Polyplastics Group: Meeting needs for insulating and conductive materials for EVs
By Bruce Geiselman
Controlling heat and reducing environmental impact are two aims of resins supplier Polyplastics Group in its work with the evolving automotive industry.
The shift toward electric and hybrid vehicles is bringing increased demand for components with insulation properties, said Katsutoshi Kasuya, CEO of Polyplastics USA Inc.
“Polyplastics is working on the development of engineering plastics to meet the need of electrification,” Kasuya said. “Specifically, grades of PPS (polyphenylene sulfide) and PBT (polybutylene terephthalate) are expected to play an active role in the future.”
In February, the company launched sales of a new electrically conductive grade of Duranex PBT for millimeter-wave-radar applications. Duranex PBT 201EB provides the benefit of electromagnetic wave shielding — an advantage that means using it requires less assembly work and cuts cost. It bonds extremely well due to its double-shot molding capability.
In addition to introducing engineered plastics to meet the needs of electric vehicle manufacturing, Polyplastics is working with automakers and suppliers to reduce the carbon footprint and the amount of virgin materials used in vehicle parts. One example of the new kinds of materials it’s released includes bg-POM, a polyoxymethylene made from methanol produced by biomass raw materials.
“In that sense, from the view of carbon neutrality, Polyplastics is actively promoting the development of grades with low PCF [product carbon footprint], such as bg-POM, in addition to working to reduce the carbon footprint of existing grades,” Kasuya said. “From the view of the circular economy, Polyplastics will also promote engineering plastic recycling, starting with recycling sprues and runners of customers.”
Bruce Geiselman, senior staff reporter
Contact:
Polyplastics USA Inc., Farmington Hills, Mich., 248-479-8928, www.polyplastics-global.com
Bruce Geiselman | Senior Staff Reporter
Senior Staff Reporter Bruce Geiselman covers extrusion, blow molding, additive manufacturing, automation and end markets including automotive and packaging. He also writes features, including In Other Words and Problem Solved, for Plastics Machinery & Manufacturing, Plastics Recycling and The Journal of Blow Molding. He has extensive experience in daily and magazine journalism.
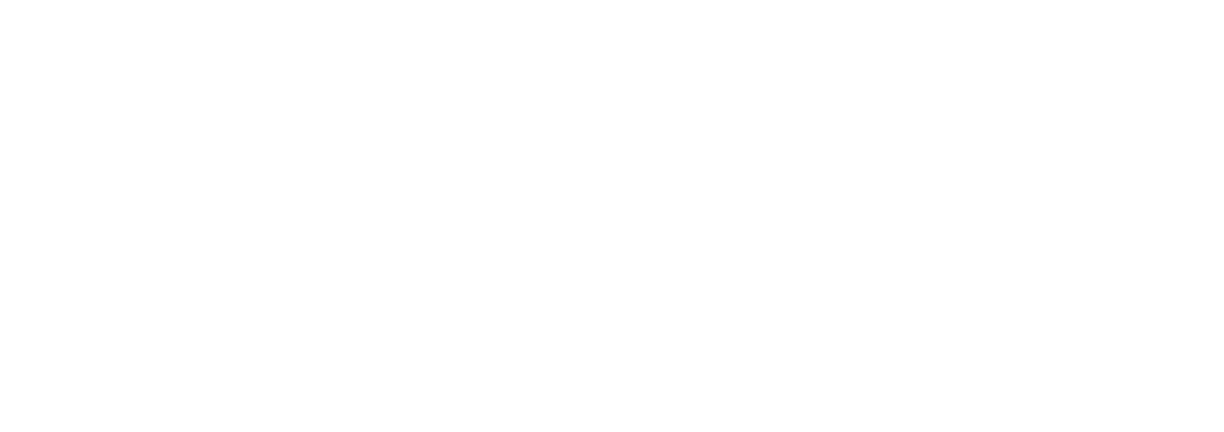