By Lynne Sherwin
Just as so many other industries experienced, the plastics industry saw in the pandemic and its aftermath how easily a supply chain can break when it’s stretched across the ocean. The industry has seen some moves toward reshoring, although it’s not a tidal wave yet.
I recently participated in a roundtable discussion with fellow Endeavor Business Media editors Robert Schoenberger (IndustryWeek), Karen Langhauser (Pharma Manufacturing) and Kevin Jones (FleetOwner). Watch it here; below are some additional thoughts about reshoring and plastics.
In a Reshoring Initiative report released July 8, plastics and rubber products ranked sixth among industries contributing to reshoring and foreign direct investment (FDI) job growth, with almost 6,000 jobs added in 2023.
In addition to the usual suspects like shipping costs, logistics and tariffs, one factor the report noted as making reshoring more affordable is that the U.S. is now producing more petroleum feedstock and resin. As the U.S. has added plants to turn feedstock into resin, Europe and other regions have experienced natural gas shortages.
There are a lot of tentacles to the reshoring story in the plastics industry. A more comprehensive look at reshoring in plastics can be found here.
Mold making is one area that is making a slow comeback in the U.S. after years of being outsourced, mostly to China. With molds made in China, quality is often an issue. Other negatives involve shipping challenges, long lead times and even intellectual property theft.
But as in most manufacturing areas, a lack of skilled workers is throwing up roadblocks in bringing plastics business home. Mold making, which requires a high degree of skill, is one of those areas of need. When mold making jobs went overseas, a lot of big mold shops closed and older workers retired; meanwhile, fewer replacements are coming up through the ranks and learning the trade. More attention and resources for apprenticeships, trade schools and other paths into the industry are needed.
Nearshoring is another option. In 2022, we wrote that Portugal, which has a long mold-making tradition, is now rebuilding some ties to U.S. processors. The country’s mold shops once sold almost two-thirds of their total mold output to the U.S. until Asia took over a lot of that business.
We’ve seen some nearshoring and FDI with the equipment companies we cover. Building primary processing machines in the US is still fairly rare, especially in injection molding, but some companies are exploring it. Some are setting up in Mexico for easier delivery to the U.S. and avoiding tariffs. Engel is putting $32 million into its facility in Queretaro, Mexico, and Arburg said recently it is considering a North American assembly facility.
LS Mtron, a South Korean injection molding machine maker from the LG family that’s making an aggressive move in the US market, invested more than $20 million in a new facility in Texas, currently to demonstrate and stock its injection molding machines, build LS tractors and improve logistics. But the site has room for expansion, and by 2027 the company hopes to announce plans for a new factory in the U.S.
In terms of reshoring of manufacturing plastic products, the U.S. imports somewhere between $50 and $70 billion worth of plastic-based products a year, according to various sources including Shale Crescent USA, an advocacy group for U.S. shale gas, and the United Nations’ Comtrade database.
But one executive told us flat out last year, “China is no longer the more economical choice.” Those looking to have a plastic part made need to consider the same issues as with mold making: shipping costs and logistics delays, quality and rising labor costs in Asia. Also, some companies are trying to reduce the environmental impact of long-distance shipping.
Electric vehicle (EV) batteries were an area of strong growth mentioned in the Reshoring Institute’s new report, and plastics play a role here. Entek, which makes extrusion equipment and also has a division that produces battery-separator film, announced that it had gotten a $1.2 billion loan from the U.S. Department of Energy to finance its facility now under construction in Terre Haute, Ind., to make parts for the growing U.S.-based EV battery supply chain.
But sometimes we just don’t learn. Everyone remembers the dire shortages of personal protective equipment (PPE) during the early months of the pandemic. Masks and gowns are made from plastic meltblown fiber, and almost all of it came from China. When COVID hit, U.S. companies sprang up and invested a lot of money to reshore production of PPE. But now that the pandemic has eased, cheap Chinese products are again flooding the market, American companies are struggling and many have closed.
The American Medical Manufacturers Association, formerly the American Mask Manufacturers Association formed during the pandemic, is keeping up lobbying efforts to support domestic production of PPE and create a stockpile, but memories are short and the lure of lower costs is winning out again.
We’ll see whether the lessons of the pandemic stick.
Lynne Sherwin | Managing Editor
Managing editor Lynne Sherwin handles day-to-day operations and coordinates production of Plastics Machinery & Manufacturing’s print magazine, website and social media presence, as well as Plastics Recycling and The Journal of Blow Molding. She also writes features, including the annual machinery buying survey. She has more than 30 years of experience in daily and magazine journalism.
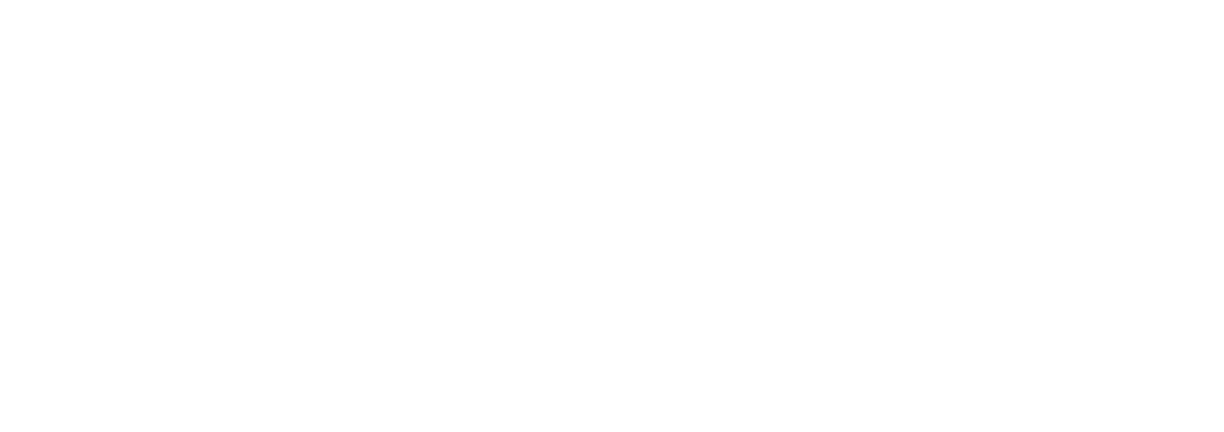