Contract manufacturers target high-volume production
Contract 3-D printing companies are embracing the latest technologies to bolster their ability to make large numbers of parts for their customers.
FORECAST 3D
Forecast 3D, a California provider of 3-D printing services, recently added two of HP’s new Jet Fusion 5210 Pro industrial 3-D printers. Designed to handle big runs, the machines will help Forecast 3D meet increasing demand for high-volume part production.
“It’s the next evolution of the [HP Jet Fusion] 4210 systems that we already have,” said Ken Burns, Forecast 3D’s technical sales director. “There are certain things that the 5210 can give us access to and capabilities that we don’t have on the 4210 printers, specifically around accessing more markets.”
In addition to faster print speeds, the printers will allow the company to use a new TPU, known as Ultrasint, developed by BASF.
“It’s about 30 percent faster,” Burns said of 5210 printers, compared with 4210 printers. If somebody is ordering 100,000 parts or a million parts, the speed becomes significant.”
“We have been leading the Multi Jet Fusion movement for the last two years, and, now, to keep up with business growth, we want to have the latest equipment and materials,” he said. Forecast 3D also provides injection molding services through a sister company.
3-D printing frequently is used to make prototypes, while injection molding and other long-established manufacturing methods typically have been used for high-volume production because of lower material costs and faster production speeds.
However, HP’s Multi Jet Fusion technology, used in Jet Fusion 5210 Pro printers, allows Forecast 3D to print parts quickly in four different materials. With the two new printers, the company now has 26 HP production printers and the capacity to print polyamide (PA) 12, glass-reinforced PA, PA 11 and TPU.
“Up until now, all of our digital manufacturing has been in rigid nylon polymers,” Forecast 3D President and CEO Corey Weber said. “With the introduction of this low-cost, 3-D printed TPU elastomer, we expect an increased amount of opportunities to come from the ability to achieve mass customization with a solution that can provide a softer custom interface with the body. Combining the comfort of an elastomer with the design freedom of 3-D printing will allow companies to engineer parts that can provide better impact performance as well as improved ventilation when using lattice-type structures.”
Examples of products that could benefit from 3-D printing with TPU include prosthetics, helmets, body armor, footwear, fashion and sports braces, he said.
“There are a few technologies out there that can print elastomeric materials or soft materials for prototyping, but the properties in them are typically only that, for prototyping,” Burns said. “They break down, they tear too easily, and they degrade too quickly because they are basically prototype-grade materials.”
However, the 5210 printer was designed to print with TPU, though it also can process other resins.
HP’s Multi Jet Fusion technology builds parts layer by layer. It applies fusing and detailing agents to a thin layer of powdered material that is then heated with infrared lamps, adhering an entire layer in a single pass. The process creates a part with more uniform strength than can be produced with a selective-laser-sintering (SLS) printer, Burns said.
“SLS is using a laser to, in layman’s terms, micro weld a part together, where the HP technology is fusing parts together with a combination of [infrared] lamps and their agents inside the printer,” Burns said. “You get a more isotropic part instead of having a significant drop in Z [axis] properties. There’s a molecular intertanglement that happens between each layer, so you create a different sort of bond between the parts. … This is, in my opinion, one of the biggest things that separates the HP technology from SLS or FDM [fused deposition modeling] or anything else. The properties in X, Y and Z are essentially the same.”
Ramon Pastor, global head of HP 3-D printing and digital manufacturing, said the company’s Multi Jet Fusion technology is faster and offers better material properties than traditional SLS technology.
“HP’s Multi Jet Fusion technology is built on decades of HP’s investment in inkjet printing, jettable materials, precision low-cost mechanics, material science and imaging,” Pastor said. “Through all of these, we have managed to deliver a technology that brings several advantages in economics, build speed and control over part and material properties that is beyond the capabilities of other 3-D printing processes.
“The way Multi Jet Fusion technology works is by jetting HP functional agents using HP printheads, which selectively fuse the plastic powder with energy,” Pastor said. “This part control and accuracy is executed at [the] voxel level. Voxels are volumetric pixels, the cubic unit that composes a 3-D printed object, and HP’s technology has the capacity to specify the properties of each voxel, defining a 3-D part point by point through a series of fusing and detailing agents.”
The addition of the two new printers comes as Forecast 3D sees greater demand among its clients for high-volume and serial production.
“We wouldn’t have 26 machines if it wasn’t happening,” Burns said.
Fusion 3D’s customers’ requirements range from prototypes to production runs of more than a million parts, he said.
Most of its customers are interested in one of three categories: product introduction, bridge manufacturing and serial production.
“We get a lot of customers that will do their initial product launch with 3-D printing because it’s a lower risk for them not to have tooling,” Burns said.
As part of a product introduction, Forecast 3D will print thousands or tens of thousands of parts. Those products often eventually transition to traditional processes like injection molding or machining when volumes increase to where it’s no longer cost-effective to use 3-D printing.
The second category of customer demand is bridge manufacturing. “This is where there’s been a change in a product once it’s already in manufacturing, and the new tools are not going to be ready for eight weeks, so they need parts for those eight weeks, just to keep the manufacturing lines going,” Burns said. “We’ve had some customers go over 100,000 units of single parts utilizing bridge manufacturing. … In terms of 3-D printing, I’d definitely say that’s high-volume.”
