By Karen Hanna
Caps strong enough to withstand the risk of bursting and releasing a volcano of sticky syrup are a must for every soda bottle maker.
Mold-Masters aims to put a lid on the problem, with a new premium version of gate seals for its Sprint product line of hot-runner systems. The new gate seals — branded as Sprint Apex — could make lightweighting easier and allow caps to hold up under pressure, even on bottles in sealed cars in August. As an additional benefit, they are cheaper to maintain than traditional gate seals, and color changes are faster, said Thomas Bechtel, Mold-Masters' global sales director for the packaging and medical sectors.
“What this product does, it increases the safety factor,” he said. “Let’s say a molder today produces a truckload full of closures and sends them to Coke [and] two of those closures are cracking; they will very likely return a full truckload of closures back to that converter. By applying this extra safety on ESCR, or [environmental] stress crack resistance, the risk of getting all of this truckload returned to your factory is significantly reduced.”
According to Bechtel, Sprint Apex gate seals represent an upgrade over conventional gate seals that produce spokes radiating in a star-shaped pattern from the center of a cap. The flow lines that produce those spokes — normally invisible to the naked eye — are vulnerable to cracking under pressure and are more likely than other areas of the cap to display vestigial colors from one color change to the next.
Conventional gate seals separate the melt flow through holes in the gate seal tip just before it enters the mold, while the Sprint Apex gate seal initiates this separation much further back, where the melt is hotter. This gives the melt fronts a better opportunity to merge and blend together again before they hit the cold cavity.
“The plastic melt merges a lot easier when the melt is hotter than when the melt is colder. That’s the whole trick,” Bechtel said.
That minimizes flow lines.
Testing performed by Dow Pack Studios showed that caps produced by systems with the gate seals can handle 40 percent more stress than caps produced by systems with conventional gate seals.
By minimizing flow lines in the cap where color can become trapped, the Sprint Apex system reduces the number of cycles needed to perform some color changes by up to 65 percent.
Cutting down on the color-change process not only ensures machine uptime, it limits the amount of material molders end up spoiling.
“First of all, you are keeping your machines busy producing things that you cannot sell. And secondly, you are wasting a lot of material because you cannot use that material, you cannot use those scraps. So, you have to dump that resin. So, you’re generating a lot of cost, and you basically screw all your sustainability goals,” Bechtel said.
While makers of caps for fizzy beverage bottles — which are most susceptible to ESCR — stand to benefit the most from using Sprint Apex gate seals, makers of caps for noncarbonated drinks also can use the new components. Because caps produced by the gate seals are stronger, they can mirror the performance characteristics of conventionally made caps — with less material.
“A typical Coca-Cola cap is 2.15 grams. And Coke is using billions of those closures,” Bechtel said. “If by using that technology, you can take off 0.05 gram, so it’s maybe 2.1 instead of 2.15, they will love this because it will reduce the costs significantly on that part, and it will make it more environmentally friendly.”
Existing Sprint hot runner systems can be retrofitted with the Sprint Apex gate seals as they share the same cut-out as the standard Sprint gate seal. These cut-outs use an industry-standard geometry that is common for cap and closure applications.
Because it is an industry standard cut-out, molds incorporating other hot-runner brands also can be retrofitted to a Sprint hot-runner system with the gate seals.
“If your existing closure mold has these industry standard cut-outs already, that saves up to $70,000 of rework or new inserts and you’ll get all the benefits of a new Sprint hot runner system, which can make such a retrofit very attractive,” Bechtel said.
Sprint Apex gate seals are designed to make swapping between different cap geometries easy and cost-effective, he said.
“Usually when you exchange from one hot runner to the next, you have to exchange that geometry, as well, just to make sure that the geometry fits and it’s sealing and all that; well, those products are designed to fit exactly the same contour,” he said.
Reshaping contours, as other systems require, can cost $70,000, he said.
Bechtel said another advantage of the new system is that it doesn’t use Vespel insulators — wear parts used by hot runners with conventional gate seals. The components cost about $50 each.
“It doesn’t sound much, but if you add it all up. … It’s a wear item on a higher-cavitation closure tool, that is easily $10,000 a year. So, $50 times 48, which is the cavitation, exchanging it four times a year, you’re at $10,000,” he said, providing a ballpark figure.
For molders of caps for bottles for carbonated beverages, the numerous advantages of using the Sprint Apex all add up, he said.
“It’s basically a triple saving, or a double saving plus a performance improvement,” he said.
Karen Hanna, senior staff reporter
Contact:
Mold-Masters, Georgetown, Ontario, 905-877-0185, www.moldmasters.com
Karen Hanna | Senior Staff Reporter
Senior Staff Reporter Karen Hanna covers injection molding, molds and tooling, processors, workforce and other topics, and writes features including In Other Words and Problem Solved for Plastics Machinery & Manufacturing, Plastics Recycling and The Journal of Blow Molding. She has more than 15 years of experience in daily and magazine journalism.
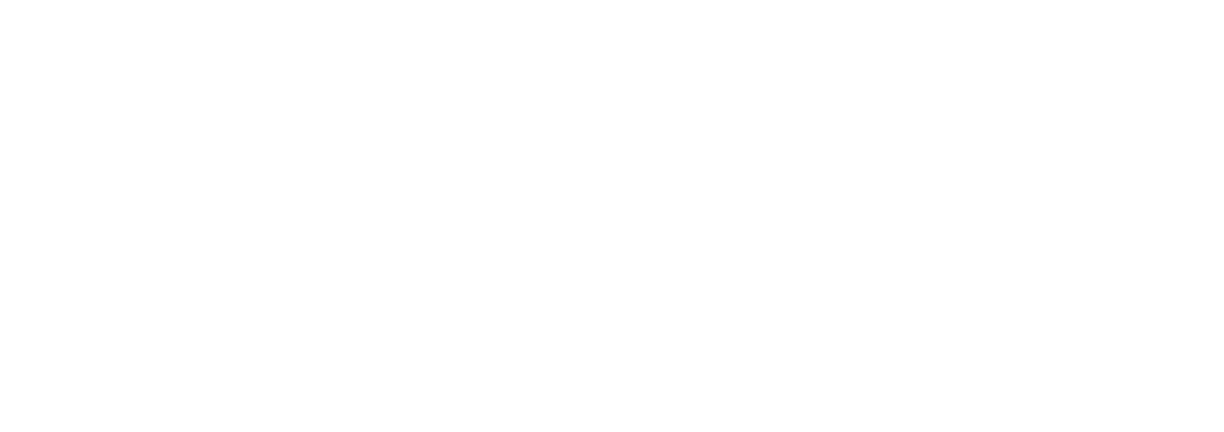