By Karen Hanna
Lean advocate David Rizzardo is a believer in a philosophy that fails. A lot.
“Most would agree that Lean has a failure rate of 70 percent or more,” he writes in his book, “Lean – Let’s Get It Right!”
Before you blame it on lean, he and fellow experts and practitioners would like you to consider some other possibilities: Half-hearted leadership, poor follow-through, a culture where continuous improvement never grabs top priority.
They say companies that look at lean as a one-and-done project won’t sustain success. Commitment and training are vital to the journey.
“We’ve got to get to the point where we’re not saying, ‘Well, yeah, we quit doing lean.’ It’s like saying, ‘I quit breathing,’ ” said Rizzardo, who, as associate director of the Maryland World Class Consortia Ltd., facilitates conversations among company leaders who want to get serious about going lean.
Making a commitment
When Michael French, the president of Comco Plastics Inc., Huntington Station, N.Y., began implementing time-consuming, companywide meetings to encourage employees to think lean, he realized he was making a sacrifice for the long term.
“Between a half an hour and 45 minutes, we’ve committed 45 minutes a day over an 8-hour day to lean,” he said. “When we first started, people thought I was crazy, like we’re going to lose 45 minutes of production. Like, yes, we are. But the things we’re going to gain are going to be immeasurable.”
His is the right attitude, say lean trainers like Rizzardo.
Too many company leaders, pressed by day-to-day demands, lose sight of long-term goals. As a recent client put it to Henry Foppoli, a managing partner at the AMSaxum consulting firm: “We will need your help for the implementation, but right now, we have other fires to put out.”
Foppoli compares it to a person in a hurry to cut a tree with a dull blade. Stepping away to sharpen the blade seems counterintuitive because it means devoting time to an activity that doesn’t directly bring down the tree; however, failing to sharpen the blade makes the entire activity a much harder slog.
“When you see the benefits — and that will depend on the maturity of the leadership ... you don’t wait until you have time; you make time for it,” Foppoli said.
Emphasis on training
Comco’s workforce of about 35 fabricates and assembles very small batches of bespoke parts for semiconductor, commercial and aerospace applications, as well as analytical equipment andmedical devices. But that’s not the focus of training at the company.
Lean is.
“Especially with our newer employees who are largely totally unfamiliar with lean or continuous improvement, they think it’s kind of hocus pocus, but we have to show them the benefits,” French said.
Training employees about lean is important to the success of the approach, proponents lsay.
Carl Livesay, who has leveraged lean principles in an effort to turn around the fortunes of Mercury Plastics MD, said training is particularly critical among the plant’s entry-level workers.
“You can’t talk about ‘work-in-process' for somebody who doesn’t have any idea of what it is,” he said. “So, we do a lot of classroom training of people explaining what ‘work-in-process' is and what overhead’s about and costing, and then they’re anxious to go back and deploy those things.”
At Comco, employees spend their first 30 days learning about lean from French. Discussions center around examples outside the shop, such as projects workers are taking on at home or the experience they might have had when they last stopped for fast food.
“Sometimes it’s hard to see it in the workplace; especially in the beginning, it’s easier to see in the outside world,” French said.
Six months later, employees participate in more formal training.
The company’s morning meetings also center on lean. They typically start with a 3- to 5-minute video, then employees have time to discuss changes they might recommend or have already started.
“We have these meetings every day, people share their improvements every day, and it’s, on some degree, contagious,” French said.
To ensure the company can weather employee absences, it also requires employees to cross-train for a variety of positions.
Take it from the top
French’s hands-on approach to lean might set him apart from some company leaders Foppoli sees. A lukewarm attitude on their end will doom lean.
“You can train all the employees, the frontline employees, they will learn the lean tools, they will identify lots of opportunities. But if top executives of the company don’t support their efforts to implement the projects, it won’t go anywhere,” he said.
It isn’t enough to read a book, learn the lean terminology, build some charts and expect improvement, Rizzardo said, though he said believes “spotty lean” — poor implementation to the approach — “is still better than no lean.”
For best results, the whole workplace culture has to change, he said.
As much of a commitment as that requires, not doing anything could be worse.
“The longer-term part of the job is [that] we need to improve; otherwise in the future, we may not have those short-term needs,” Rizzardo said.
Having onboarded employees in recent years, French said he’s reminded of the importance of continuously improving how Comco goes about its business.
“Because a lot of shops, a lot of the mom-and-pop shops ... I think they closed up,” he said, “And I know this because I got a bunch of employees from people who left companies that closed.”
Karen Hanna, senior staff reporter
Contact:
AMSaxum Inc., Burlington, Ontario, 888-772-2809, www.amsaxum.com
The Maryland World Class Consortia Ltd., Joppa, Md., www.leanmaryland.com
More on lean manufacturing
Comco and Mercury Plastics show how they've improved through cutting waste.
Lean manufacturing terms, explained.
Help is available to get smaller firms into lean manufacturing.
In-house program guides Engel through supply chain and labor challenges.
Commentary: Your workers are the key to continuous improvement.
Karen Hanna | Senior Staff Reporter
Senior Staff Reporter Karen Hanna covers injection molding, molds and tooling, processors, workforce and other topics, and writes features including In Other Words and Problem Solved for Plastics Machinery & Manufacturing, Plastics Recycling and The Journal of Blow Molding. She has more than 15 years of experience in daily and magazine journalism.
KraussMaffei now building extruders in U.S.
High-tech skills come at high price
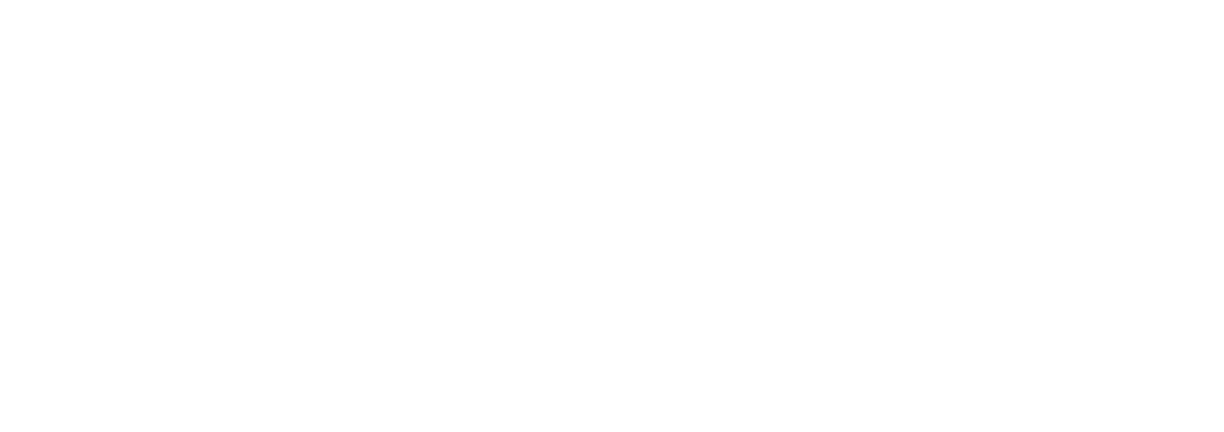