By Karen Hanna
Processors struggling to source and pay for resin might need a little patience.
“It is a difficult situation and one that is most likely going to continue for, I'm going to say, at least early summer,” said Esteban Sagel, a principal at Chemical and Polymer Market Consultants, which tracks the materials market.
Over the past month or so, prices for some resins have doubled; in some cases, they’ve nearly tripled since last year. Ask Sagel what’s going on, and you’ll get a response familiar to social media users: It’s complicated.
“We have been having issues that have slowly evolved throughout the last 12 months,” Sagel said. But a winter storm emergency that crippled Texas’ power grid in February was “the straw that broke the camel’s back,” decimating U.S. resin-making capacity.
Like many of the supply-chain issues that have bedeviled the global economy over the last year, the resin supply problems have their roots in the COVID-19 pandemic. Initially, amid shutdowns, demand for many products plummeted. Then it roared back.
September update: Ida roils resin markets again
Compared with non-pandemic years, demand throughout 2020 was “confusing,” Sagel said. Early in the crisis, the health-care industry mustered into action and consumers stuck at home stocked up on essentials. By the summer of last year, demand for plastics goods was trending up — but efforts to ramp up plastics production would soon face a number of obstacles, including the scuttled opening of a PE plant in Mexico due to administrative issues.
The Gulf Coast, where 80 percent of the polymers used by the U.S. injection molding industry are made, also weathered a couple hurricanes.
“It was just piling up one thing after the other after the other,” Sagel said.
Texas’ experiences with hurricanes has primed resin manufacturers for managing planned shutdowns. Most storms affect localized areas, allowing producers elsewhere to carry on operations. None of that was the case, though, in February, when much of the state was plunged into darkness.
The resulting chaos was like a hurricane — but for resin manufacturers, it left a wider and deeper swath of damage.
“If you picture those big production facilities, they are quite complex. And if you want to stop production at any one of those facilities, you have to go through a certain process in order to do that,” Sagel said. “You can’t just stop, but that’s what happened. We actually suddenly stopped from one moment to the next. That damaged equipment and caused problems not just in the polymer production, but also in the units that manufacture the raw materials for polymers, as well.”
Returning to normal is a bit trickier after the February storms than following a hurricane, he said.
“My opinion is that it’s going to be harder to rebound from than, say, with the hurricane that impacts just a single area of the industry, rather than the whole state at the same time,” he said.
Equipment damaged by improper shutdowns or unpredictable power availability is not easy to replace.
“Some had to be replaced, some need to be repaired, and those are not things that are sitting on the shelf. You cannot just go and buy a compressor. You have to order them, and they take time to be delivered. So, the problem that we have is that the supply issues are likely going to continue for a somewhat extended period of time,” he said.
Shipping issues that have plagued the globe — with ships backed up at ports waiting to be unloaded, creating a scarcity of empty shipping containers — exacerbate the problem. This means processors are hard-pressed to order resin from elsewhere, while Gulf Coast resin manufacturers struggle to source replacement equipment.
In some cases, Sagel said, U.S. resin manufacturers have cut down on the amount of resin they’re exporting. That will help capacity here.
"The way that you get out of this issue is definitely solving the supply problem. So, as the producers fix their raw material plants and increase their production rates, and PVC, polypropylene, polyethylene ... we’re going to start seeing some reductions on their supply problems,” he said.
Karen Hanna, associate editor
Contact:
Chemical and Polymer Market Consultants, Houston, [email protected], www.chempmc.com
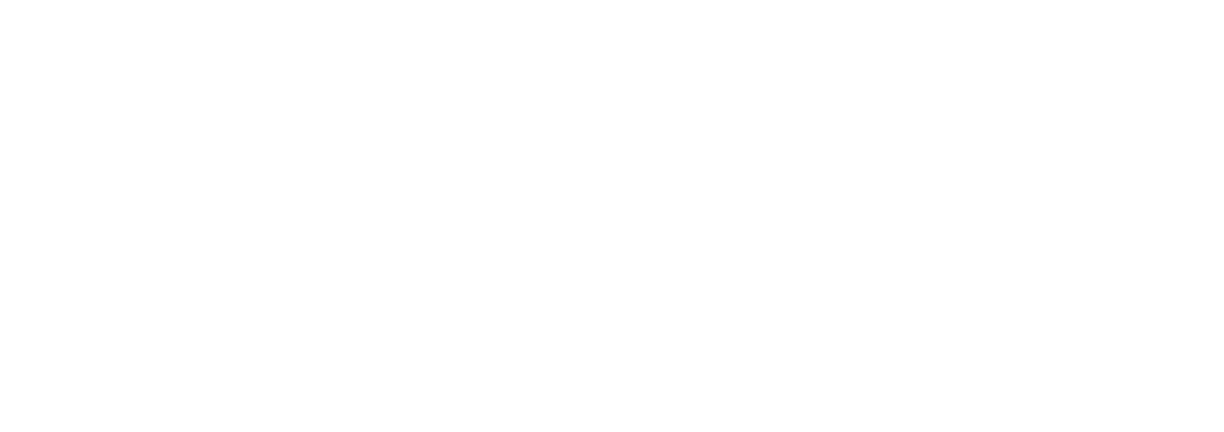