Plastics recycling is not a glamorous process, but it is becoming smarter, using electronic and online tools to improve machine performance and pellet quality.
Erema GmbH, Ansfelden, Austria, launched its version of the "smart" recycling factory at the K show, and is now moving to the next step — full vertical integration of the concept.
"This means that the process data of the complete recycling process — from sorting until the end product — is connected and entirely recorded," said Gerold Breuer, Erema's head of marketing and business development. "Erema is working together with its worldwide network and is in close cooperation with customers to take this next step."
The initial elements of the Erema approach include a manufacturing execution system (MES) called re360 that can connect two or dozens of recycling, film and other plastics production facilities anywhere in the world.
The system provides a single management dashboard of capacities and stoppage times, shows key quality data of the recycled resin, and signals upcoming maintenance jobs.
"Erema's [MES] is integrated in the individual security systems of the customer," Breuer said. "Erema has no insight in the customer's production data. If requested, the customer can give Erema the user rights exclusively for online technical support."
The company's QualityOn package consists of integrated machine sensors that record and evaluate melt volume-flow rate (MVR) and color. It can detect contaminants in the 0.004-inch to 0.04-inch size range, according to Erema. "The melt volume-flow rate is an important parameter for the quality of the pellets," Breuer said. "For example, in the HDPE-LDPE fraction, a polypropylene contamination is not uncommon. An increasing content of PP in this fraction influences the flow behavior and this can be detected with the MVR. Due to the continuous online measuring of the MVR in real time, the customer produces just pellets with the required MVR."
An online spectrophotometer is also used.
"An alarm is given if the color of the produced pellets is not within the tolerance range," Breuer said. "Recycled pellets with the wrong color (caused by the mix of input materials) are deflected out until production has become stable again; this means that a light production color is not contaminated with darker material."
QualityOn:MVR and QualityOn:Colour are just the beginning of Erema's quality tools for recycling, Breuer said. Further online measurement systems are under development.
STARLINGER & CO. GMBH
The recycling division of Starlinger & Co. GmbH, Vienna, implemented smart processes to allow customers to achieve compliance with food and drug regulations, such as FDA rules in the U.S.
"Our largest customer data-logs all machinery activity including run times, efficiencies, as well as maintenance intervals," said Alan DiUmberto, recycling sales manager for American Starlinger in Fountain Inn, S.C. "The machine control can also be accessed from any smart device, such as an iPhone or iPad."
Every 15 seconds, Starlinger recycling machines — which interface directly with enterprise software for tracking — take a snapshot of every operating component and log that data, DiUmberto said. The data can be stored internally and then accessed via thumb drive or the internet.
"You need to know when you are producing food-grade material and when you are not, so these data points have been tracked for years," DiUmberto said.
VECOPLAN AG
Vecoplan AG, Bad Marienberg, Germany, recently introduced its "Live-Service" to allow fast troubleshooting if recycling equipment malfunctions. Users can send questions to Vecoplan online "and receive immediate support from our expert service engineers, anywhere in the world," Vecoplan said in a November press release announcing the service.
Vecoplan maintenance engineers can remotely access the machine's controller or the control panel to identify and resolve problems in real time. Images can be transmitted via web cameras. Technicians can wear special goggles that allow them to see machine data while their hands are free to follow the remote expert's instructions.
Vecoplan also is supporting Industry 4.0. For example, users can monitor recycling equipment 24/7 with a Vecoplan app downloaded to a mobile device such as a phone.
NGR
Next Generation Recyclingmaschinen GmbH, Feldkirchen, Austria, is implementing a new technology called S.M.A.R.T. Dialog, which stands for self-monitoring, analysis and reporting technology. It's based on sensors embedded in recycling machines.
The goals include:
• To improve pellet quality;
• To use real-time data to reduce problems that could lead to equipment shutdowns;
• To improve maintenance efficiency through web-based spare-parts management; and
• To establish learning curves based on statistical process measurement.
Inline melt characterization is provided by a new technology from NGR sister company Dr. Collin GmbH, Ebersberg, Germany. The system provides continuous measurement of viscosity, color, polymer identification and E-modulus (tensile elasticity), the company said. The output is a customer-specific report on pellet quality. Dr. Collin, which makes specialty equipment for extrusion, was acquired by NGR in 2016.
NGR also connects recycling machines globally, and uses encryption codes to ensure security.
PALLMANN MASCHINENFABRIK
Pallmann Maschinenfabrik GmbH & Co. KG, Zweibrücken, Germany, uses an electronic evaluation system to set upper limits on bearing and operational vibration in its PMD 9-30 dryer, which is used to dry industrial plastic waste before it is reintroduced to the production cycle. A vibration monitor is installed at the housing of the machine. If the programmed value is exceeded, an alarm is triggered and the machine stops. Frequency converters control the rotor speed.
Doug Smock, senior correspondent
Contact:
American Starlinger-Sahm Inc.,864-297-1900, www.starlingersahm.comErema North America Inc., 978-356-3771, www.erema.net
Next Generation Recycling Machines Inc., 678-720-9861, www.ngr.at
Pallmann Industries Inc., 973-471-1450, www.pallmann.eu
Vecoplan LLC, 336-252-4462, www.vecoplanllc.com
Plastics Hall of Fame seeks nominees
Amcor, Berry Global will merge
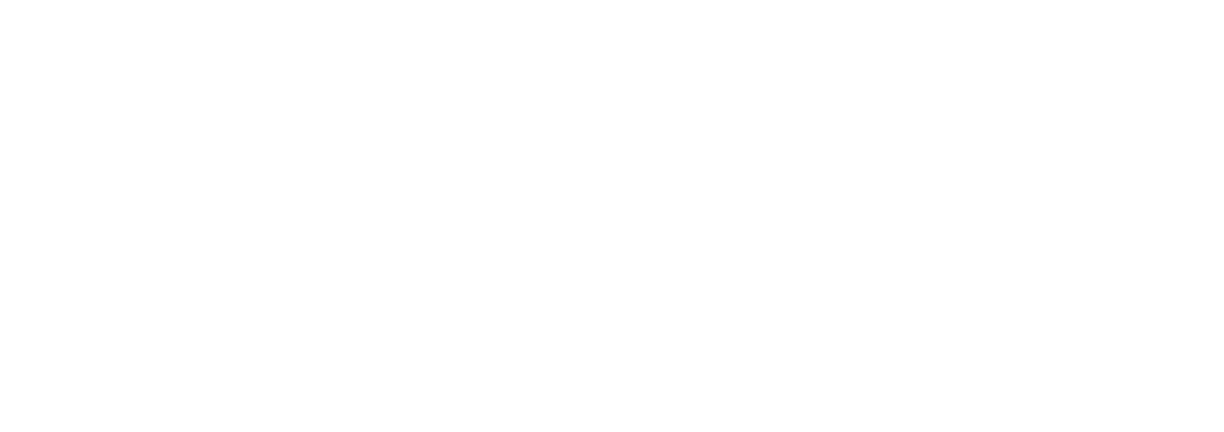