Serial production is ongoing 3-D printing for customers.
“We have several customers that do serial production,” Burns said. “We’ve been making some of these parts for almost two years for our customers. There is no plan to transition out of [Multi Jet Fusion] because the quantities are right and the price point [is right].”
Typically, Forecast 3D’s serial production customers are interested in production runs ranging from several hundred parts to more than 1 million parts annually.
Burns sees the growth of 3-D printing continuing as technology improves and new resins become available.
“More materials — I think that’s the biggest thing that’s coming that will further impact the industry,” Burns said. “Right now, we’re pretty limited on our material options, so we can only take a very small slice of a very big pie, and what I think will further move the industry is materials.”
PROTOLABS ADDS CARBON
Protolabs, a contract manufacturer that specializes in prototyping and low-volume production, has added Carbon Digital Light Synthesis (DLS) printers to its portfolio.
The Carbon M2 printers will allow customers to move into production faster and more cost-efficiently than ever before with 3-D printing, the company said. Protolabs didn’t disclose the number of Carbon printers it has, but said it has capacity to meet current demand and may add more machines in the future. In 2018, Plastics Machinery Magazine reported that Protolabs had more than 100 3-D printers overall.
“We recognize that market demand for additive manufacturing has moved beyond prototyping and is being leveraged to create fully functional parts at a much larger scale,” said Greg Thompson, Protolabs’ global product manager for 3-D printing. “We are committed to support that demand in a technology-agnostic manner so that our customers get the best possible parts from the best possible 3-D technology.”
Protolabs is one of the largest suppliers of custom 3-D printing services, producing more than 100,000 components every month across six different additive manufacturing technologies. Each of the technologies has different applications and benefits, the company said.
In addition, Protolabs performs injection molding, CNC machining and sheet metal fabrication.
“Being technology agnostic, it really allows us to look at the needs of our customers and offer the best solution for what they and their project need at the time,” Thompson said. “Often, that’s 3-D printing.”
Carbon’s DLS printers can print with photopolymers that have advanced properties, Thompson said. The printers work with resins that have mechanical properties similar to ABS and PC grades used in injection molding.
“Customers are looking to leverage the design freedom of additive manufacturing beyond just prototyping into their production applications,” Thompson said. “Now, it’s not our view that [3-D printing] competes with or will replace injection molding or CNC machining. It’s another tool that will augment the manufacturing choices that engineers and production managers have.”
Bruce Geiselman, senior reporter
Contact:
Carbon, Redwood City, Calif., 650-285-6307, www.carbon3d.com
Forecast 3D, Carlsbad, Calif., 855-406-4635, www.forecast3d.com/
HP Inc., Palo Alto, Calif., 650-857-1501, www.hp.com/go/3dprinter5200
Protolabs Inc., Maple Plain, Minn., 877-479-3680, www.protolabs.com
Bruce Geiselman
Senior Staff Reporter Bruce Geiselman covers extrusion, blow molding, additive manufacturing, automation and end markets including automotive and packaging. He also writes features, including In Other Words and Problem Solved, for Plastics Machinery & Manufacturing, Plastics Recycling and The Journal of Blow Molding. He has extensive experience in daily and magazine journalism.
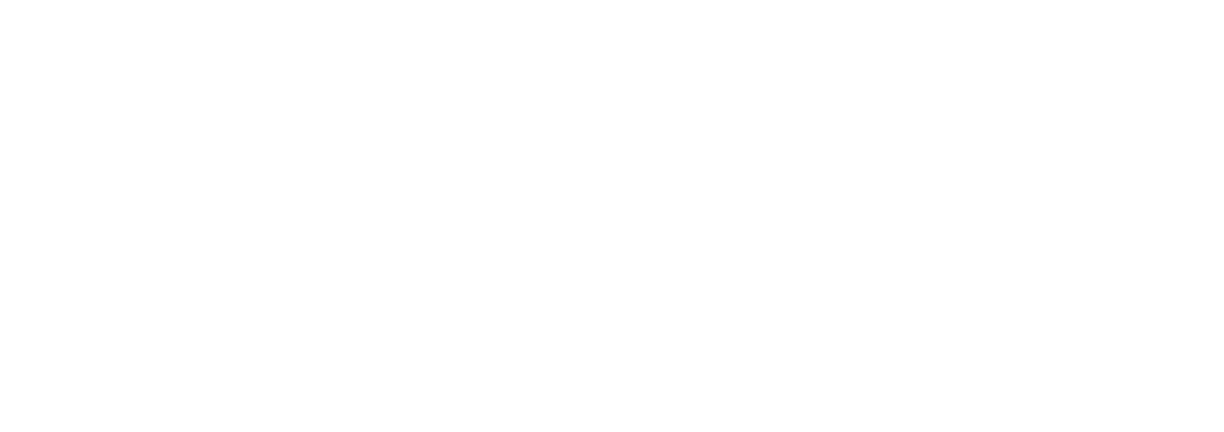