Extruder manufacturer Battenfeld-Cincinnati has sold about a dozen of its multilayer feed blocks for making coextruded thermoforming sheet since the device was introduced, and the company is using feedback from its initial customers to tweak the original design.
"Of course, we optimized the feed block based on the experiences we got out of the field," Henning Stieglitz, CTO at BC Extrusion Holding, the holding company of Battenfeld-Cincinnati Germany.
However, the company said no major upgrades have been needed for the MLA 2E3L Bolt feed block for the extrusion of three-layer thermoforming sheet, which was introduced in 2016 at the K show in Germany. It's the first time Battenfeld-Cincinnati has manufactured its own feed blocks for thermoforming sheet.
The feed block is manufactured in-house in Bad Oeynhausen, Germany, and is based on decades of experience designing and optimizing flow channels for pipe tooling for optimal melt and layer thickness distribution, according to the company.
One feed block can be used to produce both single- and multilayer sheet. The feed blocks can be used to make sheet and board from standard PP, PS and PET, as well as high-performance resins.
In most cases, the feed block is part of a complete extrusion line. It can be combined with high-speed extruders and standard and Multi-Touch roll stacks.
The feed block is placed before the die. It combines the melt streams from the different extruders, creating the layer structure. After the feed block, the melt enters the die, where it is stretched to the width of the sheet. Uniform distribution of the layers is critical for the quality of the end product, the company said.
The feed block is modular, which offers several advantages for the end user. Different types of materials can be processed, without any changes, just by turning the distribution bolt. The layer structure is flexible (A-B-A, A-B-C) and the number of layers can be increased by combining multiple feed block elements.
The feed block also can be used for foamed applications. The main advantage of these kind of sheets is a reduction in material usage, Stieglitz said. Due to the foam structure, the amount of virgin material can be reduced, which decreases costs dramatically.
To produce a foamed sheet, the melt has to be loaded with a gas. This can be done inside the extruder or externally in a separate unit.
Bruce Geiselman, senior staff reporter
Contact:
Battenfeld-Cincinnati USAMcPherson, Kan., 620-241-6843, www.battenfeld-cincinnati.com
Bruce Geiselman | Senior Staff Reporter
Senior Staff Reporter Bruce Geiselman covers extrusion, blow molding, additive manufacturing, automation and end markets including automotive and packaging. He also writes features, including In Other Words and Problem Solved, for Plastics Machinery & Manufacturing, Plastics Recycling and The Journal of Blow Molding. He has extensive experience in daily and magazine journalism.
Plastics Hall of Fame seeks nominees
Amcor, Berry Global will merge
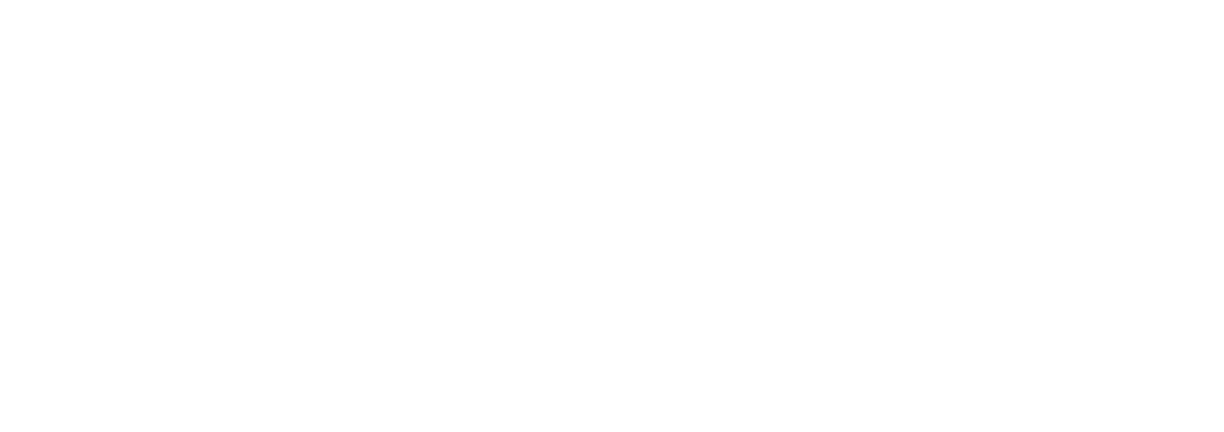