Special Report: What to consider when selecting best cooling system
Plastics processors face an important choice when determining how best to cool their equipment: use a central cooling system, or use portable chillers that serve specific machines or manufacturing cells.
The components used in each type of system are the same; central systems are just larger and have a greater cooling capacity, said Tim Miller, regional sales manager for heat-transfer products for Conair Group, Cranberry Township, Pa. Conair produces more than 450 different types of auxiliary equipment for plastics processing, including temperature-control equipment, resin-drying systems, blenders, feeders, material-conveying systems and granulators.
Miller said that factors to consider when choosing a cooling system include:
• the types of resins processed;
• how much capacity is needed;
• the performance capabilities of the system; and
• cost of installation and operation.
MATERIALS MATTER
Different materials are processed at different temperatures and give up heat at varying rates, so cooling HDPE, for instance, requires a larger chiller than PS.
A central system typically is designed to deliver water at just one temperature; a processor running materials that require widely different processing temperatures may not be able to realize the economies that a central chiller normally provides. If just one material runs 10 degrees Fahrenheit cooling than others, the central system must be sized to deliver that temperature. Therefore, the system will actually be oversized for the vast majority of the resins the processor uses. A key point is how much variation there is in temperature requirements, Miller said.
Typically, a cooling system needs 2 percent more capacity for every degree of cooling below the nominal rating of 50 degrees Fahrenheit. In other words, running just one material at 40 degrees Fahrenheit will require 20 percent more capacity. Under such circumstances, it may be more sensible to size the central system for all but the lowest temperatures and use portable chillers for those special materials. As a general rule, if 80 percent of your resins are processed within a temperature range of plus or minus 5 degrees Fahrenheit, you should consider a central chilling system, Miller said.
TAILOR COOLING CAPACITY TO NEEDS
Capacity requirements are another key criterion in selecting the type of cooling system. Plastics plants don't operate at 100 percent capacity all of the time. Manufacturers may have machines that are offline for maintenance or mold changes, and those machines that are running may be operating at a slower cycle time or with a mold or material that requires less than peak cooling.
However, while it is unlikely that all machines in a plastics plant will run at peak load all the time — thus requiring all of the cooling capacity — it is quite likely that some or all of the machinery will be operating at peak level at times. So, if portable chillers are used, they must be sized for peak load. On the other hand, if a central water system is chosen, it can be sized to match whatever total load may be reasonably expected — say 90 percent of theoretical peak load.
PERFORMANCE POSSIBILITIES
Performance is another critical consideration in choosing a central or machine-side cooling system. Since portable cooling units can easily be moved from machine to machine, a smaller chiller can be used any time a given machine is not operating at peak load. This could be a strategy if a processor has a sufficient number of portable chillers of various capacities to match changing loads around the plant.
However, even under the best circumstances, the chances of the portable chiller's capacity exactly matching the cooling requirements are virtually nil. It is likely that the chiller will be somewhat oversized. To maintain the proper temperature, portable chillers are usually designed to allow some refrigerant to bypass the condenser so that some heat is retained. The retained heat reduces the ability of the refrigeration circuit to absorb new heat, so this process in effect reduces the cooling capacity of the refrigeration circuit.
COSTS CONSIDERED
Expense is another factor to consider when deciding what type of chiller to purchase. Central chillers are more expensive initially because they are almost always bigger and have higher installation costs, but energy savings and lower maintenance costs usually make them a better long-term value, if they are properly sized.
With portables, chances are you will need to buy more capacity than you really need. For instance, if you have a production line with 10 machines and each machine requires 8 tons of cooling capacity, the line would require 10 10-ton chillers, while a central system would require one 80-ton chiller.
Generally speaking, a central system will require less operating tonnage, occupy less floor space and involve less equipment that needs to be maintained, Miller said. Most companies are likely to find that, on a cooling capacity basis, central systems are less expensive to buy and operate than their mobile counterparts. However, most plants need at least a few portable chillers for emergencies or to handle molds that run outside the temperature range of the central system.
There is no question that portable chillers offer many important benefits: their plumbing is less complicated and less costly; they allow the molder to accommodate a wide range of processing temperatures; and they are "safer" than a central system, in that failure of one unit will not shut down an entire plant.
OTHER FACTORS TO CONTEMPLATE
Other factors to consider include noise and maintenance. Air-cooled chillers, whether portable or central, tend to be noisy. Air-cooled portables also introduce hot air into the plant, which can be a benefit in the winter but a problem in the summer. Air-cooled central chillers are almost always located outside.
When choosing a portable chiller, beware of the potential for higher maintenance and operating costs. It is always best to work closely with an experienced system supplier who can interpret your objectives and design a system that meets your current needs and allows for future growth.
Mikell Knights, senior correspondent
Contact:
Conair Group,
724-584-5500,
Plastics Hall of Fame seeks nominees
Amcor, Berry Global will merge
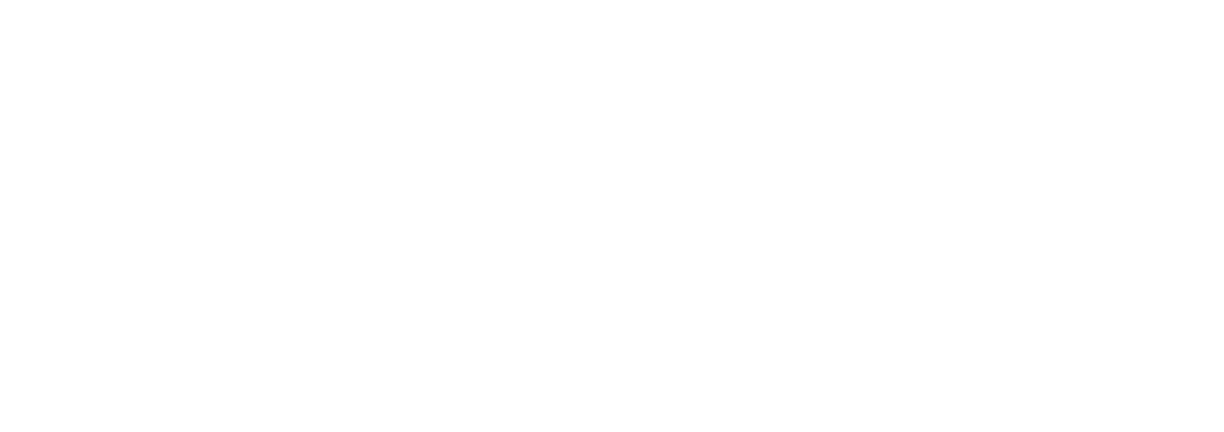