By Karen Hanna
As a large cohort of experienced workers in the manufacturing sector age, companies face a need to develop something much more important than parts: New workers to fill the void.
“You have demographic changes where older workers are retiring and younger workers are coming in, and those younger workers need to be trained up on the technical skills to do the job,” said Clare Epstein, GM for the commercial sector for Vector Solutions, which provides training for a variety of manufacturing industries, including plastics.
Instilling career-long lessons and company values into the next generation of workers has become critical for companies. For example, injection molding machine maker Arburg recently announced it’s taken on 104 trainees. Meanwhile, molding components manufacturer Hasco announced its German headquarters, located about 250 miles away, recently welcomed three clerk interns. Around the same time this summer, the Universal Robots Academy marked its own milestone — 200,000 participants.
However, overall, the influx of new workers continues to fall short of the outflow. According to preliminary, seasonally adjusted data released by the U.S. Bureau of Labor Statistics (BLS), 414,000 people left manufacturing jobs in July, while 402,000 took manufacturing jobs. More than 550,000 manufacturing jobs were unfilled.
Within the manufacturing industry, about 45 percent of tool and die makers were 55 or older last year; so were more than 38 percent of the workers the BLS defined as “other machine tool setters, operators, and tenders, metal and plastic.”
It’s a lot of experience and knowledge to replace.
“With the challenge of finding skilled workers these days, training is no longer optional. It is essential. And it can’t be a one-and-done, it must be re-occurring and consistent,” said Karen Paulson, president of Paulson Training. “A well-run training program with clear goals and expectations not only will save tens of thousands of dollars, it will reduce numerous issues within the plant. I’m not saying this is easy to do, but it is well worth the time and investment.”
Developing the workforce
One company that’s found a way to appeal to new workers is rapidly growing Pyramid Molding Group, which comprises molding shop Pyramid Plastics and tool builder Industrial Molds. More than 18 percent of the company's workforce started within the past six months.
“We have not found it too difficult to find great people,” said Becca Peterson, director of business and community development. “This is in part due to our willingness to train our own talent; hiring more for fit and spending the time to train the specific skills needed.”
Since May, Pyramid Plastics has added 18 new employees — eight assembly specialists, seven machine operators and three supervisors — while Industrial Molds has added three people to its staff.
In all, the plants employed 113 people as of early September, with seven more new hires expected to start soon.
To overcome skills gaps, the shops sponsor on-site job shadowing and provide cross training; Industrial Molds also offers a four-year apprenticeship. Training is an expectation across all levels — even to college-educated new engineers.
Every quarter, Pyramid Plastics tests operators to determine their skill level, from entry-level operator to master machine operator/part inspector, Peterson said. When operators’ rating increases, so does their pay.
Embedding continuous improvement
Companies are responding to the labor shortage with a flood of training options. For example, Christian Richard, corporate communications manager and sales administration manager for Bekum Maschinenfabriken GmbH, Berlin, said the OEM provides training services and consultation to help processors address specific knowledge gaps.
The emphasis on training has changed companies’ outlook.
“The deficit in worker knowledge has prompted industries to foster a culture of continuous learning,” he said.
Umberto Catignani, who provides training classes and seminars to injection molders, said that for employees and companies, training should provide insight into how processes work — not just which buttons to push. Too often, though, lacking deep knowledge of the process, workers turn on each other when things go wrong.
That can point to training deficiencies.
“I have worked with some process technicians with decades of experience, and they lack the basic processing methodology and understanding to properly troubleshoot,” said Catignani, president of Orbital Plastics Consulting. “This usually comes from employees that have been trained via ‘tribal knowledge,’ i.e., by others within their department that might also lack troubleshooting skills or simply did not take the time to explain why a particular change solved the problem. … If you do not understand why you are making a change, unfortunately you are merely guessing at a potential solution.”
For processors like Murphy Forsyth, GM of injection molding of Zero Tolerance, Clinton Township, Mich., training can provide the deep insights that create opportunities for improvement.
In comments provided by Milacron, Forsyth said a Roboshot class offered by Milacron paid for itself in just one day.
“I learned about mold cooling and the adjustments you can make to your process to help save on cycle time,” Forsyth said. “With the knowledge the instructor shared with the class, I was able to apply it to our production mold process when I returned from training. The adjustments I made helped our cycle time by over 8-10 seconds on average. With this adjustment, we were able to run one-quarter more parts per shift, finishing orders more quickly and efficiently.”
Filling the pipeline
At a time in which companies have struggled to hire workers, the benefits of training go beyond better parts, to include greater worker satisfaction and engagement. With the right opportunities, today’s new employee can one day take the roles vacated by an older, more-experienced worker, training providers and representatives of OEMs pointed out.
“Every molder we are talking to has skill development as a No. 1 priority,” said Martin Baumann, president and CEO of Arburg Inc. “And it isn’t just about training new employees. It is just as important to keep existing team members engaged. Continuous training of current employees can be a key element in retaining them over time.”
