US Extruders expands Med-Ex line of medical extruders
US Extruders has expanded its Med-Ex line of single-screw extruders for the medical market.
The company has rolled out its Med-Ex Elite model to replace its first Med-Ex extruder, which it introduced last year. The company also launched three other Med-Ex models.
“In the medical industry, there are different levels of requirements,” US Extruders President Bill Kramer said. “There are some people who need a machine that goes into a clean room, and they really need to have a lot of features for that. At the other extreme, there are people who just want a simple, basic extruder but maybe painted white and maybe with some stainless steel in areas that allow them to keep the machine looking clean, but they’re not looking for all those special features.”
The top-of-the-line model is the Med-Ex Elite, which features stainless-steel surfaces for easy wipe-downs. Its swappable barrels can range from 0.5 inch to 1 inch in diameter and have toggle clamps that are easy to open and close, making barrel changes uncomplicated.
The Med-Ex Elite is similar to the company’s first Med-Ex extruder but has design changes that include a covering where the barrel joins the gearbox to simplify cleaning.
Every model in the line, other than the entry-level Med-Ex Classic, can operate at temperatures of up to 900 degrees, allowing the extruders to process high-temperature resins such as PEEK.
The Med-Ex extruders also are available with a corrosion-resistant option that allows them to process fluoropolymers, which require high temperatures and are highly corrosive to metals containing iron. The corrosion-resistant design protects all surfaces that come in contact with the melt.
The Med-Ex Elite comes with a precision servo motor. It is designed so that wires running from the machine panel to the melt pump and head are concealed and accessible via a door.
A virtual pressure measurement feature is standard on the Med-Ex Elite.
“Virtual pressure measurement eliminates the transducer,” Kramer said. “The transducer in the barrel of a small machine is a relatively large hole in the barrel, so it creates a large collection place for material. It is a contaminant point. The material can sit there and degrade. Getting rid of that hole is good for some sensitive materials. The way we do that is we have a sensing device at the back of the machine, and we sense the amount of force pushing back on the tip of the screw. … It keeps the machine much cleaner and eliminates stagnation in the barrel.”
The extruders come with the ProControl Medical touch-screen controller, a comprehensive HMI. The controls are highly customizable and facilitate barrel swaps.
The Med-Ex Flex extruder includes many of the same features found in the top-of-the-line Elite. It is available with the option of switching between 0.5-inch and 1-inch barrels, or between 0.75-inch and 1.25-inch barrels.
It also has toggle clamps that are easy to open and close and a precision servo motor. However, it does not include stainless-steel surfaces or virtual pressure management as standard.
The Med-Ex Compact has a gearless direct drive and is designed for installations with space limitations, Kramer said. The Compact measures 68 inches long and 17 inches wide with widely spaced casters in the back for stability.
The Med-Ex Classic is the most economical model in the line. The barrel can be air- or water-cooled. It is available with either the ProControl Medical touch-screen controller or a discrete controls option.
“Our Classic series is just a basic extruder that has a few features for the medical industry, but it looks like just a typical extruder,” Kramer said. “It looks like an extruder you might see in a profile shop.”
Med-Ex extruders are suitable for producing medical tubing, catheters, sheet and profiles, Kramer said.
Bruce Geiselman, senior staff reporter
bgeiselman@plasticsmachinerymagazine.com
More information:
US Extruders, Westerly, R.I., 401-584-4710, www.us-extruders.com
Bruce Geiselman | Senior Staff Reporter
Senior Staff Reporter Bruce Geiselman covers extrusion, blow molding, additive manufacturing, automation and end markets including automotive and packaging. He also writes features, including In Other Words and Problem Solved, for Plastics Machinery & Manufacturing, Plastics Recycling and The Journal of Blow Molding. He has extensive experience in daily and magazine journalism.
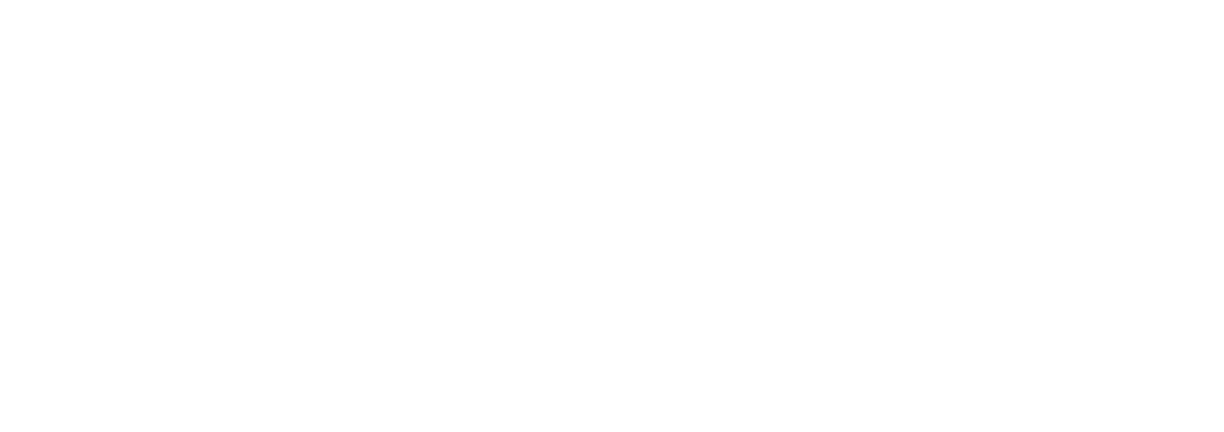