Carbon looks for growth in automotive, athletic equipment and dental fields
In an arrangement that demonstrates 3-D printing’s potential to disrupt markets typically dominated by injection molding, Ford Motor Co. continues to ramp up its use of 3-D printers from Carbon to produce parts. Carbon, the maker of printers that employ light to freeze light-sensitive resins, also is seeing its technology move into a host of other fields, including sports equipment manufacturing and dental device production.
Carbon and Ford announced their collaboration earlier this year, when Carbon unveiled a number of 3-D printed automotive parts, including an HVAC lever arm for the Ford Focus, auxiliary plugs for the F-150 Raptor truck and parking brake brackets for the Mustang GT500.
Ford is using Carbon M2 printers with Carbon’s proprietary Digital Light Synthesis (DLS) technology to print the parts from EPX 82 epoxy. Carbon’s EPX 82 passed Ford’s rigorous performance standards and met the carmaker’s demands for UV stability and resistance to interior weathering, fluids, chemicals, heat, flammability and fogging.
Carbon sees significant growth potential in the automotive market, said Erika Berg, head of application development at Carbon.
“We’ve been doing a lot of great work with partners like Ford,” she said. “Earlier this year, we launched the first 3-D printed parts on production vehicles with Ford. Normally, you know, 3-D printing has been used for prototyping parts. … We did years of material testing and validation in order to be able to release components in their vehicles that are now being sold to consumers. And that was a huge accomplishment in our partnership with Ford.”
PRODUCTION PARTS
A combination of faster printers, new resins and improved software is fueling increased interest in moving 3-D printing from prototyping to full-scale production, Berg said.
She pointed to a partnership between Carbon and Adidas for manufacturing midsoles for running shoes made by the German footwear giant.
While speed is important, so too is the ability to print parts that are acceptable to consumers and that have good mechanical properties and smooth finishes.
“That’s really what is enabling customers to be able to use our technology for final products, because we’re no longer focused on just prototyping and making visualizations of parts, we’re actually doing final properties that can actually be made and used by consumers,” Berg said.
Berg also foresees further growth for Carbon’s machines to manufacture sports equipment, such as bike saddles.
“We’re going to continue addressing the saddles and helmet market and seeing where we can provide improved performance and protection to our customers,” Berg said. “That means helmets across all sports, team sports and individual sports.”
Since the beginning of the year, Carbon has partnered with Riddell, a manufacturer of sports equipment, including helmets, to produce a 3-D printed lattice liner that is manufactured using DLS. The liners are customized to precisely contour to the athlete’s head.
Carbon also is looking at opportunities in dentistry.
“We’re also seeing incredible growth within the dental space,” Berg said. “We have the first FDA-cleared resin for dentures, and that’s a really great area where we’re seeing a lot of growth and will continue to grow in the coming years.”
Carbon and Dentsply Sirona USA, a manufacturer of professional dental products and technologies, earlier this year announced they would market a system for 3-D printing dentures.
In addition to agreements with Adidas, Riddell, Dentsply Sirona and bicycle manufacturers Specialized Bicycle Components and Fizik, Carbon has partnerships with companies that include Johnson & Johnson and Vitamix to move beyond prototyping to full-scale additive manufacturing.
Bruce Geiselman, senior reporter
Contact: Carbon, Redwood City, Calif., 650-285-6307
Bruce Geiselman
Senior Staff Reporter Bruce Geiselman covers extrusion, blow molding, additive manufacturing, automation and end markets including automotive and packaging. He also writes features, including In Other Words and Problem Solved, for Plastics Machinery & Manufacturing, Plastics Recycling and The Journal of Blow Molding. He has extensive experience in daily and magazine journalism.
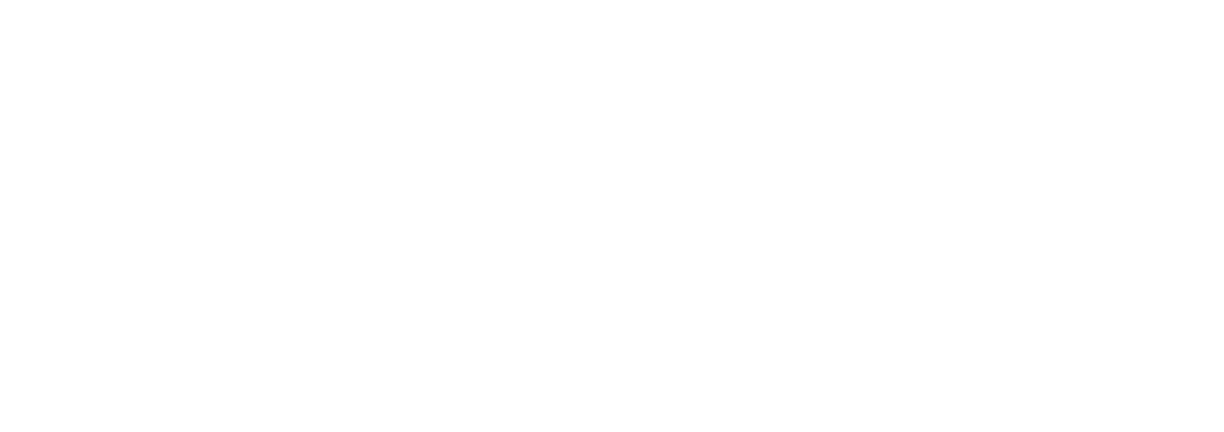