By Karen Hanna
To his dismay, Umberto Catignani, the president of Orbital Plastics Consulting, has seen operators silence notifications and alarms from their molding machines. They just couldn’t be bothered to figure out what was going wrong.
“They don’t want the machine to alarm and keep it running, but they have everything turned off,” he said. “I’ve given up on people like that. I don’t even bother trying to push them into something, because if they can’t even turn on basic alarms, they’re not going to do much data monitoring.”
Whether it’s the micron-by-micron erosion of steel from their molds, or this quarter’s sales figures, manufacturers have massive amounts of data to track. Molding specialists, like Catignani and fellow consultants David Routsis, president of Routsis Training, and Torsten Kruse, president of Kruse Training, say that by leveraging data correctly, plastics processors can be sure their numbers are trending in the right direction.
The alternative can be expensive, as manufacturers can run parts for cycle after cycle without realizing the process is out of kilter.
“I’ve actually done some plant tours for a couple of these companies who are very, very good at all of this, where they are tracking everything, they’re looking at it, and if something goes out of whack, they know about it right away, and either somebody’s at the machine, or somebody gets paged automatically, and they run over to it and look at it,” Routsis said. “But others … they go through and produce parts overnight and realize that they’re all bad when they come in in the morning.”
Of those two extremes — the manufacturers that are tracking, monitoring and re-adjusting in real time, and those that aren’t — the winner is easy to predict, reaping the rewards of proper data analysis.
“By focusing on the right data points and avoiding unnecessary distractions, processors and mold makers can enhance efficiency, improve quality and stay competitive in an increasingly digital manufacturing landscape,” Kruse said.
Making the most of big data
The consultants say getting started requires focusing at first on just the basics, allowing manufacturers to start charting progress toward continuous improvement.
“Every mold and order can be analyzed and optimized to further enhance the [company’s] bottom line,” Kruse said.
The best metrics, Catignani said, are “what people are using. A lot of times, they’re using nothing.”
While setting up a process correctly takes analysis and time, the cost of putting forth no effort can be higher, he warned.
“If you take the time up front to set it up, you’ll make better parts more consistently down the road. So, if you were to do some monitoring, there’s less chance of a quality spill, the time involved going back to, where did you start making bad parts? If you’re not monitoring anything, how do you even know where to go back? Do you go back a day? To when you changed that mold?” he said.
To keep processes on track, Catignani recommended watching a few data trends in particular: cycle time, injection time, peak pressure, switchover pressure or velocity-to-pressure transfer, melt cushion, plasticizing time.
He said molders also can benefit from readings involving the barrel heater zone or feed throat temperature.
In-cavity pressure and temperature sensors represent a further advance. While pricey, the technologies are especially important in medical molding for product traceability.
Placing flush-mounted temperature sensors in multi-cavity tooling can help processors identify cavities that aren’t filling evenly so they can work to achieve a better filling balance. Molders can link these sensors to their hot runner controller, so it can make automatic adjustments based on temperature.
With a cavity temperature sensor acting as a “ ‘proximity switch’, valve gates can be opened sequentially or even [activate] a mold action such as setting or pulling cores,” Catignani said.
If the process has degraded material, the barrels might be too hot, or moisture levels in the material might have been out of spec when it was molded. If the fill time is starting to fluctuate, molding pressure might be out of spec, Catignani said.
He warned that relying on vision and quality-control systems alone to determine that processes have drifted is costly, a path too many molders take.
“They’re not capturing any almost ... no data, and just running because they’re maybe using vision systems and they have 100 percent inspection, things like that, and rely on that, which is fine,” he said. “You want to make sure you don’t send any bad parts, but, as a first step, what’s wrong with setting up the machine to tell you that you’re trending that you might start making bad parts?”
In addition to process data like pressure, temperature, and cycle and cooling times, Kruse suggested watching tool wear and maintenance data, material usage and waste, machine utilization and downtime analytics, and energy consumption.
Both he and Catignani noted that few plastics processors have tapped into the insights they might be able to glean from statistics related to plants’ energy consumption and environmental impact.
“With increasing sustainability regulations, tracking carbon footprint and emissions can help companies stay compliant and competitive,” Kruse said.
With such data, Catignani said processors can even land support from their utility companies for upgrades.
But, according to Kruse, those aren’t the only metrics manufacturers overlook.
Two other sets of data that can yield results, in terms of overall plant improvement, are predictive analytics and customer feedback.
“Many manufacturers still rely on reactive rather than predictive maintenance, leading to unexpected breakdowns and higher costs,” Kruse said.
