New center to promote smart manufacturing for small companies
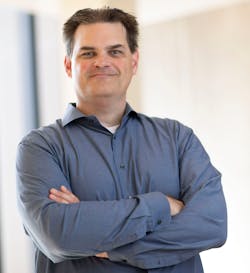
A Cleveland university will be the home of a new Smart Manufacturing Innovation Center dedicated to helping small- and medium-sized manufacturers (SMMs) in Northeast Ohio and across the country better understand and adopt smart manufacturing technologies.
The U.S. Department of Energy in partnership with the non-profit Clean Energy Smart Manufacturing Innovation Institute (CESMII) on Aug. 27 announced that Case Western Reserve University (CWRU) will host one of four new Smart Manufacturing Innovation Centers (SMICs) in the country.
The other new SMICs will be established at Penn State University, in University Park, Pa.; Purdue University, in West Lafayette, Ind.; and Feyen Zylstra LLC, an electrical services and industrial tech firm headquartered in Grand Rapids, Mich.
With the additional SMICs, the DOE will have established a total of eight nationwide. The centers offer specialized training and information to U.S. manufacturers wanting to implement smart manufacturing technologies to optimize their use of energy and materials.
“Smart manufacturing makes the American manufacturing sector more productive, energy efficient and competitive on a global scale,” Assistant Secretary for Energy Efficiency and Renewable Energy Kelly Speakes-Backman said in a press release. “DOE’s investments in smart manufacturing will accelerate the adoption of those technologies and processes, while developing a highly skilled manufacturing workforce for the future.”
Smart manufacturing is a broad term for an approach that uses technology and internet-connected machinery to monitor production, automate operations and use data analytics for more efficient and safe manufacturing.
The Cleveland-based SMIC will focus on SMMs since more than 70 percent of all manufacturing workers in the U.S. are employed by SMMs, and Northeast Ohio has more than 7,000 such companies, according to Team NEO, a business and economic development organization focused on Northeast Ohio job creation.
“Based on conversations with our partners, including MAGNET [the Manufacturing Advocacy and Growth Network] and Team NEO, we decided to focus on small- to medium-sized manufacturers,” said Nick Barendt, executive director of the Institute for Smart, Secure and Connected Systems at CWRU, who will direct the new SMIC.
“Part of the goals overall for CESMII, the DOE institute that we’re receiving funding from, is to drive adoption of smart manufacturing or Industry 4.0, whatever you want to call it, across the continuum of companies and manufacturers from OEMs to SMMs. We know many of them are not as far along with their Industry 4.0 adoption as we would like to see from a regional or national competitive standpoint.”
Many large manufacturers have been adopting smart manufacturing technology for years. However, many SMMs have barely begun the transition, due to limited technical staff and capital budgets. SMICs aim to help smaller companies address those concerns.
“Addressing these limitations requires a multi-pronged approach, from building awareness to education at all levels and the development of new, innovative ‘right-sized’ manufacturing solutions,” Barendt said. “This SMIC project is a direct result of years of collaboration between academia and the public and private sectors in Northeast Ohio.”
Outreach, assessment and examples
The Cleveland SMIC will bring together several partners including the university, the IoT Collaborative (a partnership between CWRU and Cleveland State University), Team NEO’s Smart Manufacturing Cluster, MAGNET and Bennit AI, a company building artificial intelligence solutions for manufacturing.
The Cleveland SMIC will help build awareness in the business community about smart manufacturing and will partner with Team NEO to offer online assessments that help companies develop a sense of their readiness to adopt smart manufacturing technologies.
“There is an outreach component and an assessment component,” Barendt said. “Then we’ll be doing some work with MAGNET, and MAGNET will be working with companies and doing some co-investment to help them begin smart manufacturing pilot programs. We’ll also be building some manufacturing exemplars [demonstrations] on the campus at Case to be housed within the Sears think[box].”
The Sears think[box] is housed in a seven-story, 50,000-square-foot facility at CWRU and is an innovation center, makerspace and entrepreneurship ecosystem that welcomes thousands of visitors each year. It includes fabrication and machining equipment, 3-D printers and laser cutters, milling machines, arc welders and other equipment.
The Cleveland SMIC will also demonstrate smart factory software that can collect data from machinery.
“There’s a software and technology component to this as well,” Barendt said. “There’s a smart manufacturing platform that CESMII has developed that is sort of a Switzerland of software automation systems supporting the integration of various data streams and visualizations within a factory. We’ll be integrating with that for demonstration purposes.”
That data could then be fed into a manufacturing data system, such as manufacturing execution system software.
Many SMMs have been hampered in adopting smart factory technologies because of their limited IT and OT staffs and the complexity of collecting data and integrating it into software that can analyze the data and provide predictive maintenance, quality control and inventory management benefits, for example.
