K 2019 gave manufacturers of blow molding equipment a chance to look back — and gear up for the future.
Machines made for general use took their places near models made for specialized niches as the industry celebrated the anniversaries of some companies while looking forward to a future that promises faster cycle times, easier changeovers and greater efficiency.
Bekum
On the 60th anniversary of its founding in Berlin, and the 40th anniversary of beginning operations in the U.S., Bekum Maschinenfabriken GmbH used K 2019 to look ahead. It presented a new extrusion blow molding (EBM) machine for packaging, called Concept 808, that showcased new features that might be included on future Bekum machines.
Clad in a new yellow color for Bekum, the three-layer machine is due to launch commercially late this year, first in Europe and then in the U.S., according to Steve London, Bekum America Corp.’s president and COO. The machine, as configured at K 2019, would cost about $2 million.
The Concept 808 features an optional magnetic system that enables fast mold changes –– without tools or a special mold cart. Molds and blow pins are always changed from the front of the machine. Standard molds can be used with the quick-change system, Bekum said.
Bekum also introduced a new generation of high-output extruders with helically grooved barrels. Extruders are the main energy consumers in any EBM machine, but Bekum used energy-efficient motors and drives, enabling up to 20 percent energy savings.
London said the Concept 808 also features a new, 24-inch control panel. It has an intuitive touch screen that is equipped with Industry 4.0 applications, and displays throughputs and energy, water and air consumption.
London said Bekum also is developing a new line of industrial blow molding machines in its BA series to make such products as L-ring drums and large drums. This has not been an area of focus for Bekum in recent years, but he said the company sees “a window of opportunity” and plans to pursue it.
Magic
Magic MP SpA, Monza, Italy, touted what it calls “the biggest all-electric extrusion blow molding machine in the world,” its new ME-T60-1000D, which offers up to 71.6 tons of clamping force and a 5.2-foot stroke.
At the show, however, Magic ran a smaller version of the machine — an ME-T50-1000D, with a 55-ton clamp and 3.3-foot stroke. The two-cavity, double-station machine molded 20-liter containers that weighed just under 2 pounds and featured a view stripe.
“We can go up to 50-liter containers,” said Pietro Spiga, area manager for Magic North America, noting that the machine on the stand was already sold.
Touting the benefits of all-electric machines, he noted that energy consumption is half that of comparable hydraulic machines, with up to 70 percent lower maintenance costs, and very good repeatability and cycle-time consistency. The machines are suited for processing extrusion blow molding grades of HDPE and high-molecular-weight PE.
Spiga said the company makes about 100 machines a year. It has been active in the U.S. via sales agents for some 30 years, but in 2018 opened its first North American office and showroom to handle sales, service, spare parts and training.
FlexBlow
Lithuania-based UAB Terekas, which operates under the brand name FlexBlow, has introduced a series of two-stage stretch blow molding machines targeting the cosmetic containers sector. The company, which celebrated its 25th anniversary last year, said it developed the new line, dubbed the Beauty series, in response to changing industry needs and to compete with single-stage machines.
The company said that cosmetics makers want containers that have a scratch-free surface, as well as a variety of designs, shapes, colors and necks –– all in ever-decreasing batch sizes. To deliver maximum manufacturing versatility, the company’s new Beauty models offer an integrated solution, enabling a complete production changeover in just 30 minutes from oval, narrow-neck cosmetic bottles to shallow, wide-mouth jars. The machines can be used to manufacture PET and PP containers.
Designed to minimize the possibility of scratches on the preforms, the Beauty machines can be directly integrated with injection molding machines (IMMs). Wide-mouth preforms from an IMM can be fed directly into a Beauty machine, blown into containers, then transported to a packaging machine or filling line without human interaction. Alternatively, FlexBlow’s pick-and-place system can take preforms from boxes and place them into the Beauty machines.
“Because in cosmetics, elegance is everything, the Beauty-series machine comes in an aesthetic white color and premium exterior design,” the company said.
Jomar
A Jomar injection blow molding (IBM) machine designed specifically for molding small PET containers can easily accommodate more commonly used resins such as PP and PE. Operators of the new TechnoDrive 65 PET can change between resins and products simply by swapping out the screw and making some minor adjustments.
Ron Gabriele, global sales and marketing manager, said the new machine builds upon the company’s TechnoDrive 65, a high-speed production model introduced in 2018. With a dry cycle time of just 1.8 seconds, the TechnoDrive 65 PET is one of the fastest IBM machines in the industry, according to the company.