Looking beyond the plant, he said manufacturers also can benefit from listening to their customers.
“While internal quality checks are common, incorporating real-world customer feedback data can enhance part production, product design, mold design and performance,” Kruse said.
Overcoming challenges
But not everyone’s leveling up. The obstacles to using the data that’s collected across the plant include technical issues, as well as workforce challenges.
No matter the hurdle, the consultants say the effort to leverage data is worth it, and Kruse noted there’s never been more of it available.
“However,” he said, “the key question is: Are they using this data effectively? While many companies are leveraging data to optimize operations, reduce costs and improve product quality, there are still gaps in utilization and focus.”
Catignani acknowledged getting started can feel overwhelming.
“I think a lot of molders are scared. Maybe that’s not the right word, maybe intimidated. Like when I teach classes and I just show the curve from the machine itself — pressure, screw position and injection speed — and ask, ‘Guys, have you looked at the machine graphs?’ ‘No, not really, I get a little nervous,’ ” Catignani said. “I’m like, ‘I’m going to show you how to do this.’ ”
Kruse warned against “data distractions.” If the numbers are too granular, or look impressive but have no context and inspire no insight, they’re not useful.
Also, just as overcorrecting while in a skid can precipitate a crash, Kruse said reacting to minor shifts in the numbers can disrupt stable processes.
In some cases, larger processors have an advantage over their smaller competitors, due to the strengths and capabilities of both their machines and their workforce.
For example, processors that run machines made by different manufacturers or in different eras can experience inconsistencies and incompatibilities in communications protocols.
“These machines, they don’t all speak the same language. So, if they want to get data out of them, and they have different manufacturers, sometimes they have to ... see how to get that data out,” Routsis said. “It can all be done. It’s just if they’re running all different ones, it makes it harder for them to get that because it’s going to start costing them money to be able to monitor it.”
“Data silos remain a challenge, with companies not fully integrating information from different software and machinery for a holistic view of operations. It is required to evaluate a companywide data collection software integration to allow to take advantage of all data,” he said.
But leveraging the data requires technological and personnel investments that can be a reach for some companies, especially smaller ones.
In the past few years, Routsis said he’s visited only a few plants, most of them relatively large, and noticed they’d upgraded their fleets to interoperable machines.
But even smaller companies can benefit by harnessing their data and putting it to work.
“It depends on how serious they are about it. It does take time; they do have to look at it,” Routsis said. “There’s also a price that you’re paying for that. What I find is everybody seems to want to do it, but they’re half-heartedly doing it, where the bigger companies tend to say, ‘Yes, we’re going to do this,’ and they’re finding that they’re making more money now because it’s working for them and they can see what’s going on.”
Bridging the knowledge gap
Just as their equipment might require upgrades, companies also might have to invest in their workers. In a lot of cases, Catignani said, companies simply don’t have enough workers with the skills to draw inferences from the numbers they’re seeing.
A lot of operators don’t know what to do as the process starts to shift outside pre-set parameters. They aren’t sure what data points are most important and what adjustments to make.
So, while one operator might have set up a process within relatively narrow process windows, the next person running the machine might see trends start to slide — and ignore them.
“Part of the problem is not everyone has the same knowledge, and so if I [establish these process] windows, give an alarm, the alarm goes off and scraps the part. Another guy comes over, trusts the process, is really not sure what he should change to stay within that window, and so he starts to increase the window so much, it really doesn’t mean anything. That’s what unfortunately tends to happen,” Catignani said.
Teaching workers to understand what they’re seeing and how to respond to data fluctuations is critical.
“I think it comes back to training people how to do this, and when the process moves out of that alarm, what’s the most efficient way to tweak the process,” he said.
When he’s encountered experienced workers who think they’ve mastered the art of molding but can’t explain the science, Catignani said he confronts them with the data, explains it and challenges them to see how letting it be their guide can improve their process.
“I remember hearing a comment from a job, a plant, I did some work at. They bought a bunch of molds, and they put sensors in all the molds. And the guy that came to help set this stuff up, one of the first things, he says, ‘You guys don’t need all this stuff,’ because he’s never used it, but he’s technically right because he’s [gone] 30 years without it. But there’s always room for improvement. So, if we could use it to mold better, more consistent parts and get data, why not?” Catignani asked.
From one machine to the next, the goal is consistency and efficiency.
“Scientific molding is trying to duplicate the process, regardless of the machine,” Catignani said.
