Read more on the labor crunch: https://plasticsmachinerymanufacturing.com/21248002/.
By Karen Hanna
For custom molder Jesco Molding Inc., the impetus for investing in a new model of worker came in the form of mismatched parts.
“It’s a different type of robot,” said James Schoudel, VP at the Sandy, Utah, company, which recently doubled its portfolio of automation equipment by purchasing a W818 robot to go along with a Primus 14. Like the Primus 14, the W818 will pick and place parts. Both three-axis robots are from Wittmann Battenfeld.
“It does more. It lifts more weight, for one. Then, I think it’ll lift around 22 pounds versus like the 5-pound payload,” Schoudel said.
Compared to flesh-and-blood employees, robots don’t confuse one component with another when putting together intricate assemblies, like those Jesco supplies to the dental industry. They also don’t miss work, call in sick or dally at the water cooler. For all the things they don’t do, some processors are adding another: Robots don’t have to replace workers. They can make workers — and work — better. Optimizing automation technologies could help companies find and retain humans to work alongside them.
To serve humans
In the imaginations of sci-fi writers, robots take jobs, then lives as they move inexorably toward total domination.
But that’s not how automation expert Will Healy III sees it.
“These kinds of technologies are part of the HR strategy,” said Healy, who, as the marketing manager for the Americas for industrial automation supplier Balluff, speaks at conferences about the importance of automation. “How can we invest to make the life of the worker easier?”
A self-described “automation evangelist,” Healy blames much of employers’ challenges in finding workers on demographics, as millions of baby boomers retire each year in a “silver tsunami.”
According to the Social Security Administration, the number of Americans 65 and older will increase from about 57 million in 2021 to about 76 million in 2035. Currently, there are 2.7 workers paying into Social Security for every one beneficiary. By 2035, that ratio will decline to 2.3 to one.
Healy contends not all older workers want to leave the workforce.
“A lot of the jobs we have people doing are very physically demanding, right?” Healy said. “They’re lifting parts and loading a cell. They’re moving parts around all day. So, with boomers, I would like to talk about, how can we extend their careers? How can we use technology to make the work that boomers are doing, the physical part of it, easier?”
He recounted the struggles he and his wife recently experienced trying to find carpenters for a home project.
“We wanted to redo our kitchen and our master bathroom. Our master bathroom’s on the second floor. And the guy who did our kitchen, I asked him, ‘Will you quote our bathroom?’ And he said, ‘My workers refuse to do any work on the second floor of a house,’ ” Healy said. “Because all these guys are over 50.”
To help accommodate older workers’ needs, Healy said employers should take stock of the tasks on the plant floor and find ways to optimize workers’ brainpower over brawn.
“We can invest in technology, like a cobot to do machine tending. Then, we can have one worker running three machines, setting up the machines and using their brain to solve problems, and they’re not doing the physically tough part of loading and unloading a machine all day,” Healy said.
Considering the cost and time involved in finding and training new workers, an investment in automation could quickly realize value — both for employers and for aging workers presented with the opportunity to stay on the job.
“It can take you months to find a replacement of that skilled machinist or whoever. ... And what if you talked to him in the exit interview, and he’s like, ‘The job’s just too hard; I really can’t do it anymore.’ What if you said, ‘Hey, man, will you stick around and we’ll get some cobots?’ They probably would do that. They’re probably just retiring because they’re tired,” Healy said.
“Most of the people that I talk to want to work. They’re just too tired.”
Meeting employees’ expectations
New, younger workers entering the workforce bring with them expectations honed by growing up in a data-at-your-fingertips culture, Healy said.
Unfortunately, in his experience, that’s not the environment many workplaces offer.
At conferences where he has asked participants about the age of their machines, Healy said he has found anywhere from 10 percent to half of people report that their companies have machines that began operation in time to see FDR in office; every plant has some machine from the 1970s.
“Most of these kids are getting phones at nine, 10 years old. They expect technology, and so if the last big investment you made was in 1970, they’re not going to want to work for you,” Healy said.
He acknowledged investing in technology is expensive, and if not done strategically, can be counterproductive.
To get the most bang for their buck, Healy said companies should consult their workers on the floor, to see how to prioritize their technology projects.
“People know your problems. The operators know the things that are most painful, the line supervisors know the things that are most painful. Find a problem, and then try to figure out what will solve that. Just a process improvement? Is it a people training problem? … And then is it a product? Do we need a technology to solve it?” he said.
For him, automation planning comes down to a series of questions:
How do we get faster onboarding?
How do we shorten the time when a new product is rolled out to the production line to get everyone able to do it?
How do we get rid of ergonomic problems or issues that lead to workers’ compensation claims?
How do we bridge the skills gap, rather than replace workers?
Robots at work
Jesco isn’t only the plastic parts maker investing in automation. The hiring market for robots is hot.
“We are trying to automate many of the tasks that are repetitive and utilize our labor for the truly value-added tasks,” said Matt McDermott, director of operations at Champion Plastics Inc., Auburn Hills, Mich.
