protected], www.clarkhill.com
EY Americas, www.ey.com/en_us/chemicals
Harbour Results Inc., Southfield, Mich., 248.552.8400, www.harbourresults.com
Plante Moran, www.plantemoran.com
QAD, Santa Barbara, Calif., 805-566-6100, www.qad.com
Resilinc Corp., Milpitas, Calif., 408-883-8053, www.resilinc.com
Riveron, Miami, 305-563-8000, [email protected], https://riveron.com
Type of alerts, by the numbers
Most common alerts, by year
2018 | 2019 | 2020 | 2021 |
Merger and acquisition | Factory fire | Factory fire | Factory fire |
Factory fire | Factory disruption | Merger and acquisition | Merger and acquisition |
Leadership transition | Business sale | Business sale | Business sale |
Factory disruption | Leadership transition | Factory disruption | Factory disruption |
Extreme weather | Recall | Human health | Supply shortage |
Karen Hanna | Senior Staff Reporter
Senior Staff Reporter Karen Hanna covers injection molding, molds and tooling, processors, workforce and other topics, and writes features including In Other Words and Problem Solved for Plastics Machinery & Manufacturing, Plastics Recycling and The Journal of Blow Molding. She has more than 15 years of experience in daily and magazine journalism.
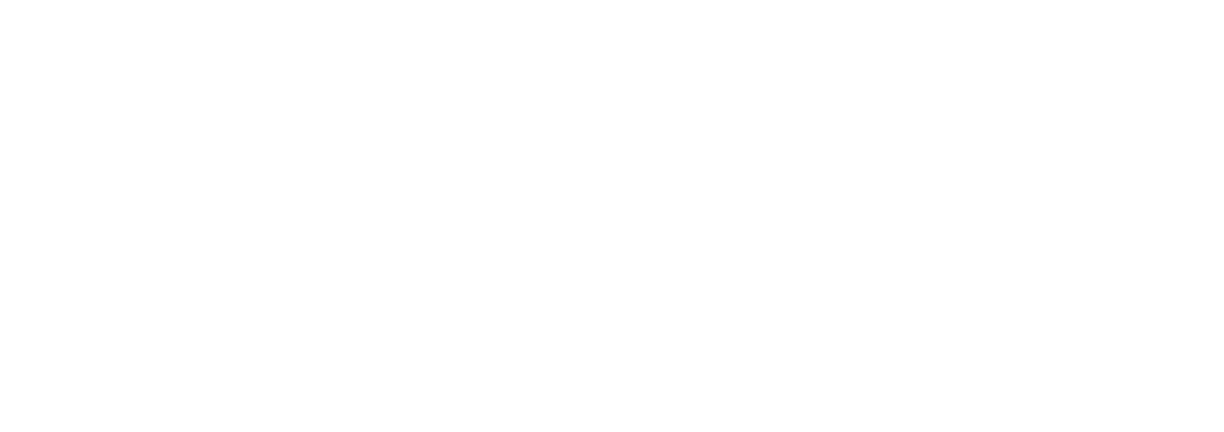