Engel will feature a production cell at K 2019 that will use its organomelt process to produce lightweight, thermoplastic composite parts showcasing the latest innovations in car door materials. The company previewed the process on June 24 during a press conference at its headquarters in Schwertberg, Austria.
This will be the first production cell to use infrared radiation to heat and form three fiber-reinforced sheets of various thicknesses and mold them into a demonstration part with a high-quality surface in the same injection molding process, the company said. The system will be equipped with three Engel easix articulated robots operating simultaneously.
“Thermoplastic composites are growing in importance when it comes to lightweighting in the automotive industry,” said Norbert Müller, head of Engel’s Centre for Lightweight Composite Technologies.
There are two reasons for this. Using thermoplastics makes it possible to efficiently form fiber-reinforced prepregs, which reduces unit costs. Also, the exclusive use of thermoplastics makes it easier to develop recycling strategies.
“Returning composite components to the material loop at the end of their service life is one of the priorities for ongoing development in the electric vehicle sector,” Müller said.
Engel will use organomelt, an older process, to achieve new lightweighting goals. In this process, fiber-reinforced thermoplastic prepregs such as sheets and tapes are heated, inserted into the mold, formed and then overmolded with PP.
“In the future, several different prepregs will be combined for each component to tailor the lightweight construction characteristics to the relevant component’s shape, as well as the different stresses on individual areas inside the component,” Müller said. “The production cell at the K show will clearly demonstrate that great potential.”
Engel said this is the only system that can simultaneously process three differently shaped sheets between 0.6mm and 2.5mm in thickness in a fully automated process involving integrated infrared ovens.
OVEN INTEGRATION
One challenge in the process is heating the prepregs. The time they take to heat and cool depends on their thickness. Heating the prepreg quickly without damaging it and getting it to the mold quickly are keys to success, Engel said.
The organomelt production cell will use a duo 3660/800 injection molding machine that includes two integrated ovens. A vertical oven positioned above the clamping unit will heat the 0.6mm-thick sheet so it can get to the mold quickly.
A horizontal infrared oven on a pedestal above the moving platen will be used for the two thicker sheets. Both ovens, which were made by Engel, and the three robots are fully integrated with the molding machine’s CC300 control unit.
All three sheets are heated at the same time. During heating, two robots hold the sheets in front of the vertical radiation field so that they can be placed in the mold after heating. The third robot, located next to the clamping unit, removes the final molded part and also places the prepregs into the mold.
The prepregs are made of glass fiber and PP. When the mold closes, the prepregs are formed and are immediately overmolded with glass-fiber-reinforced PP in the same mold. Reinforcing ribs are shaped on the back of the component and a grain simulating leather is shaped on the side that will be visible to people once the car is assembled.
Bruce Adams, senior staff reporter
Contact:
Engel Machinery Inc. York, Pa., 717-764-6818
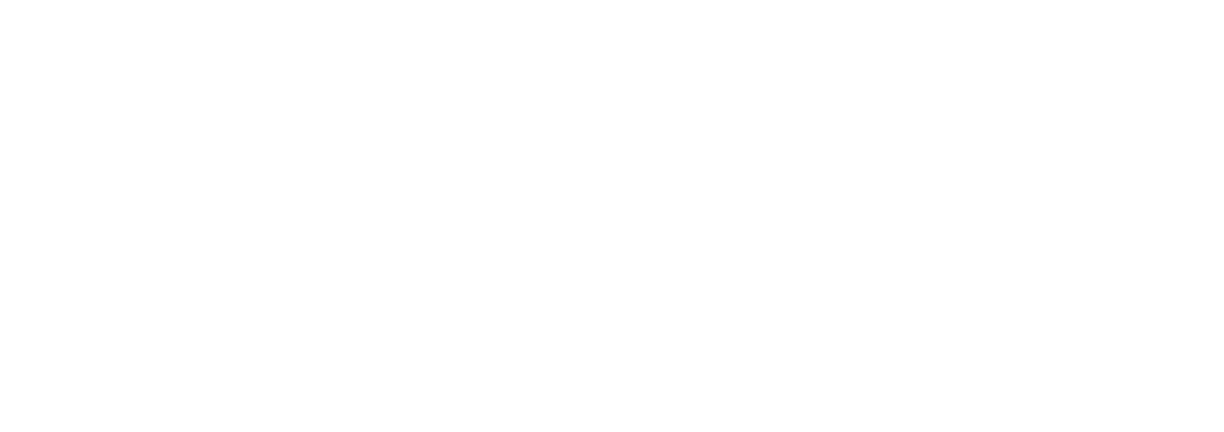