As autumn rolls in, so does the potential for severe weather systems across the country. The Southeast prepares for the second half of hurricane season, as drought conditions increase the likelihood of an extended wildfire season in the West. But any severe weather — including thunderstorms, tornadoes, snow, hail and ice — poses a threat to your personal safety, as well as the safety of your plastics business and employees. It’s no wonder why National Preparedness Month is recognized each September.
As your business adjusts its operations and workflows to meet the changing demands of 2020, it’s more important than ever to ensure your safety protocols also include new emergency action plans for severe weather events.
As national safety consultants for Sentry Insurance, we’ve helped businesses across the country plan for all types of extreme weather. No two businesses or facilities are alike, so it’s important to consider your unique operations — and what kind of severe weather risks are most common in your area — before finalizing any processes or procedures. What follows are some general recommendations and considerations we’ve compiled to help guide your plastics business during safety planning. Taking the time to thoughtfully prepare your emergency response may be one of the most important investments you’ll ever make.
Assess from the outset
You’re probably well aware of your region’s typical weather-related threats that may impact your business. But the dangers of severe weather don’t stop at damaging winds or flooding. Weather itself may be the catalyst for secondary threats, from fires and explosions to the risk of electrocution and toxic gas inhalation. Particularly when dealing in petroleum-based product manufacturing, it’s important to consider all potential threats.
- Major risks: Determine the most probable types of weather-related events and the responses you’ll need to prepare. If your business is likely threatened by tornadoes, how will you plan to keep employees safe within your facility? If you’re more likely to face dangerous fires, how will you quickly guide your employees to safety?
- Facilities: Knowing all the details of the space or spaces your business inhabits is critical in developing an adequate emergency response. Account for all exits — not only doors and windows that would make for an ideal escape, but secondary ones as well, in case your employees can’t reach the primary exits. Also be aware of what equipment may pose potential obstacles to making a safe exit, and what areas are best suited to protect employees if indoor conditions are deemed safer than outdoors. Finally, remember the immediate surroundings of your facility. Are there fences or other obstacles that could impede an emergency exit? Is there a designated area to ensure employee safety outdoors?
- Materials: Assess potential hazards caused by the petroleum-based products your business houses. Minimizing the risk of explosion or toxic inhalation is as important as the primary physical dangers posed by extreme weather. Consider how chemical processing and storage may affect areas that are otherwise safe for emergency occupancy, and take inventory of all your facility’s flammable liquids.
- Communications: Think about what systems are in place to immediately notify employees in the event of an emergency. As different threats require different responses, it’s important to differentiate alarms and alerts so your employees are instantly aware of the steps they need to take to stay safe. How will you communicate danger to those employees who are not in the facility? Do you have plans in place to alert employees who are blind or deaf, or have other disabilities? Does your plan account for potential power outages?
Collaborate and communicate
An emergency action plan requires effective communication and engagement to keep all employees in the know about how to respond when severe weather hits. Plans should be detailed in writing and easily accessible across your work environment. Better communication — rather than relying solely on a written document — makes for a more effective plan.
- Leadership: Developing and implementing an emergency preparedness and response plan requires effective leadership. Designating an emergency coordinator is helpful but having more than one person involved in planning emergency action promotes a shared understanding and ownership of the plan itself. With so much to consider — and so much at stake — having more perspectives at the table can also lead to better preparedness.
- Training/onboarding: An effective emergency action plan not only takes time to develop, it takes time to communicate. Once the plan is finalized, it’s critical to actively engage all employees in the plan itself. Apprise all staff — spanning all shifts, titles and duties — of the detailed plans and describe how they’ll be notified in the event of an emergency (remember, your alert system should be a central part of the plan itself). Given the nature of plastics manufacturing settings, new employees should also be informed of emergency protocols as part of their onboarding process.
Stay vigilant
A phrase we often use in safety planning is, “How you practice is how you play.” You can know an emergency plan like the back of your hand but running through scenarios with your employees helps prepare them in the moments that matter.
- Practice: Conducting regular emergency drills is critical. Drills should be timed to measure response efficiency, and occur every six months, or when plans and procedures change. In the same way that all employees should receive regular communication about emergency response procedures, drills should also be conducted for every shift, to help ensure safety around the clock.
- Emergency response: In worst-case scenarios, weather-related disasters can make it difficult or impossible for first responders to reach employees in danger. Your business should ensure that it has emergency equipment on hand, such as first aid supplies, functional automated external defibrillator (AED) machines and fire extinguishers — and that employees on every shift are trained to use them. You may also invite first responders to conduct their training at your facility, allowing them to practice their skills and get an inside look at your facility, which may help accelerate an emergency response.
- Regular maintenance: When it comes to regular facility maintenance, potential emergencies should always be a determining factor. Keep your facilities clean and orderly to avoid unanticipated obstacles, dangerous spills or contaminants, while also checking spaces for emergency preparedness as part of each inspection schedule. It’s also important to update sprinkler and ventilation systems whenever you change manufacturing materials and processes. This will help extinguish flames and reduce the spread of toxins.
There’s far more to emergency response than can be summarized in a brief article, but there’s no better time to begin assessing — or developing — your business’s emergency action plan than National Preparedness Month. The guidance above, along with that provided by OSHA and U.S. Department of Homeland Security, could help you avert a potential business disaster.
Sentry provides insurance, retirement and safety services for dealerships and businesses. You can reach the authors at [email protected] and [email protected], or visit sentry.com to learn more.
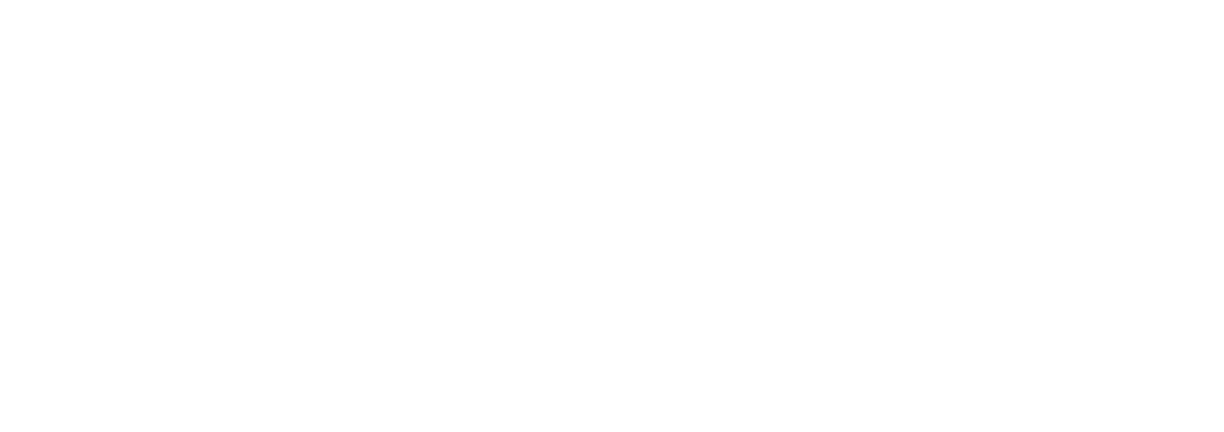