Milacron's DME division, in partnership with Linear AMS, is offering 3-D printed metal tooling components with conformal cooling channels, for use in injection molds.
DME's TruCool conformal cooling components reduce molding cycle times by improving thermal control of the mold, the company said. This can reduce scrap production and improve part quality. Employing conformal cooling provides increased flexibility in the design of a cooling line.
Conformal cooling channels follow the contours of a core or cavity insert and offer several benefits compared to conventional, straight, gun-drilled cooling channels. This includes the location of the conformal cooling channel, which can be positioned at an optimal distance from the surface of the mold.
The ability to exactly position the cooling channel allows the mold to maintain a targeted and consistent molding temperature, which can significantly reduce cooling times and reduce overall cycle times by up to 60 percent, depending on part complexity. The company also is offering components for conformal venting channels that can be used in hard-to-reach areas in a tool that could contain trapped gases.
Linear AMS has been involved with metal additive manufacturing since its founding in 2003. The company has more than 12 years of experience building 3-D printed cavity and core inserts with conformal cooling channels.
Under the partnership, DME TruCool conformal cooling inserts are 3-D printed using a direct-metal-laser-melting (DMLM) technology that results in cores, cavities and components that are extremely dense and strong compared to 3-D printed parts made via direct-metal-laser sintering (DMLS). According to DME, use of DMLM allows for lighter-weight components with improved performance characteristics to create complex shapes.
To make TruCool inserts, DME starts with a detailed review of the moldmaker's or molder's cooling requirements, using 3-D CAD modeling and finite-element-analysis software. Simulation software is used to determine the optimal cooling channel design and location in the mold.
DME TruCool components with conformal cooling are manufactured to a hardness up to 56 HRC. An additional 0.25 inch of rough metal is left on the part to allow the mold maker/molder to finish the surface of the part. Every tooling component made under the DME TruCool brand is material-, flow- and pressure-tested before shipment.
Mikell Knights, senior staff reporter
For more information:
DME Co.,Madison Heights, Mich., 248-398-6000, www.dme.net
Linear AMS,Livonia, Mich., 734-422-6060, www.linearams.com
Plastics Hall of Fame seeks nominees
Amcor, Berry Global will merge
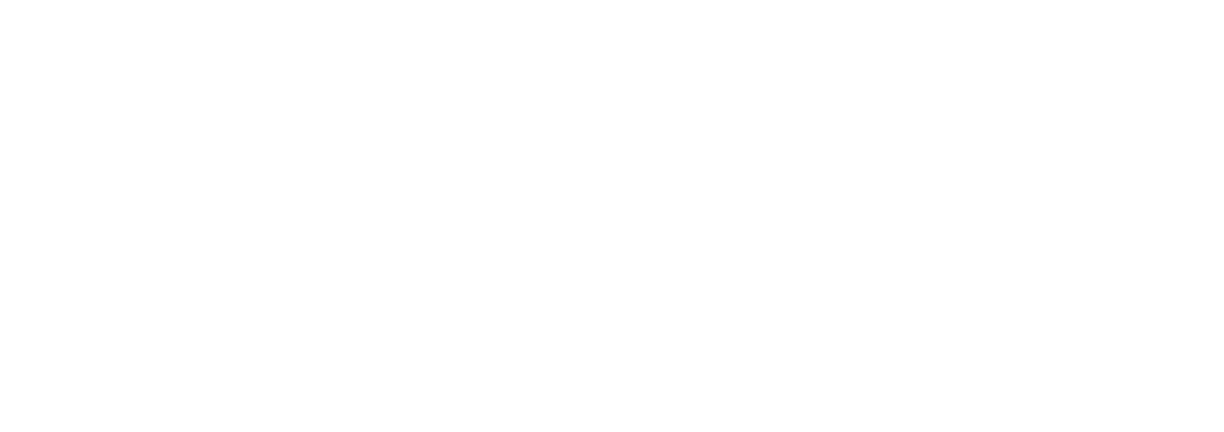