Gabriele said Jomar’s engineers expanded on the original model’s capabilities by adding a more robust plastifier motor and high-pressure valves, while also making other upgrades such as built-in nozzle heaters that he said aid in the processing of PET.
The new machine merges the third and fourth stations often needed in PET blow molding machines, allowing the ejection station to condition the core rods and make sure they are the correct temperature before the core rod is enveloped in PET. Gabriele said this gives the machine the ability to manipulate the core rod temperature and creates optimal processing conditions very quickly. Eliminating the need for a fourth station also saves money on tooling.
The TechnoDrive 65 PET adds the versatility that Gabriele said customers are increasingly demanding, by enabling them to bid for a variety of projects — from PET cosmetic jars to HDPE packers — that can run on the same machine.
Jomar demonstrated the new model at its K 2019 stand, with a six-cavity mold pumping out 50-milliliter (ml) perfume bottles in clear PET. The average wall thickness for a PET bottle made by the TechnoDrive 65 PET is about 1mm, the company said, so it is better suited for molding jars, vials and bottles for the pharmaceutical and cosmetic industries than beverage bottles.
“Before,” Gabriele said, “we couldn’t make the core rods thin enough to make these mascara bottles” –– but the TechnoDrive 65 PET makes that possible.
The base model of the TechnoDrive 65 PET costs about $330,000, Gabriele said. Jomar makes all its machines in New Jersey, using U.S.-sourced components.
The company said it will build and supply both the TechnoDrive 65 PET machine and the mold for any molder intending to use the technology to make PET containers.
Sipa
The latest generation of Sipa's XForm stretch blow molding machines, the XForm GEN4 XP, comes with a new user interface.Sipa North AmericaSipa, a maker of stretch blow molding machines, has upgraded its XForm PET preform injection molding system.
Sipa said that its XForm GEN4 XP provides “a totally new operator experience,” with a 21.5-inch touch screen with high-definition graphics, swipe functions like a smartphone, a multi-function control knob for one-handed operation and fast response times.
The new technology is available on machines with clamping forces of 276 tons, 386 tons and 551 tons, with molds with up to 96, 128 and 180 cavities, respectively. According to the company, the machines boast short cycle times.
Robert Grace, contributor
Contact:
Bekum America Corp., Williamston, Mich., 517-655-4331, www.bekumamerica.com
Jomar Corp., Egg Harbor Township, N.J., 609-646-8000, www.jomarcorp.com
Magic North America, Whitmore Lake, Mich., 734-358-7722; www.magicnorthamerica.com
Sipa North America, Atlanta, 404-349-3966, www.sipasolutions.com
Terekas UAB, Kretinga, Lithuania, 370-445-51431, www.flexblow.com
High-tech skills come at high price
So, you need a new ERP. Now what?
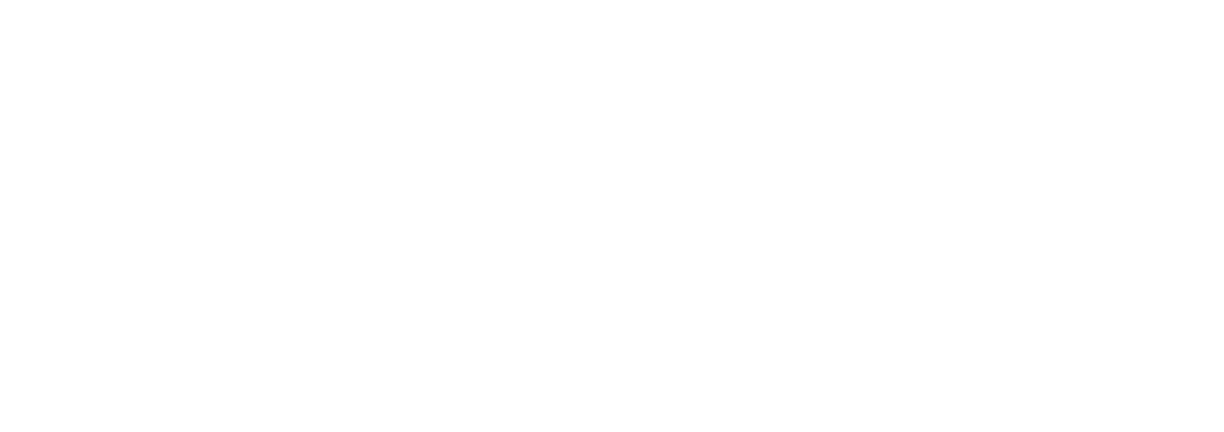