ST BlowMoulding launches dual-head machine aimed at U.S. market
In the wake of NPE 2021’s cancellation, ST BlowMoulding SA opted for a recent web exhibition to introduce its ISIT 1320 dual-head blow molding machine to the North American market.
The company had planned to present the machine at the Orlando trade show, which was canceled because of the pandemic. The company designed the machine to meet the needs of North American manufacturers of small- and mid-size automotive components, said Luca Bertolotti, an engineer and technical board member with ST BlowMoulding. European companies still favor single-head machines, which are better suited for small-batch production, he said. The ISIT 1320 dual head is particularly well-suited for producing car ventilation and air conditioning ducts, according to the company, which is headquartered in Switzerland and has a facility in Italy.
“We see that the North American market is demanding and asking for the dual-head configuration, so we want it to be available to them,” said Ernie Hollo, president of Hollo Plastics Equipment Inc., based in Northfield, Ohio, which represents ST BlowMoulding in the U.S. and Canada.
The company has introduced several features that boost the machine’s functionality. Each head has a top blow device, the most straightforward alternative to a bottom blow stand, the company said. Heads are adjustable side to side, and their center distance is variable to fit asymmetric cavities and minimize flash. Take-out grippers have been designed with pneumatic compensation to prevent arm deflection.
The machine is equipped with a removable access cage for an ergonomic die and core changeover. In addition, the operator is aided by a swing arm to support the tooling during changeovers.
ST BlowMoulding, when designing the ISIT 1320, aimed to improve ergonomics.
“As an example, the takeout device we designed moves the part down to the operator, avoiding some unnatural body movements,” Bertolotti said.
The takeout device lowers large parts down to the operator, so workers don’t have to reach up to retrieve the parts, Hollo said.
The takeout device has a laser-scanning system that ensures that no one is standing in the way of the parts that are being lowered, Bertolotti said.
A new interface for the machine control unit is intuitive and easy to operate, Bertolotti said.
“Let’s put it this way, it looks more and more like a smartphone,” Bertolotti said during the web presentation. “You don’t have to deal with complex menus to navigate through.”
The ISIT 1320 is equipped with a 200-ton clamping unit, and is designed to work with foaming technology, a company spokesman said. Each accumulator head has a 10-liter shot capacity, and each one is fed by two extruders, each 75mm in diameter. The two heads and the closing unit allow the production of two parts at the same time. The parts can be the same product or not, providing that the cycle time of the two products is similar, the company said.
The ISIT 1320 Dual Head achieves significant energy savings with an innovative hydraulic power pack equipped with a pre-filling cylinder and variable-speed pumps that minimize the energy needed for clamping and motion.
Bruce Geiselman, senior staff reporter
Contact:
Hollo Plastics Equipment Inc., Northfield, Ohio, 330-467-9595, [email protected], https://www.st-blowmoulding.com/
Bruce Geiselman | Senior Staff Reporter
Senior Staff Reporter Bruce Geiselman covers extrusion, blow molding, additive manufacturing, automation and end markets including automotive and packaging. He also writes features, including In Other Words and Problem Solved, for Plastics Machinery & Manufacturing, Plastics Recycling and The Journal of Blow Molding. He has extensive experience in daily and magazine journalism.
Plastics Hall of Fame seeks nominees
Amcor, Berry Global will merge
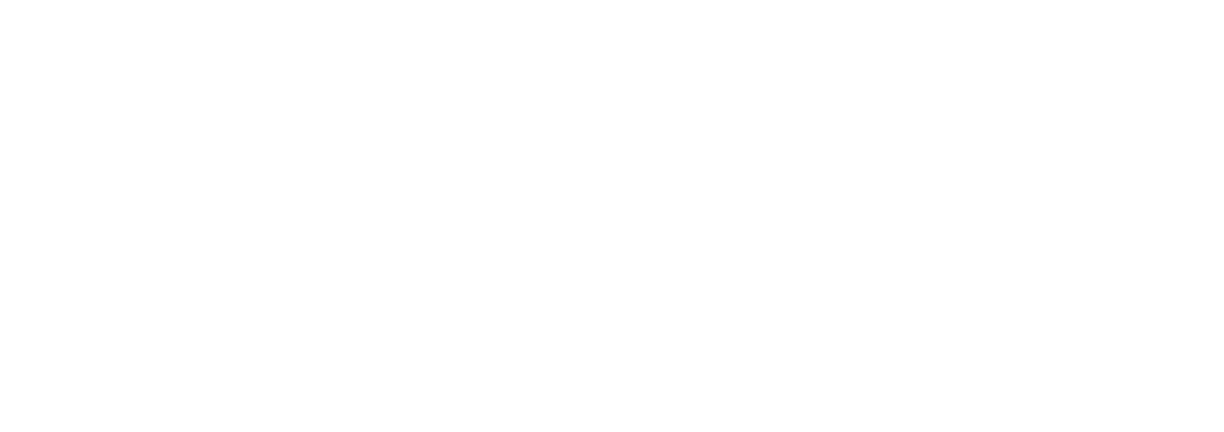