Meanwhile, Routsis is experimenting with artificial intelligence (AI) and fascinated by the ways manufacturers are starting to leverage it. While he said companies are mostly using it to differentiate between good and bad parts, it could have varied applications, such as providing assistance in programming robots or analyzing data.
He said big companies, in particular, are looking to combine it with vision systems.
Like Catignani, Routsis emphasized the importance of training and hiring skilled workers. Younger workers have exposure to the technologies, like AI, that will be important to manufacturers in the years to come.
“I think a lot of these companies do that and go out and get some of the younger ones who have been starting to use this in colleges and trying it all out, it would help them get to the point they want to a lot faster,” he said.
But while he said he’s looking to AI to create training packages to offer to his customers, Routsis acknowledged he’s not ready to go all-in on the technology.
His reasoning reflects the notion that “good enough” won’t cut it — whether you’re creating workforce development materials, as he does, or producing parts, as his clients do.
“I’ve experimented with pieces of it. … Some of it still has to be checked, because obviously, you don’t want to put a bad product out, and I don’t want a product that’s 95 or 98 percent, I want it to be 100 percent when it goes out,” said Routsis, who recommended manual intervention and oversight when using AI.
Embracing improvement
As manufacturers increasingly turn to data to drive decisions, competition could heat up among molders. Those who ignore data could already be paying a high price — even if they don’t realize it.
“I think it’ll be tougher for them, and they won’t make the margins and stuff like that. I don’t think it will eliminate them, but … I think in the long run, it’ll help them. But you have to hop into it,” Routsis said.
Catignani urged molders to dig into their numbers. They might be surprised to see they’re not performing as well as they might think. And however they’re doing now, they could be doing better — when they turn to data to inform their decisions.
Like Routsis, he cautioned against the notion that performing in a way that’s good enough now will prove sustainable in the future. Molders have to push for improvement.
“I think you’re putting your head in the sand if you’re just saying, ‘Well, I’m making money and we’re doing good.’ I think you always have to try to do better. ... So, I would push the guys [by saying], ‘How do you really know what you could achieve or not, until you try?’ ”
Contact:
Kruse Training Inc., Naples, Fla., 239-353-6468, https://krusetraining.com
Orbital Plastics Consulting, Atlanta, 404-849-6714, www.orbitalplastics.com
Routsis Training LLC, Nashua, N.H., 978-957-0700, www.traininteractive.com
Karen Hanna | Senior Staff Reporter
Senior Staff Reporter Karen Hanna covers injection molding, molds and tooling, processors, workforce and other topics, and writes features including In Other Words and Problem Solved for Plastics Machinery & Manufacturing, Plastics Recycling and The Journal of Blow Molding. She has more than 15 years of experience in daily and magazine journalism.
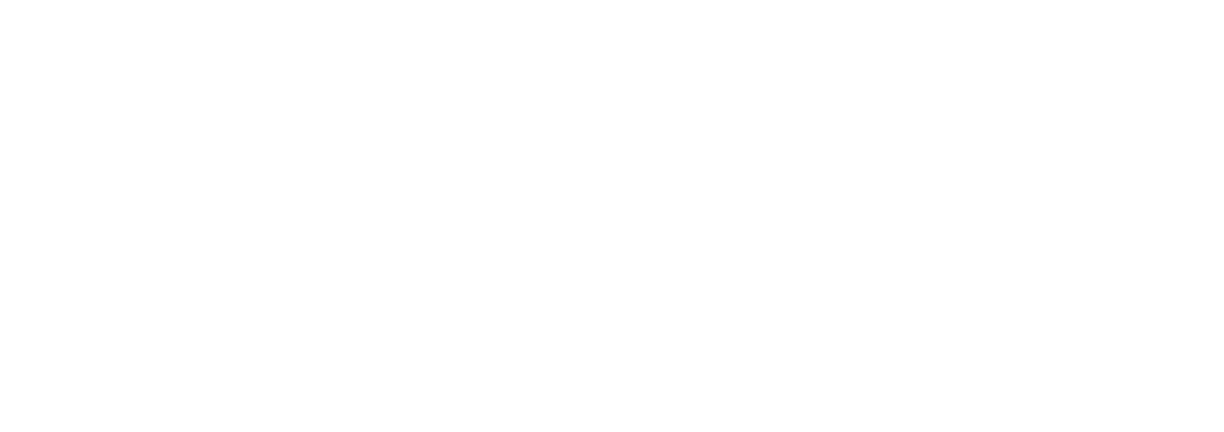