EV transition, cost pressures pose risks for auto parts suppliers
By Karen Hanna
As the United Auto Workers (UAW) strike recedes into suppliers’ rearview mirror, auto-industry analysts are issuing a sobering picture for the outlook of both parts manufacturers and the makers of molds and tooling. Experts say plastic parts manufacturers need to work with OEMs to be sure there’s a place for them as the industry transitions from internal-combustion-engine (ICE) vehicles to electric vehicles (EVs).
“I think now’s a good time — as the strike is coming undone, and you need to start talking to your customers above you, regarding what the anticipated volumes are going to be in the coming weeks and how fast things are going to ramp [up] — is to take time and say, ‘Hey, let’s sit down and talk about the EV in general, and how much of our mutual business is dependent on that,’ ”said Terry Onica, a supply chain expert and the director for automotive business for QAD, which offers manufacturing enterprise resource planning software.
In an Oct. 31 webinar detailing the outlook for manufacturing, Laurie Harbour warned of “tremendous vulnerability in the supply chain.”
The UAW strike — which could come to an official end in the next few days as members vote on new contracts with Ford Motor Co., General Motors (GM) and Stellantis — represents just the latest disruption to hit the volatile auto industry. But it won’t be the last, said Harbour, the president and CEO of Harbour Results Inc., which provides consulting services to manufacturing companies, including molders and mold makers.
Center of the strike
Determining the strike’s full impact is difficult, according to an analysis published Oct. 19 by the Plastics Industry Association. Harbour said returning to full operations could take some time.
According to Harbour, about 11,000 workers for parts suppliers were forced off the job, at least temporarily. Toward the strike’s end, the UAW’s cascading walkouts paralyzed about 50 percent of the Big Three’s normal output — affecting about 11,000 vehicles a day.
Around 45,000 UAW members participated in the strike.
With tentative agreements coming around the six-week mark, the strike is similar in duration to strikes in 1998 and 2019. According to PLASTICS, in the two months of the 54-day 1998 strike, the Industrial Production Index for plastics and rubber products manufacturing dipped 0.5 percent and 0.3 percent, respectively. The 39-day 2019 strike — which targeted only GM — saw dips of 1.0 percent and 0.7 percent.
According to PLASTICS, the Industrial Production Index for plastics product manufacturing increased by 1.9 percent in September, but was 4.5 percent lower than the previous year.
Return to work
As suppliers look to fill orders from the OEMs, the strike’s impact on labor and wages could reverberate beyond the Big Three, according to Harbour and Onica.
“Six weeks is a pretty significant amount of time,” Harbour said. “If you were a supplier and you were dedicated to any one or more than one of these facilities, and a significant portion of your plant was down or you had to lay off quite a few people in that six-week period, it’s going to take some time to ramp back up because you have to purchase material, you have to make sure you have all of your labor back.”
Recovery will require communications, said Onica, whose company has offered a 13-point restart checklist.
In an interview while the strike still was taking place, Onica warned the strike — along with supply chain disruptions that have included the COVID-19 pandemic and the computer chip shortage — could deter workers from entering or remaining in the auto industry. For manufacturers, that could cause further destabilization.
“I worry how much they can handle. And then on top of that, the other thing I worry about a lot, too, is just how much more is this going to hurt automotive manufacturing?” Onica said. “Because it doesn’t seem like a stable environment to come to work every day.”
The UAW’s wage wins also could spell trouble for manufacturers further down the supply chain, Harbour said.
Before the strike began, the Big Three were spending $64 an hour on employee wages and benefits, Harbour said.
Meanwhile, she said, “The Japanese are about 55 [dollars] and companies like Tesla are about 45 to 50 [dollars]. So, these increases in wages are going to take them up overall in terms of their hourly rate and their competitiveness, which I also believe is going to affect market share of the OEMs because it means prices will continue to rise for vehicles.
