Lights-out manufacturing is not a new idea for Robert Schad.
He started working on it in the 1980s at Husky Injection Molding Systems Ltd., the first injection molding machine manufacturer he founded, and today he is running an aggressive R&D project at Niigon Machines Ltd., his second company.
The project at Husky more than 30 years ago was aimed at improving the reliability of making preforms, Schad said.
He has long espoused the idea that lights-out molding is necessary for North American processors to compete in the worldwide market and that everything in the molding plant — not just the molding machines — has to be capable of unattended operation.
“We only build injection molding machines and not molds, hot runners or other equipment,” Schad said. “We will, however, pass on all of our knowledge to support our customers.”
Phase I of the Niigon project has met its goal of running unattended for up to 10 hours at a time. The cell has a molding machine with 165 tons of clamping force and a 24-cavity mold that has been operating for more than two years at an otherwise-unused end of Niigon’s sprawling plant in Vaughan, Ontario.
The molding machine features automatic startup and shutdown and emergency shutdown when needed. Mold changeovers can be done in one hour.
The cell has molded more than 30 million PET preforms with no parts rejected by Niigon’s Canadian customer.
Orders for the four different food-industry preforms change from day to day, ranging from 500,000 to 1.5 million preforms per run. The four different preforms range from 21 grams to 38 grams with a 38mm neck thread. Frequent mold changes are required.
The cell includes liquid and masterbatch color dispensing with a pre-mixer, molding area dehumidification, a closed-loop water-processing system and direct communications between the machine control and the resin dryer and water temperature-control unit.
Phase II of the lights-out project, which was on schedule to start April 15, is considerably bigger. It features a molding machine with 330 tons of clamping force running a 72-cavity mold. The goal is 140 million preforms a year.
The Phase II preforms will weigh 16 grams and have a 33mm neck thread.
A key to making the lights-out system work is developing a reliable cycle-complete function to safely shut down the cell in the event of a power outage. The Niigon solution will use a power buffer to complete a full cycle. The power buffer includes super capacitors to maintain 750 volts on the bus bar that drives the servomotors. The power buffer also can be used to provide peak power shaving.
Schad has again targeted 1 hour for mold changes. The system includes a dedicated robot crane, a split gate and improved accessibility to the mold and robotics.
What is Schad’s secret for building molding machines suited for lights-out operation? “To focus on every service issue, no matter how small,” he said.
Most of the auxiliary equipment in Phase II is the same as in Phase I but in larger capacities. This includes dryers from Conair Group, chillers from Berg Chilling Systems and robots for post-mold cooling developed by Niigon.
The Phase II system will use automated guided vehicles (AGVs) to move empty containers to the molding cell and full containers from the molding cell to the weighing and labeling stations. Until the AGVs are phased in, a pallet conveyor system from Alfacon Solutions, which recently was acquired by JMP Solutions, is being used for unattended production.
On the opposite side of the plant, Schad has installed a fully automated, high-density storage system complete with a stacker crane and radio-controlled shuttles for storage and retrieval from 576 pallet locations. The AGVs will move containers from the labeling and weighing stations to the storage system, then eventually to the staging area for loading onto trucks.
The Phase I molding cell and the Phase II cell are located side-by-side, and the Phase I cell also will be serviced by the AGVs.
Schad said goals of the Phase II project include unattended production for 24 hours, 100 percent in-line quality inspection for parts, automatic vent cleaning, faster color changes and cycle-time reduction. Initially, an Intravis Sample- PreWatcher will inspect parts.
Schad estimated he has invested about $2.3 million in the Niigon lights-out projects. Two different Canadian customers each own one of the Niigon molding machines and molds.
Ron Shinn, editor
Contact:
Niigon Machines Ltd. Vaughan, Ontario, 905-265-0277,
Ron Shinn | Editor
Editor Ron Shinn is a co-founder of Plastics Machinery & Manufacturing and has been covering the plastics industry for more than 35 years. He leads the editorial team, directs coverage and sets the editorial calendar. He also writes features, including the Talking Points column and On the Factory Floor, and covers recycling and sustainability for PMM and Plastics Recycling.
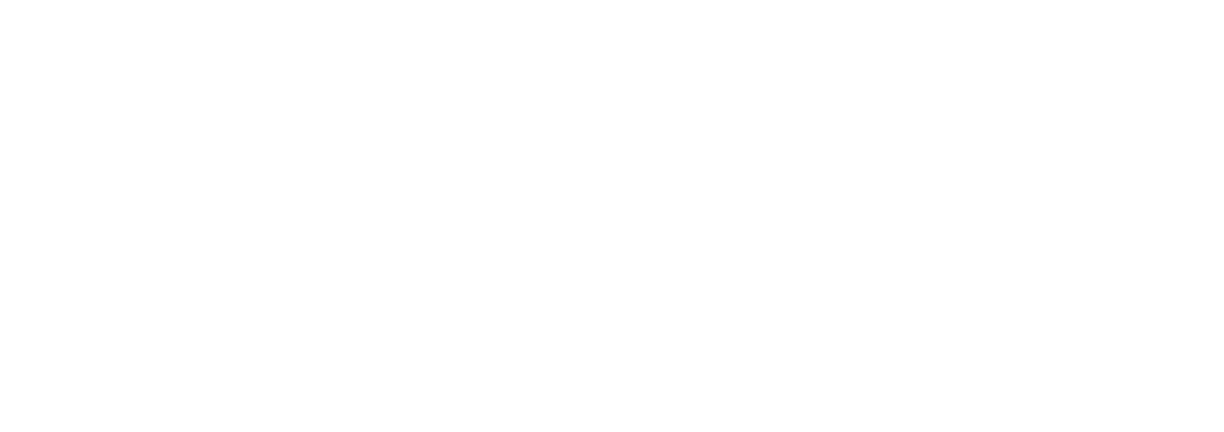