By Bruce Geiselman
Conair has significantly sized up, with a new line of downstream processing equipment and tooling that can extrude PVC and polyolefin pipe with as many as five layers and outer diameters of up to 24.9 inches.
The 2-foot-plus maximum diameters possible with the new PipeMaster line represent a new frontier for the company, which until now only manufactured products for pipe measuring 8 inches or less, said Ernie Preiato, Conair’s VP of extrusion.
“For some time, Conair has been looking at what it would take to expand our pipe extrusion offering to deliver large-diameter pipes,” Preiato said. “We heard from the processors [that] if we were going to make such a move, they would be looking to us to provide them with the following: ruggedness and durability; cost-competitiveness; a complete line of equipment and tooling; and U.S.-based sourcing, sales and service.
“As you know, there’s a lot of good-quality equipment in the market that meets some but not all these requirements, especially the part about being cost-competitive and offering a comprehensive line from one source. If you could get those right along with the others, we felt we would have a winner. Well, now, we feel that we have met these requirements.”
Conair designed the PipeMaster line to meet the fundamental needs of processors, he said.
“This equipment — spray tanks, haul-off units, saw cutters and drop-offtables — combines very rugged construction with simple but well-engineered controls,” he said. “It is complemented by an extensive range of the extruder tooling, including pipe dies and calibration sleeves, that most processors need but often have difficulty finding or building at a competitive price.”
The PipeMaster extrusion equipment line also includes:
Monolayer and multilayer pipe extrusion dies optimized for different material types and for pipe diameters of 2.5, 4.3, 6.2, 9.8, 15.7 and 24.9 inches. Outputs rates range from 550 to 3,520 pounds per hour. Interchangeable die pins and nozzles allow dies to produce multiple sizes of pipe.
A range of calibration tools with options for dry sizing or water-ring cooling and sizing.
Cleated puller/haul-off units that automatically synchronize speed with extruder screw speed control.
Servo-driven pipe cutting units synchronized to line speed.
Pneumatically operated pipe-tilting/dump-off tables synchronized to line speed.
To demonstrate the new technology, Conair has built a new 6-inch pipe extrusion line at its extrusion laboratory and pilot plant in Pinconning, Mich.
Bruce Geiselman, senior staff reporter
Contact:
Conair Group, Cranberry Township, Pa., 724-584-5500, www.conairgroup.com
Bruce Geiselman | Senior Staff Reporter
Senior Staff Reporter Bruce Geiselman covers extrusion, blow molding, additive manufacturing, automation and end markets including automotive and packaging. He also writes features, including In Other Words and Problem Solved, for Plastics Machinery & Manufacturing, Plastics Recycling and The Journal of Blow Molding. He has extensive experience in daily and magazine journalism.
Request More Information
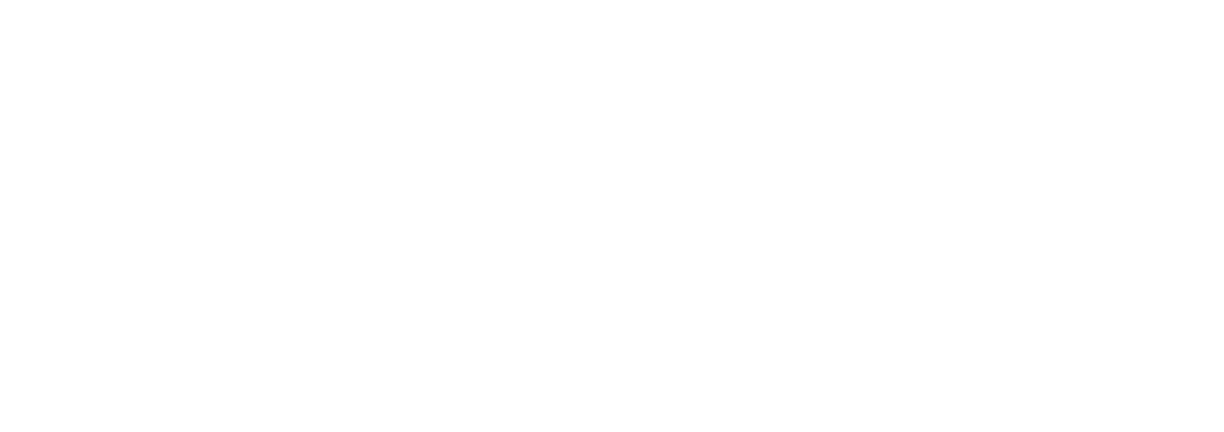