Problem: An company wanted to secure new business that involved two-shot injection molding, but did not want to invest in a dedicated two-shot injection molding machine.
Solution: The processor purchased an all-electric Nissei NEX IV press and a Mold-Masters E-Multi injection unit to attach to the new press to provide two-shot molding when needed.
Plastics processors need to be wise when making capital investments to expand their capabilities. Spending investment dollars on machinery that’s dedicated to a single process, such as two-shot injection molding, might fix a short-term problem but create long-term misery if enough work can’t be procured to keep the single-process equipment running.
That’s what Joe Vest, VP of engineering at Bright Plastics, was thinking about when he contemplated new business for the custom injection molder. The company manufactures components for a wide variety of industries, including the medical, heavy truck, aerospace, military, industrial, outdoor recreation, entertainment and telecommunications fields.
The plant has its own mold shop, on-site tool room and an automation lab for manufacturing custom parts. Its presses range from 40 tons to 1,550 tons. It has 31 injection molding machines at its corporate manufacturing center and headquarters in Greensboro, N.C., and 10 injection molding machines and an extrusion line at its manufacturing and logistics hub, which also is in Greensboro.
“We've always done overmolding, but we've always done it with two molds, where we mold the base part and then mold the overmold on top of that in a separate mold,” Vest said. “For years, we've wanted to have a dedicated machine to do regular two-shot molding, but we've never had a job that had enough volume that would justify the expense.”
He was concerned that investing in a two-shot injection molding machine might produce short-term gains that could turn into long-term pains if the two-shot molding business was not sustainable.
“There are several manufacturers that make great two-shot presses, but they are expensive machines and are generally dedicated to two shots,” Vest said. “You can’t turn that second shot off and run it as a single shot.”
That’s why he considered other options.
“We liked the idea of getting a base Nissei press and the E-Multi unit because we could take the E-Multi to another machine in the future if we had another job that needed a little bit bigger machine,” he said. “We could just move the E-Multi to another size machine.”
The company purchased an all-electric 140-ton Nissei NEX IV series press and auxiliary equipment, including a Mold-Masters E-Multi injection unit, a Wittmann Battenfeld robot, a Matsui dryer and two AEC thermolators, for approximately $250,000.
The E-Multi injection unit was attached to the Nissei press to make a part for a company in the video game industry. If that business went away, the E-Multi unit could be moved to other presses and the Nissei unit could be operated as a stand-alone, single-shot injection molding machine.
“This job was supposed to need only about 60 to 70 percent of the machine loading,” Vest said. “We planned on running medical products in there when it was not being used for its purchased purpose. We've only done that once for a few weeks because it's been running the two-shot molding job that we bought it for the whole time.”
Originally, Bright Plastics was going to be a secondary supplier to its two-shot molding customer.
“We were going to be a backup supplier, but because [of] the way that this press has performed, we've moved ourselves into more of a lead role as a supplier for them,” Vest said.
Bright Plastics started making products from its new equipment in July, he said.
“We ran non-stop from July until December,” Vest said. “We started up sometime in February, and we'll run probably again non-stop until late fall or early winter. The volume is more than what we initially contracted for and has kept us running.”
The decision to buy the Nissei press and the E-Multi injection unit was based more on expediency and practicality than cost, Vest said.
“When you start doing cost comparisons, adding an E-Multi to a base machine or buying a two-shot machine, the pricing really isn't that different. But the lead times are,” he said. “The lead times on a two-shot machine typically are in the months whereas we were able to buy a standard Nissei off the shelf that was in stock and bring it in a few weeks. I think the lead time on the E-Multi was longer than the lead time on the Nissei.”
The company already owned about 10 Nissei injection molding machines with similar controllers, so operators were familiar with the new press and how to operate it. It took only a few days to learn how to program and operate the E-Multi injection unit, he said.
The robot handles almost all of the part movements. Machine operators make sure cold runners are separated from the parts before packing them.
Two-shot molding is more efficient and takes less time than overmolding, so parts cost less to produce, Vest said.
“The overall part price is cheaper with two-shot molding because you have the two-injection process happening at the same time in the same mold. After every cycle, a finished part comes out of the mold,” he said.
With overmolding, the base parts are molded and put in a box or taken by conveyor to another machine where the base parts are overmolded.
“When we do overmolding, typically an operator, rather than a robot, is going to handle the base parts and take them to the other press to do the overmold,” Vest said. “So, you’ve got two separate molding operations, with an operator moving parts between them.”
The company’s two-shot molding process uses a family mold with a total of eight cavities – four cavities make the base part and four cavities overmold the TPE on the base part. When the mold closes, the machine is molding four base parts and simultaneously overmolding the four base parts that were made in the previous cycle.
“The mold does not rotate so you have to get the four base parts that were molded into the other four cavities to overmold the TPE,” Vest said. “The robot moves the base parts from the first four cavities to the second four cavities. It also removes the four overmolded parts and delivers them to be packed. You can build a mold that will automatically rotate half of the mold to accomplish this, but our mold relies on the robot to move the parts.”
Bruce Adams, senior staff reporter
badams@plasticsmachinerymagazine.com
Contact:
Mold-Masters, Georgetown, Ontario, 905-877-0185, www.milacron.com
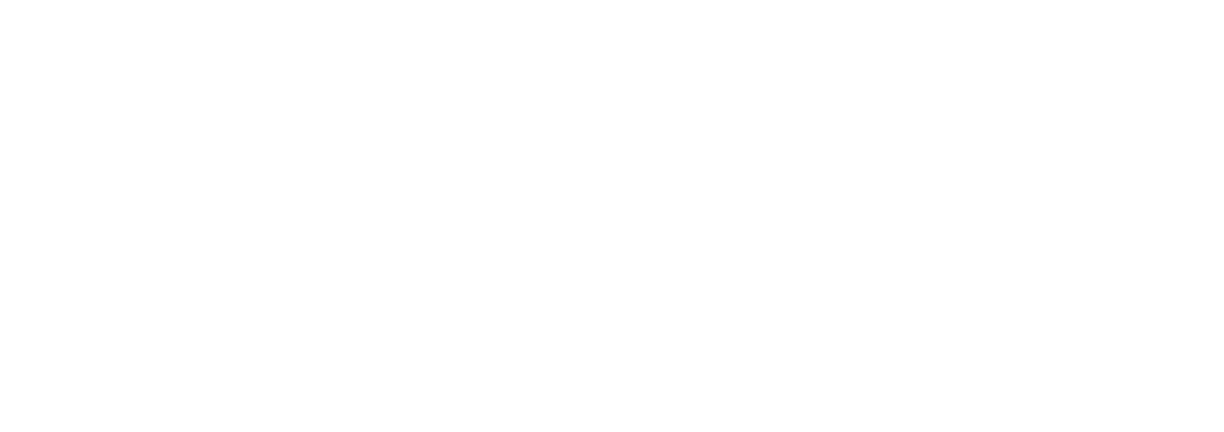