For Torsten Kruse, president of Kruse Training, it comes down to a philosophy of “Attract, Train, Retain.”
He said training gives workers a foundation and helps them avoid the frustration that comes with being new on the job.
When training workers, Catignani said he can identify talent based on the questions that come up in class. “When I was working on a problem, if the personnel present were inquisitive, curious and asked questions such as: ‘How did you fix that problem? Why did you make that change? How did you know to make that change? How long do you have to wait before you can walk away from the machine and know you have fixed the problem? Will that change work on similar parts?’ … These operators usually continued to ask questions, and I would target these individuals to become process technicians.”
Not all processors make that connection, though, he said.
For some, the cost of training seems too daunting.
“Usually, people look at it from a money side instead of, what are they really going to get, instead of investing in the people?” said David Routsis, president of Routsis Training, who lamented that training dollars are among the first cuts when business is tough. “ … What happens is you end up with happier people when you’re training them because they feel they’re getting something out of it, and the company is getting better product and a better employee out of it, as well.”
As Catignani said, “They might state: ‘If I train my personnel, they might take that knowledge and use it to get a better-paying job or leave my plant.’ I say, ‘What if you don’t train them and they stay?’ ”
For Pyramid Molding Group, that’s not an option
Human-resources manager Chris Paulson confirmed experience isn’t everything. Training can compensate for skills gaps for candidates who have the personal characteristics that align with the company’s values.
“When looking for new employees, I often seek a combination of skills, attributes and qualities that align with Pyramid Molding Groups requirements and organizational culture," he said. “Hiring a candidate that will fit well within our company culture is just as important as their skill set that they bring to the table. Pyramid Molding Group strives for a positive and productive work environment.”
Maintaining that culture requires a commitment to training.
“Really, it comes down to our company culture of sharing and being willing to invest the time in new talent," Peterson said. "Our team members are patient, and they are great teachers. They understand the importance of training up new talent to help keep up with the demands as we continue to grow.”
Karen Hanna, senior staff reporter
Contact:
Arburg Inc., Rocky Hill, Conn., 860-667-6500, www.arburg.com
Bekum America Corp., Williamston, Mich., 517-655-4331, www.bekumamerica.com
Kruse Training Inc., Naples, Fla., 239-351-7428, www.krusetraining.com
Milacron LLC, Batavia, Ohio, 513-536-2000, www.milacron.com
Orbital Plastics Consulting Inc., Atlanta, 404-849-6714, www.orbitalplastics.com
Paulson Training Programs Inc., Chester, Conn., 860-526-3099, www.paulsontraining.com
Routsis Training LLC, Nashua, N.H., 978-957-0700, www.traininteractive.com
Vector Solutions, Tampa, Fla., 813-207-0012, www.vectorsolutions.com
Karen Hanna | Senior Staff Reporter
Senior Staff Reporter Karen Hanna covers injection molding, molds and tooling, processors, workforce and other topics, and writes features including In Other Words and Problem Solved for Plastics Machinery & Manufacturing, Plastics Recycling and The Journal of Blow Molding. She has more than 15 years of experience in daily and magazine journalism.
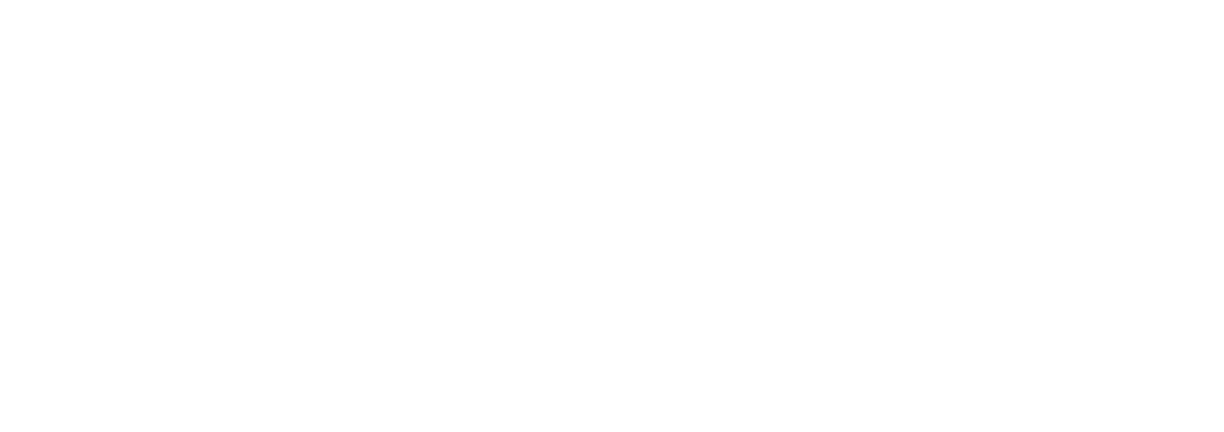