By Ron Shinn
WiPa Werkzeug und Maschinenbau GmbH is a new name in recycling equipment in North America. It manufactures wash lines, grinding equipment, agglomerators and controls at its headquarters in Stadtlohn, Germany.
WiPa is currently represented in the U.S. by Zerma America LLC, but a new company titled WiPa USA is being established to focus on WiPa products, according to Carlos E. Garcia, owner of Zerma America and WiPa USA.
Garcia talked about three WiPa products at the Plastics Recycling Conference in February: the Type MD dry cleaner, Silo Type S and the Plast Compactor Type PC.
The Type MD machine is multi-functional in that it can be used as a dry cleaner, as well as a conventional dryer, for cleaning plastic material with or without water. It comes in four sizes, with rotors ranging from 39 inches to 78 inches.
The plastic material is fed into the top of the housing and is conveyed to the discharge side by the internal rotor and the exchangeable throwing blades attached to the rotor. The material is accelerated when it enters the machine, which results in impurities, such as paper fibers, sand and organic matter, as well as the adhering water, being pushed through the holes in the screen basket.
The screen basket is continuously cleaned. Depending on the type and degree of contamination and the use of the machine, different screens can be used to remove the contamination.
A polygenic screen basket ensures continuous turning of the material, which significantly improves the separation of impurities. A square screen basket offers a higher degree of cleaning compared to a round screen basket, according to WiPa. More corners mean more friction and therefore a better cleaning effect.
The company said screen changes are easy, simply by loosening the screws that hold the screens onto a skeleton. The screen elements are inexpensive perforated plates. All plates have the same dimensions, which saves on storage and the cost of spare parts, since the elements can be interchanged.
Screen elements have a thicknesses of 3mm. The screen perforation can be individually adapted to the material. Round screen perforations between 2mm and 12mm are standard. However, other types of screens with conical or square perforations, as well as special screen elements for processing fibers or big bags, can be supplied.
Rotors are equipped with exchangeable Hardox throwing blades. This enables the use of a wide variety of materials and geometries, tailored to specific materials. In dry-cleaning applications, Hardox blades are also used to "armor" the inlet and outlets of the machine to prevent excess wear.
The Type MD machine can eliminate up to 95 percent of moisture, according to Garcia.
The WiPa Plast Compactor Type PC series is used to gently compact plastics with a low bulk density such as fibers, film, foils, stretch foil, foams, powder and dust. The compactor increases the bulk density of the material with little thermal damage.
The material stays in the Plast Compactor Type PC for only a few seconds. It is brought to a doughy state and is not melted at this stage.
During the next stage, finger-sized agglomerates are formed, which are cut to the desired particle size in a downstream cutting mill. The size of the agglomerate is defined by a screen installed in the granulator. To cool down the material and avoid the formation of dust and fines in the end product, the agglomerate is sent through a separation and recirculation unit before being sent to a silo or bag.
The Plast Compactor Type PC is available in seven sizes. The smallest, the PC 500, can be equipped with a main drive motor ranging from 15 kilowatts (kW) to 45kW, depending on the material being processed. The largest, the PC 850, can be equipped with a motor from 400kW to 1,000kW.
The WiPa Silo Type S modular silo can be expanded as needed. It can be used as a blending silo, round silo, film silo, buffer silo and dosing container for substrates.
The silo uses a push-bar system that WiPa said moves material efficiently and uses less energy than other systems. Push bars move back and forth. During the forward stroke, hinged paddles fold outward, conveying the material toward the discharge direction.
During the rearward stroke, the paddles fold inward and slide through the material with less resistance. This causes less material to be moved rearward on the back stroke.
WiPa said there is a 78 percent energy savings with this design compared with existing conventional designs.
Type S silos come in 11 sizes, ranging from 245 cubic feet capacity to 35,000 cubic feet.
WiPa in Germany is owned by the Wissing family. WiPa USA follows the same family-owned philosophy in that it is owned and operated by Carlos E. Garcia and his father, also named Carlos, along with other members of the Garcia family.
Contact:
WiPa USA, Weston, Fla., 954-224-1539, www.wipa-germany.de/en/home
Ron Shinn, editor
Ron Shinn | Editor
Editor Ron Shinn is a co-founder of Plastics Machinery & Manufacturing and has been covering the plastics industry for more than 35 years. He leads the editorial team, directs coverage and sets the editorial calendar. He also writes features, including the Talking Points column and On the Factory Floor, and covers recycling and sustainability for PMM and Plastics Recycling.
MAS 110 increases throughput
ACS Group names area sales manager
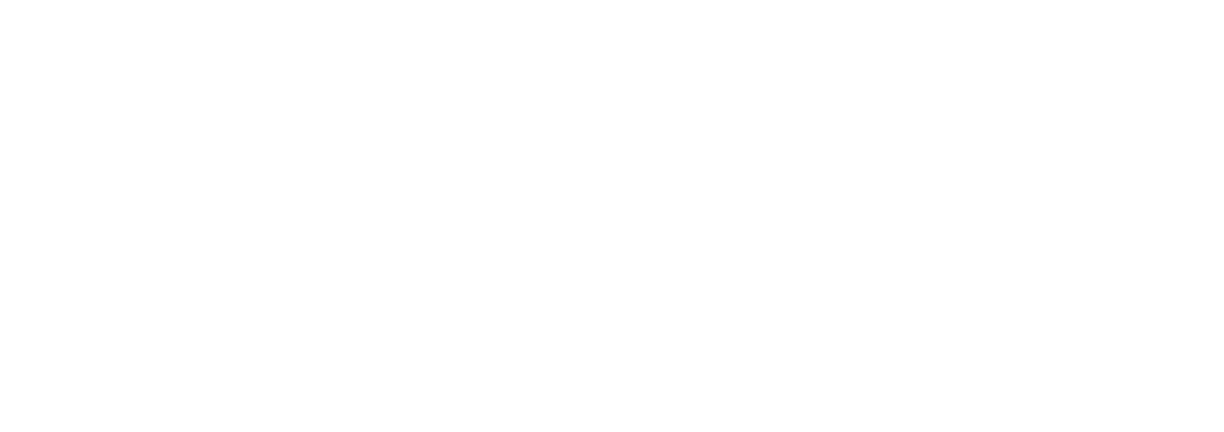