This story appeared in the Summer 2020 edition of Plastics Recycling magazine.
Heat-bonded porous structures. A patent awarded to Ten Cate Thiolon B.V., Nijverdal, the Netherlands, describes a method for making heat-bonded porous structures from recycled plastics, such as those used in drainage devices.
The current invention shares a previous invention’s use of an agglomerator to turn chopped thermoplastics scrap into small “noodles.” But the previous method was limited in the size and shape of its output, requiring extra steps to either stack and secure the output or to cut it into the required size for the desired end product. The current invention provides multiple methods of forming end products.
In one embodiment, noodles leaving the agglomerator are carried by a conveyor belt, which may be sprayed with water or another liquid to cool the exterior of the molten noodles, preventing them from sticking to the belt on contact or coalescing together to form a solid mass. By controlling the time, speed and concentration of noodles, this method can produce end shapes with the desired connection between noodles, density and open spaces or voids.
The noodles are passed to a possible second conveyor belt, which can form the noodles into clusters in buckets on the conveyor belt. These clusters are then passed through a rotating cylinder, which forms the clusters into roughly spherical shapes. These shapes are then passed into a cooling tank. The patent says the clusters could be formed into roughly the size of a tennis ball and used as water-treatment media.
In another embodiment, the noodles can be dropped from a conveyor belt into a chute that feeds the noodles down to form an extrusion profile. In one form, a conveyor belt would create a flat side to the profile, while an opposing second conveyor “… is formed from segmented sections that make the shape of the intended end form.”
In this example, the shape of the second conveyor is semicircular so that the noodles are formed into a profile that is flat on one side and semicircular on the other. As the resulting profile exits downward from between the conveyors, cooling jets reduce the profile’s temperature and help it solidify into its final form. Additional conveyor belts continue to propel the profile, which can then be cut to the desired length.
Patent 10,639,817; issued May 5
MAS 110 increases throughput
ACS Group names area sales manager
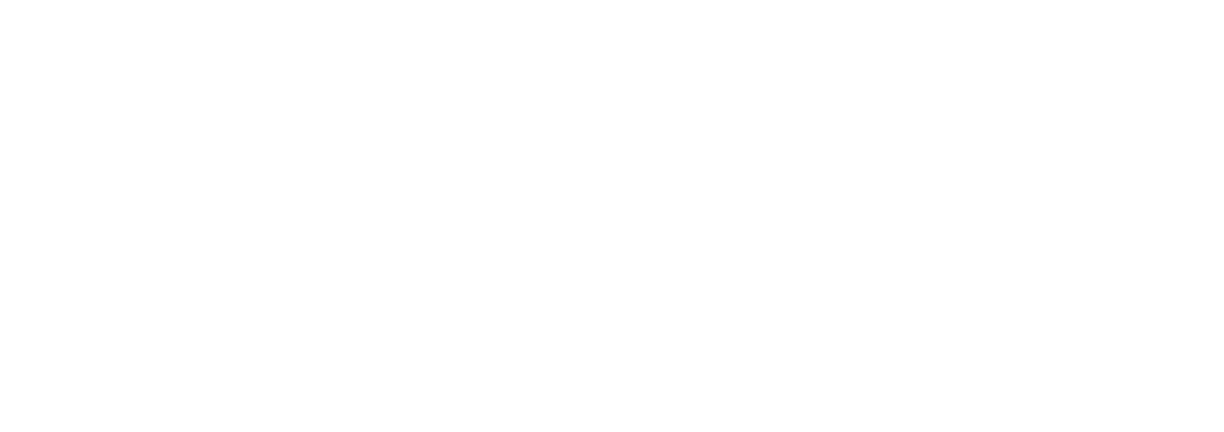