CPM Extrusion Group’s first field trials of its patented High Performance Elements (HPEs) in twin-screw extruders increased production by 20 percent when compounding HDPE for pipe.
As a result, the company is now marketing the screw elements for use with twin-screw extruders.
The asymmetrical shape of CPM’s screw elements results in thorough compounding but generates less frictional heat.CPM Extrusion GroupThe screw elements previously had been limited to use on CPM’s RingExtruder RE, a 12-screw extruder developed by Extricom GmbH, a company that CPM purchased in 2017. The HPEs, which replace traditional kneading elements, are asymmetrical instead of the typical symmetrical shape. Their unique design results in thorough compounding but generates less frictional heat.
“The geometry of the elements themselves was modified to promote elongational mixing or elongational flow, which is very difficult to achieve in a twin-screw extruder,” said Adam Dreiblatt, CPM’s director of process technology. “It’s the Holy Grail — everybody wants to do this.”
CPM suspected the HPE technology developed for the RingExtruder RE could be used on its twin-screw extruders for compounding heat- or shear-sensitive resins. However, the company wanted proof of its effectiveness before marketing the technology for use in twin-screw extruders.
Tests over the past year by a CPM customer have proved the screw elements can boost production rates when compounding heat-sensitive resins.
“One of those is in the highest-viscosity stuff you can imagine, where a twin-screw will generate so much frictional heat it will either degrade the material or reduce the [extruder] capacity,” Dreiblatt said.
The elements were tested on a 92mm twin-screw machine processing HDPE with pigments for use in high-pressure water pipe. Because the material has a high melt viscosity, screw speed must be kept low to minimize the shift in melt flow and still provide excellent dispersion, according to CPM.
Replacing traditional kneading elements with HPEs produced compounds with the same dispersion quality but with a lower melt flow index, which equates to less shear degradation under the same operating conditions, Dreiblatt said. This allowed the machine to operate at a higher screw speed, resulting in 20 percent higher capacity.
HPEs currently are being tested in the field for other applications where elongational mixing can provide increased productivity; CPM plans to release those results once the trials are completed.
Bruce Geiselman, senior staff reporter
Contact:
CPM Extrusion Group Traverse City, Mich., 231-947-6400,
Bruce Geiselman | Senior Staff Reporter
Senior Staff Reporter Bruce Geiselman covers extrusion, blow molding, additive manufacturing, automation and end markets including automotive and packaging. He also writes features, including In Other Words and Problem Solved, for Plastics Machinery & Manufacturing, Plastics Recycling and The Journal of Blow Molding. He has extensive experience in daily and magazine journalism.
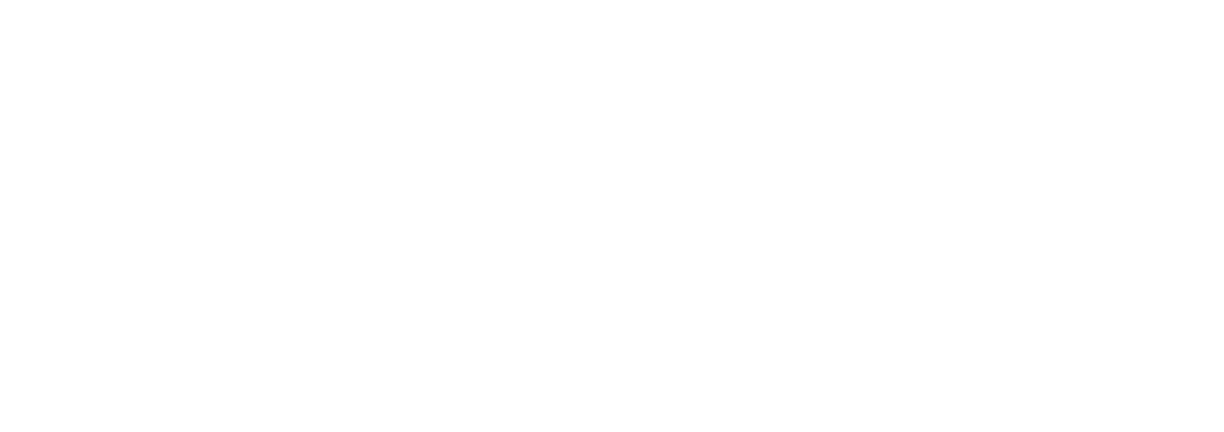