Dri-Air introduces trade-in program for its dryers
By Karen Hanna
The feeling of trading in a used car for a gleaming new one is now available to purchasers of Dri-Air's dryers.
In partnership with a supplier of used auxiliary equipment, Dri-Air has set up a new program, called Trade Up, to allow customers to put the value of their older dryers toward the purchase of new machines. The company’s newest drying technology, a closed-loop, dry-air recirculating system, targets PET and other amorphous resins.
Available to owners of dryers from any supplier, TradeUp is part of Dri-Air's efforts to help customers upgrade aging machines. According to the company, it can no longer supply new control components for more than 5,000 of its dryers currently in operation.
With TradeUp, dryer buyers can get a reduction on the cost of a new dryer — and benefit from new technologies that improve communications and energy efficiency.
To determine an existing dryer’s value, Dri-Air requests the serial number of the unit and photos, including pictures of the inside of the control box. It also needs to know whether the dryer is functional, where it is located and whether it can be loaded onto a truck. If applicable, potential buyers should provide details about loaders or receivers that are attached to the dryer.
Upon receipt of the information, Dri-Air will provide the prospective customer with a quote for a new dryer that reflects the deducted value of the trade-in. Dri-Air covers the costs and logistics of shipping the new dryer and removing the old one.
In addition to the new purchasing program, Dri-Air recently announced a new dry-air recirculating system for its hopper banks, intended for drying multiple batches of resins for short runs. With the new system, users can crystallize resins in some hoppers while drying already crystallized resins in others. This approach saves time and work.
Karen Hanna, senior staff reporter
Contact:
Dri-Air Industries Inc., East Windsor, Conn., 860-627-5110, www.dri-air.com
Karen Hanna | Senior Staff Reporter
Senior Staff Reporter Karen Hanna covers injection molding, molds and tooling, processors, workforce and other topics, and writes features including In Other Words and Problem Solved for Plastics Machinery & Manufacturing, Plastics Recycling and The Journal of Blow Molding. She has more than 15 years of experience in daily and magazine journalism.
Request More Information
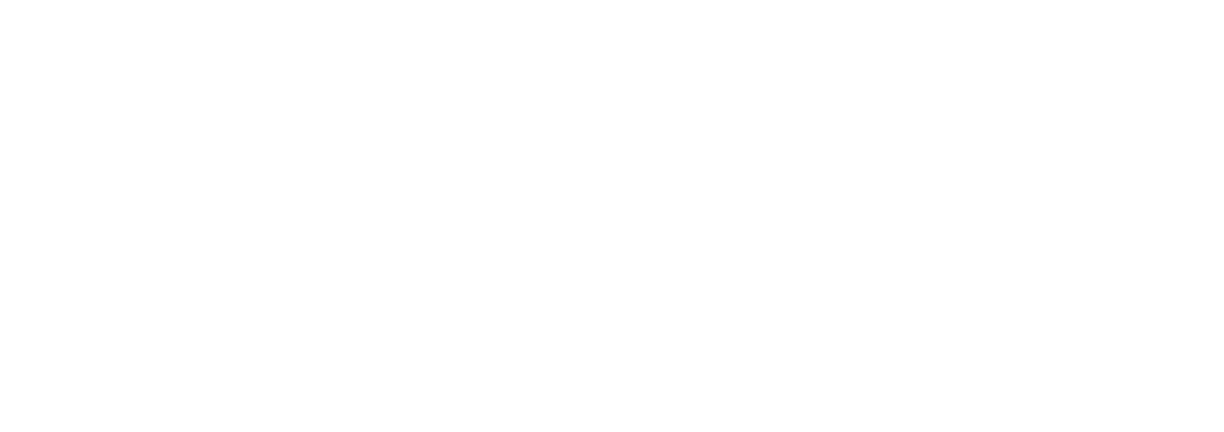