“If you look at the supplier impact, obviously, [the] initial impact is reduction in revenue over the last six weeks. ... The longer-term implication to the suppliers is that this is, unfortunately, probably going to mean that some suppliers won't make it through.”
She noted that mold and die makers’ wages used to be among the best in the industry, but they’ve fallen far behind.
Having settled with the Big Three, UAW President Shawn Fain has said he is setting his sights on other, non-unionized manufacturers within the supply chain, specifically calling out Tesla.
“The other thing that probably concerns me the most is that the UAW is going to absolutely target new OEMs,” Harbour said. “So, he was very successful with the D3 [Detroit Three], and so now that the president of the union gets to say, ‘Hey, guys, look at what I won for the D3. I can do that at your plant, Nissan or Honda or Volkswagen, Toyota, or even other industries — heavy truck and agriculture and things of that nature.’ ”
Electric transition puts suppliers at risk
Having absorbed reductions in output that have eaten into automotive inventories already far below their 100-day, pre-pandemic levels, the Big Three have reported the impact to third-quarter earnings could total hundreds of millions of dollars, Harbour said. In its third-quarter earnings report, Ford, for example, projected that the strike will cost it $1.3 billion this year. In light of record personnel-cost increases detailed in their tentative agreements with the UAW, Harbour said automakers are motivated to cut costs elsewhere, even as the industry goes all-in on EVs.
Onica offered a stark warning for lower-tier suppliers that have not gotten serious about supporting the transition to EVs.
“That’s the big takeaway that I’m always trying to make sure that lower-tier suppliers are thinking about is time’s going to run up pretty soon. If you’re left there without a strategy, you’re at risk of being bankrupted,” she said.
For the makers of molds and tooling, as well as parts manufacturers, the transition represents both opportunities and risks. On one hand, OEMs need to retool; on the other hand, they could look overseas to fill their needs. And, while EVs require many fewer parts than ICE vehicles, automakers also are cutting back on the trim levels of ICE vehicles — meaning the volume of parts needed for EV and ICE vehicles might even out.
OEMs are working hard to consolidate, according to a Nov. 1 post from the Motor & Equipment Manufacturers Association, “Why Every Supplier Needs an EV Strategy – Ahead of the Curve – November 2023.” For example, Toyota found a way to replace 86 parts and 33 processes into a single part, driving cycle times down from 30 minutes to 100 seconds.
“Simply put,” the post states, “in many cases, traditional components supplied to an EV program may be over-engineered and represent a cost penalty compared to purpose-built components and systems.”
Impact on mold makers
Harbour said American manufacturers have to find ways to become more efficient if they want to compete over the next couple years, when large fleets of new vehicles are expected to storm the market.
“I am bullish that there’s a lot of new products coming in over that four-year period of time, that equates to $25 billion of tools spend, which is like what we saw in 2017 and 2018, two of the largest years in the history of the automotive tool business. So, the wallet [of potential dollars devoted to new tools] available for people to source is significant. The challenge is, where does that wallet gets sourced?” Harbour asked.
In the Oct. 31 Harbour Results webinar, Cara Walton, director of market intelligence for Harbour Results, discussed a survey the company conducted in mid-September of about 300 manufacturers. Based on a review of their 2022 balance sheets, Harbour Results concluded about 29 percent of the manufacturers are overleveraged or not making a sustainable amount of money. That’s up from 19 percent the previous year.
For the makers of molds and tooling, capacity utilization sits around 61 percent, and quoting activity is down, Walton said.
Despite strong demand for goods, manufacturers are struggling with inflationary pressures and difficulties filling jobs, Walton said.
“What we’re seeing is that despite them improving efficiency on average — they’re getting more efficient on their shop floors — in many cases, they’re still not able to make as much money as they were back in that 2017 and 2018 timeframe,” she said. “This is where it’s kind of that death-by-a-thousand-cuts mentality, that they’re paying higher interest rates, they’re paying higher wages in some cases, everything is costing them more money than it did back in 2017.”