According to the Association for Advancing Automation (A3), a trade association for the automation industry, global robot sales in the third quarter of 2021 hit record highs, with nearly 29,000 units valued at $1.48 billion sold. The numbers represent increases of 5.8 percent and 0.5 percent, respectively, over the previous records set in 2017, and 37 percent and 35 percent, respectively, over the same period in 2020.
In North America, third-quarter sales represent the third-highest number of units and fifth-highest unit value, A3 said.
A3 President Jeff Burnstein attributed much of the growth to labor shortages.
According to the World Robotics 2021 Industrial Robots report, available from the International Federation of Robotics, a record 3,014,900 industrial robots were operating in factories around the world in 2020 — an increase of 10 percent over the previous year. In the U.S. manufacturing industry, there 255 robots for every 10,000 workers, compared with 126 in the world generally.
The federation, which like A3 represents the robotics industry, expects growth in the industry to continue into 2022 and beyond at rates in the low double digits.
That has been good news for robot makers, like Universal Robots (UR), which reported its cobots brought in record third-quarter revenues of $78 million — an increase of 46 percent over last year.
“Almost everywhere we operate we see the manufacturing sector facing considerable challenges — such as workforce shortages and supply chain disruption — which can be tackled through the use of collaborative automation,” UR President Kim Povlsen said. “Post-pandemic, we also see businesses more open to questioning the way they work, looking for opportunities to make their businesses more resilient and improve the working lives of staff.”
Implementing technology solutions
At Plastics Unlimited, like Jesco, new technologies are helping to absorb problems stemming from the labor shortage.
Co-owner Dakota Kieffer said the Preston, Iowa, thermoformer has worked to update and standardize its equipment, an effort that has simplified training. It also has invested in a robot, so that people working on the first and second shifts can be more productive, helping the company compensate for problems it has had finding night workers.
The company, he said, is investing “half a million dollars a year on new thermoformers that are more similar to our other newer thermoformers, [that] are easier to learn,” he said. “They save all the information that you need, [they’re] easier to access, easier to read, [with] easier setup, less training.”
The investment has made operators’ jobs easier — and increased productivity.
“All new equipment is much easier to set up and train on than stuff that was made 30, 40, 50 years ago,” Kieffer said.
Meanwhile, supply-chain problems are bogging down Jesco’s solution for its labor problems — five months since ordering its second robot, it was still waiting on delivery.
Karen Hanna, senior staff reporter
Contact:
Association for Advancing Automation, Ann Arbor, Mich., 734-994-6088, www.automate.org
Balluff, Florence, Ky., 800-543-8390, www.balluff.com
International Federation of Robotics, Hamburg, Germany, 49-408-22-44284, www.ifr.org
Universal Robots USA Inc., Boston, 844-462-6268, www.universal-robots.com
Karen Hanna | Senior Staff Reporter
Senior Staff Reporter Karen Hanna covers injection molding, molds and tooling, processors, workforce and other topics, and writes features including In Other Words and Problem Solved for Plastics Machinery & Manufacturing, Plastics Recycling and The Journal of Blow Molding. She has more than 15 years of experience in daily and magazine journalism.
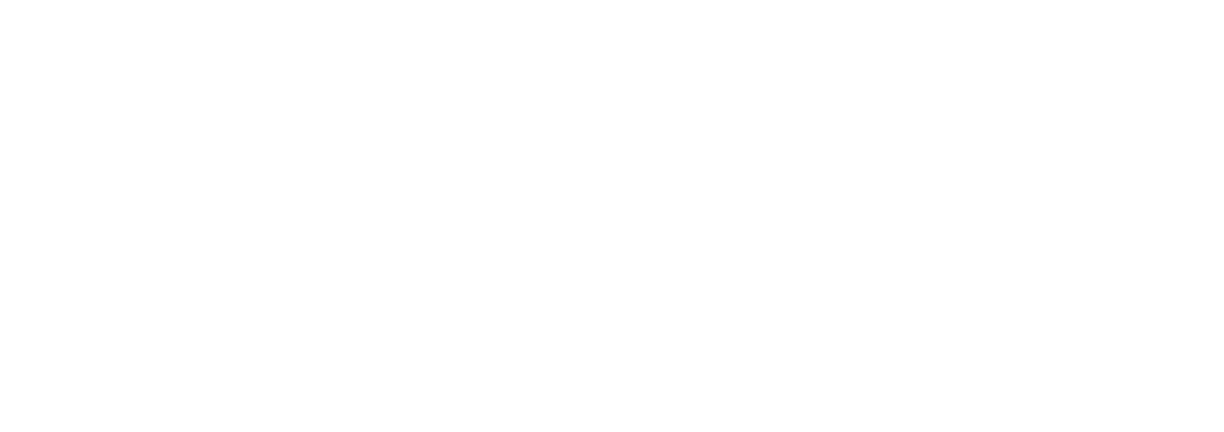