From the spring 2022 issue of Plastics Recycling.
By Ron Shinn
The clamor from consumers, brand owners and government mandates for more recycled content in bottles and food packaging sounds like a significant business opportunity for Alpek Polyester and its DAK Americas LLC business unit.
Alpek Polyester, the largest PET producer and recycler in the Western Hemisphere, has invested $32 million to expand a PET recycling plant in Richmond, Ind., to supply the growing demand for recycled PET (rPET).
What will be the future demand for rPET?
“Growing and growing and growing as brand companies request recycled content, coupled with more and more states and regions passing legislation on requirements for recycled content,” says Ricky Lane, public affairs and trade relations director for Alpek Polyester. “We see initial market targets for 25 percent required recycled content by 2025 and 30 percent or higher by 2030. We are committed to meeting our customers’ goals to achieve these targets.”
Lane says the ability to produce and supply rPET is a key strategy for Alpek Polyester and has helped establish it as a leader in recycling. The company has been involved in recycling for more than 10 years and the Richmond facility is its third PET recycling facility.
The Alpek Polyester strategy is to be able to sell virgin PET; recycled PET that a processor can use as-is or mix with virgin resin; and a virgin-resin-based product that contains a specified percentage of rPET that is ready for customers to process. The company refers to the recycled-content product as its Single Pellet Technology, Lane says.
DAK Americas, based in Charlotte, N.C., acquired the 10-year-old Perpetual Recycling Solutions plant in Richmond in early 2019. It is being rebranded as the Alpek Polyester Richmond Site under the legal entity of DAK Americas.
The facility already had the capacity to produce about 100 million pounds of clear, green or mixed-color rPET flake per year when DAK Americas acquired it. It was equipped with Sorema processing equipment and Titech automated near-infrared optical flake sorters. Recycled material collected mostly at curbsides comes into the plant, metal is removed, bottles are sorted, then the material is ground, washed and the flake is separated and sorted.
DAK Americas’ investment is designed to turn that PET flake into pellets and increase the material’s intrinsic viscosity (IV) to accommodate direct bottle-to-bottle recycling. A higher IV improves the material’s melting point, crystallinity and tensile strength and allows it to be reprocessed into bottles.
DAK Americas added a second building next door along with six silos and installed two complete pelletizing lines from Starlinger & Co. GmbH. The silos, with a capacity of 500,000 pounds each, included both flake silos and ones for pellets or finished product, and bulk loading equipment that give the plant the ability to ship material in bulk rather than just bags.
The three flake silos can hold enough flake to run the pellet plant for about one week.
There is space in the new building for a third pelletizing line, according to Jeremy Troutwine, operations leader at the Richmond facility, who has supervised the expansion. The site sits on 25 acres.
The old and new plants are connected by a pneumatic conveying system that moves the finished flakes to silos at the new plant.
The two Starlinger recoSTAR lines together can produce a total of about 66 million pounds of pellets a year.
The flake is stored in a silo until it is ready to be processed, Troutwine says. Once it is conveyed from the silo, the line has an option to send the material through a blender. Next, it is dried, extruded, filtered and water cooled to complete the pelletizing process.
Then the pellets are fed into a solid-state polycondensation (SSP) reactor to increase the IV. The SSP uses heat and pressure to lengthen the polymer chains. The final step is to convey the material back to a storage silo to await shipment.
“Everything runs off an HMI that is very user-friendly,” Troutwine says.
The expanded operation employs 95 people. About 30 new jobs were added for the pelletizing project. It currently runs 24 hours a day, seven days per week. Troutwine estimated there will be slightly more than 100 employees when the plant reaches full capacity.
There are five full-time quality assurance personnel in the plant. The expansion project included expanding the lab that was already in operation and purchasing new equipment to test pellets.
Feedstock comes mostly from the Midwest. The finished rPET goes to customers throughout North America. It is expected the material will go mostly back into new bottles.
The expanded facility was running at 90 percent capacity in January. Lane says that when the pelletizing lines are fully commissioned, DAK Americas plans to upgrade the rPET flake process to debottleneck clear flake production and improve efficiency.
“These new project goals and improvements will focus heavily on increasing and optimizing sortation with the addition of optical sortation technology,” he says.
The project is on track even though there were delays in receiving equipment caused by supply chain issues due to COVID, Troutwine says.
The Richmond site was Alpek Polyester’s second food-grade PET recycling facility. The first is Ecopek S.A. in General Pacheco, Argentina, which it acquired in 2014. Ecopek has the capacity to produce about 35 million pounds a year of 100 percent rPET food-grade flake and pellets.
In mid-2021, DAK Americas acquired the former CarbonLite bottle-to-bottle PET recycling facility in Reading, Pa., for a reported $96 million. The plant, still under construction at acquisition, is expected to process up to 140 million pounds of postconsumer PET a year. It is now operated as the Alpek Polyester Reading Site.
DAK Americas also has a fiber-grade recycling joint venture in Fayetteville, N.C., with Shaw Industries, launched in 2010. It is called Clear Path Recycling and has capacity to produce about 40,000 tons of rPET flake a year.
Ron Shinn, editor
Ron Shinn | Editor
Editor Ron Shinn is a co-founder of Plastics Machinery & Manufacturing and has been covering the plastics industry for more than 35 years. He leads the editorial team, directs coverage and sets the editorial calendar. He also writes features, including the Talking Points column and On the Factory Floor, and covers recycling and sustainability for PMM and Plastics Recycling.
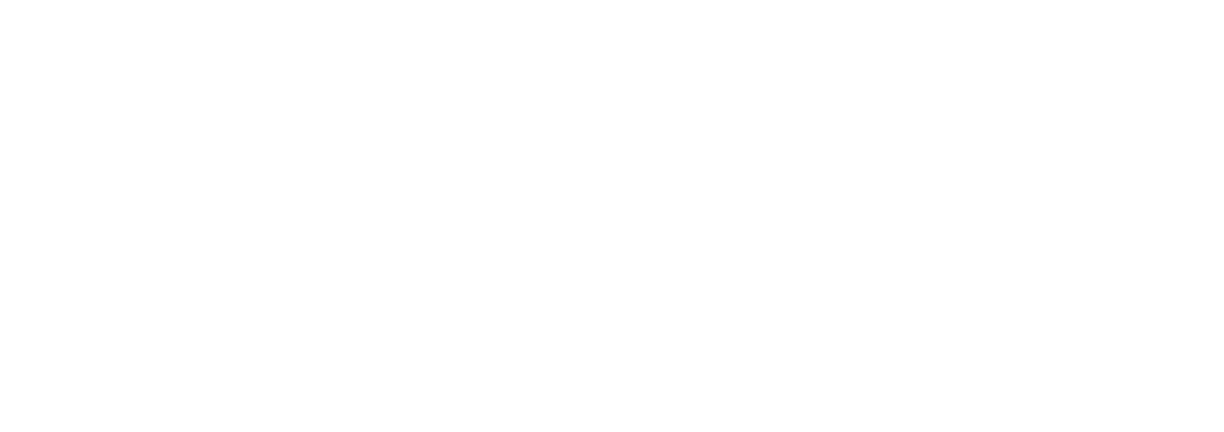