According to Harbour, between 2002 and 2022, Chinese imports of molds and tooling grew over 1,500 percent, from $35 million to $562 million. Meanwhile, since 2008, the U.S. molds and tooling industry has lost more than 50 tooling shops.
However, Harbour said the U.S. industry still has capacity to do the work.
“We currently today have between 9 [billion dollars] and $10 billion of automotive tool capacity alone, not counting medical and consumer goods and everything else,” she said.
But, with low-wage labor overseas and China producing tooling that’s cheaper than American tooling even in the face of 25 percent tariffs, U.S. tool makers will need help from OEMs to survive.
“We need them to be critically supportive of our industry here in order for us to continue to have a viable industry five to 10 years from now,” Harbour said.
Negotiating the road ahead
Harbour warned of layoffs and price challenges to come. Those issues could stall the launch of some vehicles — the ramp-up from the strike alone could take the next couple quarters — but they won’t prevent the EV transition.
In particular, she issued a challenge to the makers of molds and tooling.
“The shops have to fight for their own viability by improving their business,” she said. “And the data shows us that they’ve not done everything that they can to improve their business. Once they can do that, then they can show data to the OEMs and their customers about why we should make tools here.”
For too many suppliers, the threat of bankruptcy is very real, according to Onica.
To survive, she said, “You have to transform your company. Do you need to move to another industry?”
To steer through the challenges ahead, she said plastics processors must probe some big questions, as the EV and BEV transition continues.
“There’s some time left, but not a lot of time to really be thinking through this issue,” she said. “What are you going to do? Are you going to diversify? Are you going to transform your business? Are you going to divest?”
Contact:
Harbour Results Inc., Southfield, Mich., 248-552-8400, www.harbourresults.com
Plastics Industry Association, Washington, 202-974-5200, www.plasticsindustry.org
QAD Inc., Santa Barbara, Calif., 805-566-6100, www.qad.com
Karen Hanna | Senior Staff Reporter
Senior Staff Reporter Karen Hanna covers injection molding, molds and tooling, processors, workforce and other topics, and writes features including In Other Words and Problem Solved for Plastics Machinery & Manufacturing, Plastics Recycling and The Journal of Blow Molding. She has more than 15 years of experience in daily and magazine journalism.
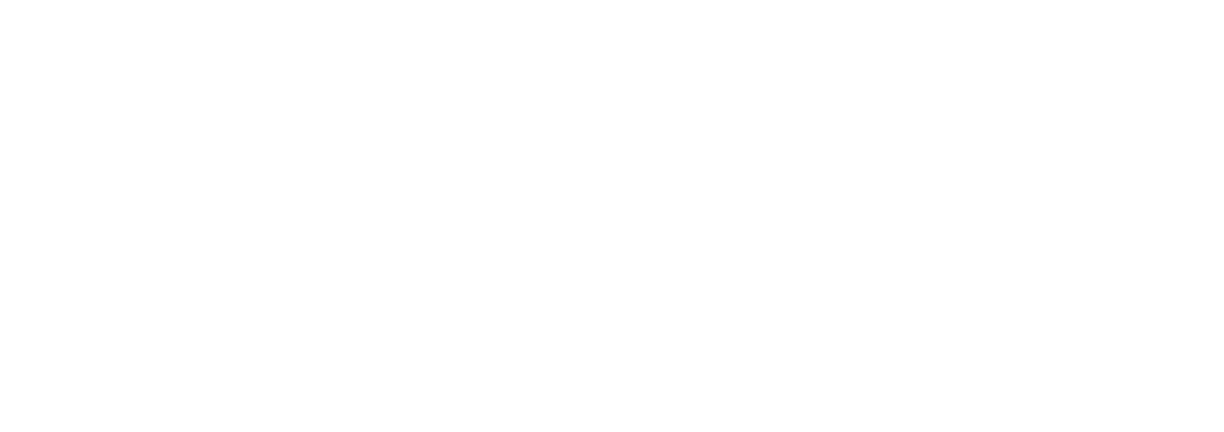