By Ghislaine Bailey, Nova Chemicals
With the rise of recycled content mandates and extended producer responsibility (EPR) programs, the market for recycled plastics is growing rapidly. Research from Fortune Business Insights projects the global recycled plastics market to nearly double from $55 billion in 2024 to $107 billion by 2032. Although more companies are exploring the use of recycled materials in their products, postconsumer recycled (PCR) plastic for food packaging requires the passing of several necessary milestones.
Polyethylene (PE) is commonly used in many types of food packaging because of its versatility and barrier properties, and the U.S. Food and Drug Administration has strict regulations for food-contact PE. To produce food-contact mechanically recycled PE (rPE), all materials entering the recycling stream must meet the same standards as virgin food-contact PE.
Collecting film scrap intended for food-contact purposes requires recyclers to track the chain of custody for all incoming bales so the composition, manufacturer and use of the plastic can be validated.
This is a big ask for generators and recyclers; it requires coordination, diligence and innovative thinking to simplify plastic film collection for companies and retailers while asking them to pay close attention to PE packaging they view as waste.
Designing the necessary networks and protocols to produce food-contact rPE through mechanical recycling is a lot of work, but the lasting effects are worth the effort. Expanding the production of food-contact rPE will help bring about meaningful progress toward a circular economy for plastics and support a stronger supply chain for recycled plastic, leading to more use over time.
Chain of custody
Maintaining a chain of custody for rPE is important because of the FDA’s regulations for food-contact.
Virgin PE for food packaging must meet the standards defined in the Federal Food, Drug, and Cosmetic Act, which addresses material purity, manufacturing practices, comonomer percentages and properties such as density and melt index.
Although postconsumer PE does not have to come from food packaging to be reprocessed into food-contact rPE, it has to adhere to the same standards. This is because the mechanical recycling process only removes surface contaminants, not additives, from plastics. Every food-contact substance (FCS), which includes additives like antioxidants and colorants, must be compliant with applicable FDA regulations before being used as a component in food packaging materials. Plastics containing additives that are not approved as an FCS cannot be allowed into the recycling stream for recycled food-contact materials.
Letter of nonobjection
To manage these requirements, the FDA examines each proposal for food-contact recycled plastic on a case-by-case basis. Although it is technically voluntary and not legally binding, it is a best practice for recyclers to obtain a letter of nonobjection (LNO) from the FDA, which is an opinion that the proposed recycling process and the approach to chain of custody is expected to produce materials that can be used in food-contact applications.
There are three parts to the LNO submission process: a description of the recycling process, test results to show the removal of contaminants and the proposed conditions of use for the recycled plastic.
The description of the recycling process must include details about the source of the recyclable materials, meaning recyclers should be able to audit the plastic’s journey from its production to how it was used and the types of products it packaged. The FDA also requires information about source controls and the precautions in place to ensure the appropriate plastics are collected and remain uncontaminated.
Collection protocols
For most PE film suppliers, including retailers, grocery stores, manufacturers and distribution centers, the task of tracking and verifying the uses and suppliers of stretch film used during shipping is a new process.
Recyclers and procurement partners need to nurture these relationships and develop clear and simple protocols to support the chain of custody validation process outlined in the LNO. Collaboration throughout the value chain can help streamline collection methods for rPE products that meet customer needs, such as NOVA Chemicals’ mechanical recycling facility in Connersville, Indiana, where it is collaborating with Novolex, which will operate the facility on Nova’s behalf
It is important for recyclers to communicate the value of these materials and the positive impacts of repurposing used plastics into high-performance applications.
Mechanical recycling processes
At a recycling facility, good manufacturing practices (GMP) and quality management systems are crucial. Current GMP are defined by the FDA and cover personnel, maintenance, pest control, process water management and other aspects of plant operations.
Cross contamination between different types of plastics must be prevented. One way to do this is to design separate wash lines and silo systems. Any process additives, such as a stabilizer added during pelletization, must also be accounted for as the FDA considers the total amount present when evaluating food-contact materials.
After the PE film has been collected and validated as usable in food packaging through its chain of custody, incoming bales must be sorted and cleaned. A series of optical sorters separate different materials, with plastics unsuitable for food-contact uses diverted to other applications, such as plastic lumber or advanced recycling. The materials are shredded and washed to remove surface contamination, glue and fiber that can cause problems in processing equipment and with the performance in the end product.
After drying, the rPE is extruded into pellets. The pellets then spend several hours circulating in hot air to remove any remaining tastes and odors, and the final product is blended in silos for a homogeneous mixture.
Recycled content targets
Major brands and retailers around the world are committing to significant recycled content targets for packaging over the next decade, and many of them are food companies.
To meet their objectives, manufacturers need access to high-quality rPE that can be used in food-contact applications. As recyclers, establishing a chain of custody and obtaining an LNO supports producer and consumer confidence in PCR materials.
Building the rPE supply chain cannot be done in isolation. Partnerships and collaborations will make it easier to develop methodologies that support supply chain transparency and verifiable chains of custody so that more plastics are able to be reprocessed into high-value materials.
With a commitment to product stewardship and an understanding of the regulatory landscape, recyclers can help bring more recycled-material options to the food industry and support the transition to a more sustainable model of production.
For more information
Nova Chemicals, Calgary, Alberta, 403-750-3600, www.novachem.com
The author is senior advisor, product regulations at Nova Chemicals.
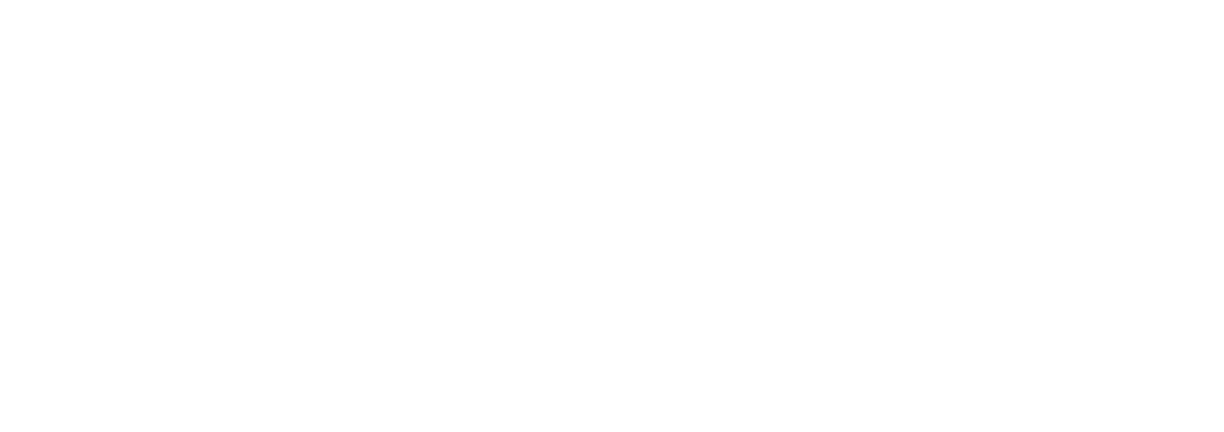