When it comes to scrap, plastics processors have high expectations for the equipment used to process material that others might characterize as garbage.
“The expectation of injection molders is to eliminate waste beside the machine, replace virgin resin, increase competitiveness, reduce material consumption and the carbon footprint of the company,” said Denis Metral, international granulator sales manager for Wittmann Battenfeld, which makes press-side granulators. The company aims for its equipment to operate in a closed-loop system that keeps contaminants out of the regrind.
The expectations Wittmann Battenfeld faces aren’t unique. Equipment suppliers cited regrind quality, equipment longevity, rotor speeds and price as some top considerations for customers. In-house recycling — long a strategy for reducing costs — is an imperative, as the recycling market evolves and governments and consumers increasingly demand more sustainable production practices.
Two years after China implemented its National Sword policy barring imports of recyclable waste, U.S. producers and recyclers of plastic scrap are still adjusting.
Dana Darley, senior sales director of Vecoplan’s plastics division, has seen it firsthand. He cited a pipe maker he knows that had been sending scrap to a recycler that shredded the material. But the recycler went out of business, forcing the company to recycle in-house.
Serving that need are companies like Vecoplan, which makes a wide range of size-reduction systems, from those that can be used in-house to large models appropriate for recyclers. Darley said that processors increasingly are able to justify processing scrap in-house. Material, such as barrier film, that once went straight to a landfill now can be economically processed.
Jim Hoffman, president of Rapid Granulator, said his company seeks to help customers return their scrap to productive use. “They want to find a way to use their material efficiently. And that granulator is the tool to give them the highest quality regrind. If they can get it into a granulated form as soon as possible, then it reduces the risk of contamination, being cross-mixed with other unusable materials.
“We’re trying to give people the best quality regrind by optimizing rotor speeds, by optimizing screen hole sizes and things like that, so that the right-sized granulator doesn’t cost them money to have in place.”
Hoffman sees ease of access and ease of cleaning as key concerns. Rotor speed is another big focus, which prompted Rapid to introduce a variable-speed machine. With the ability to fine-tune rotor speeds, machines can cut both rigid and soft materials.
Durability is a watchword for scrap-processing equipment.
“For machinery makers, it’s basically making it bulletproof. With most any company, the reclaim department is the redheaded stepchild. Nobody likes it. It’s there to fix mistakes,” Vecoplan’s Darley said.
“So, it’s a matter of, that equipment is not their production equipment, they don’t think of it like production equipment, it just needs to work. It needs to be simple to run. Very robust.”
As government regulations and the recycling market continue to evolve, the machinery maker representatives said there’s always room to grow.
Laws mandating even more closed-loop processes could be on the way. “We anticipate it, but it just hasn’t happened yet,” Darley said.
Sustainability just makes sense — economically and environmentally.
“Plastics recycling is an urgent topic to keep the planet clean,” Metral said. “The plastics industry is under growing pressure due to pollution concerns, especially ocean plastics, and must develop more and more sustainability opportunities.”
Allan Gerlat, correspondent
For more information
Vecoplan LLC, Archdale, N.C., 336-861-6070, www.vecoplanllc.com
Rapid Granulator Inc., Leetsdale, Pa., 724-584-5220, www.rapidgranulator.com
Wittmann Battenfeld Inc., Torrington, Conn., 860-496-9603, www.wittmann-group.com
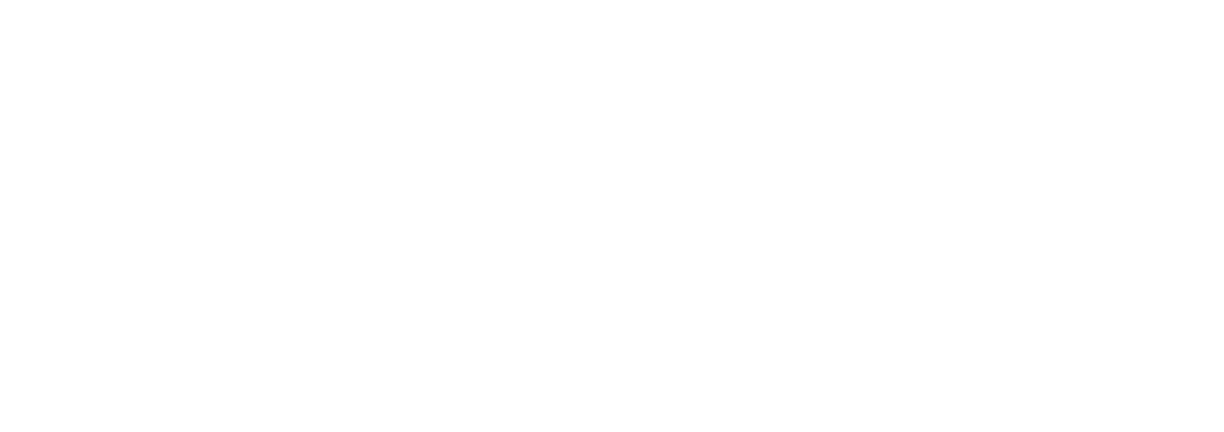