Problem: An automotive parts maker needed to produce a part for a niche option on Ford Super Duty trucks.
Solution: Additive manufacturing enabled quick production of the low-volume part, with a quality similar to injection molding.
By Karen Hanna
In commercials, muscular new Ford trucks conquer the frontier with horse trailers and fishing boats bouncing along behind them.
But not all new Ford buyers need to haul other vehicles, and for those who don’t, Ford had to find a cost-effective way to produce a very niche accessory package — a no-tow cap that seals away the powerful pulling capabilities of its heavy-duty trucks.
Enter 3-D printing.
“Most trucks have a trailer tow package, and basically, it’s what you plug your trailer into. If your vehicle does not have this option, this connector needs to be protected, needs to be sealed from the environment,” said Jerry Rhinehart, manager of additive engineering for Aptiv PLC, a mobility-technologies manufacturer based in Dublin.
Holding the plug-like connector, Rhinehart stars in a web commercial to discuss how his company partnered with Fast Radius Inc., a Chicago-based contract manufacturer that offers a variety of 3-D printing services, to make the unique part, using printers from Carbon Inc.
“Fast Radius and Carbon enabled us to additively manufacture Ford’s trailer-tow connector cap, greatly improving our time to market over traditional injection molding and paving the way for future innovations in our lower-volume part production,” Rhinehart said.
John Nanry, co-founder and chief manufacturing officer of Fast Radius, said 3-D printers are an ideal technology for producing injection molded-quality parts at small volumes that make the costs of tooling impractical.
“We found that we’re really helpful from that prototype through mid-volume production, that’s where we really played best,” Nanry said.
On the manufacturing stage, 3-D printers are adept at improv.
To guarantee it could withstand external elements, the cap needed to meet the automotive industry’s standard engineering and quality requirements. A small part, it required precision— a quality guaranteed by the injection molding machines that make a lot of the trucks' higher-volume parts.
Carbon’s Digital Light Synthesis (DLS) technology, which uses ultraviolet light to cure light-sensitive liquid plastic resin into solid parts, met Aptiv’s expectations for fast, reliable and scalable production.
Aptiv worked with Carbon to select a material for the job — Carbon’s EPX 82, a durable, high-strength epoxy-based engineering material with mechanical properties comparable to lightly glass-filled thermoplastics.
Having selected the technology and resin, Aptiv turned to Fast Radius for its help optimizing the part for manufacturability. Using its proprietary software, Fast Radius devised a way to optimally position the parts on the printer’s build plate to account for subtle variations in temperature and light.
Flexibility was key, Nanry said.
“True-on-demand production without any buffer is challenging. With a highly demanding automotive customer, you don’t want to be late. We do maintain a small amount of buffer inventory, but it's very small, on the order of maybe one week of production or something like that, to enable us to meet any unexpected demand. … Because this manufacturing platform is fungible and we don’t really have tooling, we can switch over and start producing these parts whenever we have machine capacity,” Nanry said.
He broke down the other benefits:
“On the economics front, it’s a low-volume part by automotive standards, which is tens of thousands a year, that quantity. It would not be economical to mold. The second is speed: We were able to work with Aptiv to reduce the time to market by 20 weeks versus injection molding, so they were able to get this part to market a lot faster.
"... The Carbon DLS process in particular is highly suitable for small, complex parts.”
For Aptiv, which had no previous experience using 3-D printers to make plastic automotive parts, the technology put the project in gear.
“We were able to reduce 50 percent out of the cycle time. We needed to get a solution to the customer as fast as possible, and this allowed us to do that,” Rhinehart said.
Karen Hanna, senior staff reporter
Contact:
Carbon Inc., Redwood City, Calif., 650-285-6307, www.carbon3d.com
Fast Radius, Chicago, 888-833-4543, www.fastradius.com
Karen Hanna | Senior Staff Reporter
Senior Staff Reporter Karen Hanna covers injection molding, molds and tooling, processors, workforce and other topics, and writes features including In Other Words and Problem Solved for Plastics Machinery & Manufacturing, Plastics Recycling and The Journal of Blow Molding. She has more than 15 years of experience in daily and magazine journalism.
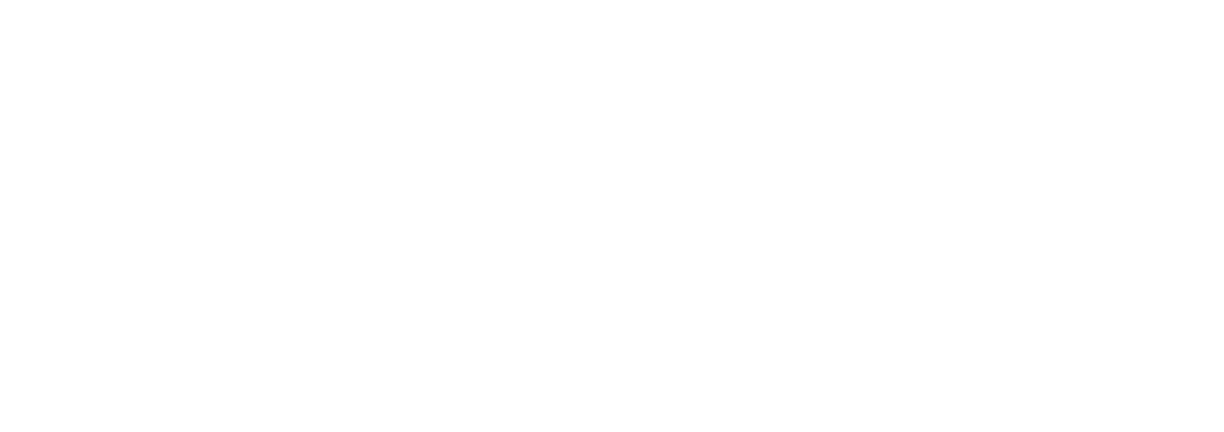