Wittmann Battenfeld Inc., Torrington, Conn., has a new addition to its Silmax Series of drying hoppers: a larger, completely modular hopper that can be converted into a PET crystallizer or expanded after installation.
The electric drying hopper, designed in the U.S., consists of up to four sections — a 500-liter base cone, a 1,500-liter body with a door, and one or two additional body sections that allow the capacity to be customized from 2,000 to 5,000 liters, or 176.5 cubic feet. That's enough capacity for up to 6,177 pounds of material, assuming a bulk density of 35 pounds per cubic foot. Introduced during the company's open house in October, the hopper can be used with both desiccant and hot-air-dryer applications. The insulated vessels easily can be converted into crystallizers by inserting an agitating unit into the assembly, said Nicholas Paradiso, engineering manager for material handling and auxiliaries. A crystallizer allows amorphous PET to be recrystalized so it can be processed again. This is typically used to reprocess PET regrind.
The modular design helps Wittmann Battenfeld keep costs down and allows the company to ship orders quickly because components can be kept in stock. The design also allows the hopper or crystallizer to ship in sections on standard pallets rather than as a fully assembled unit, Paradiso said.
The drying hoppers can fit in tight spaces because there are two locations in which the heating elements can be installed. The standard installation is on the rear of the drying hopper, but users can also install the heater unit at a 45-degree angle, which allows for placement of the heating elements within the leg footprint. Cables are located within the insulation layer, hidden from view, yet accessible if needed.
Wittmann Battenfeld is partnering with another company to design and build mezzanines to be installed along with the hopper/crystallizer, Paradiso said.
Bruce Geiselman, senior staff reporter
Contact:
Wittmann Battenfeld Inc., 860-496-9603, www.wittmann-group.com
Bruce Geiselman | Senior Staff Reporter
Senior Staff Reporter Bruce Geiselman covers extrusion, blow molding, additive manufacturing, automation and end markets including automotive and packaging. He also writes features, including In Other Words and Problem Solved, for Plastics Machinery & Manufacturing, Plastics Recycling and The Journal of Blow Molding. He has extensive experience in daily and magazine journalism.
Plastics Hall of Fame seeks nominees
Amcor, Berry Global will merge
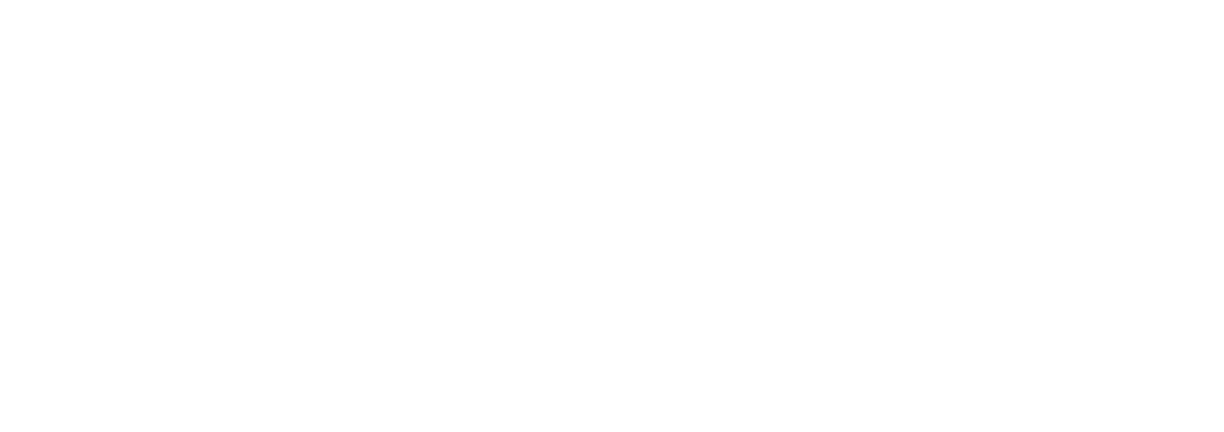