Most smart manufacturing solutions are not well-targeted to SMMs, Barendt said. “If you’re an OEM, you can invest relatively large amounts of capital in automation, improved sensing, better quality control, better inventory management, supply chain, etc. The SMMs don’t always have that option. I think we’re seeing some of those technologies move downstream a little bit in terms of lower cost investments, and certainly more turnkey systems where you don’t need a software development team on staff, and you can buy more of the equipment and the solutions off the shelf.”
Predictive maintenance optimizes uptime
Although adopting smart factory technologies can pose a challenge to SMMs, there are numerous potential benefits, including increased productivity and quality control, Barendt said.
“Clearly, predictive maintenance is one common theme,” he said.
Adopting predictive maintenance can reduce equipment downtime by moving from an hours-of-operation or “odometer” model to one that’s based on equipment data. Standard preventive maintenance that relies on a calendar-based system tends to be very conservative in terms of when a piece of equipment should have routine maintenance, such as lubrication or changing bearings, Barendt said.
Predictive maintenance tends to optimize equipment uptime and allow for better management of downtime. It relies on data such as the vibration of bearings or measured wear on cutting components.
“There’s obviously lots of opportunity on the quality-control side of things, whether that’s deploying optical cameras and machine learning to look at parts coming out of the system or other modalities of sensing, whether it’s temperature or pressure or non-visible spectrum or ultrasound, and integrating that into your overall workflow,” Barendt said.
SMMs may believe smart factory technology isn’t important for them, but adoption may become essential for them to remain competitive, Barendt said.
“I think the reality is, these SMMs are going to be forced one way or another, to begin adopting some of these technologies just to remain globally competitive, whatever supply chain they’re in, whether it's automotive, or military and aerospace, medical equipment, consumable package, consumer packaged goods, whatever,” Barendt said.
“So, they need to be having conversations with their integrators and suppliers to talk about the kinds of problems that they’re dealing with, and what the options are for them to start deploying some technology. Clearly, there are lots of companies and organizations trying to move this forward, and it’s clearly a priority for the Congress and the Biden administration.”
Barendt said he expects more federal and state resources will be dedicated to helping manufacturers remain competitive, create jobs, keep more manufacturing in the U.S., and make local supply chains more robust.
Contact:
Clean Energy Smart Manufacturing Institute, Los Angeles, 888-720-8096, www.cesmii.org
The Institute for Smart, Secure and Connected Systems, Case Western Reserve University, Cleveland, 216-368-4477, https://case.edu/issacs
Bruce Geiselman
Senior Staff Reporter Bruce Geiselman covers extrusion, blow molding, additive manufacturing, automation and end markets including automotive and packaging. He also writes features, including In Other Words and Problem Solved, for Plastics Machinery & Manufacturing, Plastics Recycling and The Journal of Blow Molding. He has extensive experience in daily and magazine journalism.
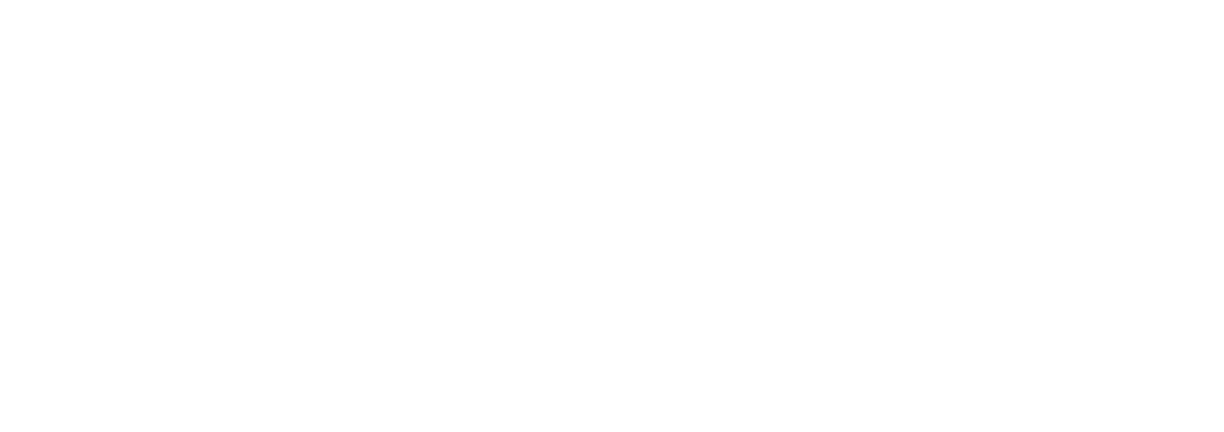