Welding is the lifeblood of any tool and die shop, and several welding options are available for performing mold repairs. While each technique has its pros and cons, advances in laser welding technology are providing significant advantages for mold repair, resulting in faster turnaround and less reworking. The new technologies also require less maintenance.
Laser welding is not new to mold repair shops where Nd:YAG (neodymium-doped yttrium aluminum garnet) laser-welding systems have already shown advantages over traditional TIG (tungsten inert gas) and micro-TIG arc welding. What is new are fiber-laser-welding machines, which offer the same advantages as YAG welding machines over traditional arc welding, and avoid some of the drawbacks of the better-established YAG laser-welding systems.
That has given fiber-laser-welding machines a foothold in mold repair. At the Amerimold trade show in Novi, Mich., in June, two exhibitors — Phoenix Laser Solutions, Meadville, Pa., and Alliance Laser Sales Inc., Wauconda, Ill. — exhibited their latest fiber-laser-welding machines. The companies shared their views on the advantages of laser welding generally, and what fiber-laser-welding machines in particular bring to the table.
NEW MACHINES HIT THE MARKET
At Amerimold, Phoenix Laser Solutions, a mold repair company and distributor for Alpha Laser GmbH, Puchheim, Germany, demonstrated the ALFlak 900 F fiber-laser welder, which, at 900 watts, is the most powerful system Alpha Laser offers.
Blair Learn, an owner of Phoenix Laser Solutions, described the ALFLak laser welder as an open laser system, because it doesn't have a cabinet around it. This allows more flexibility to direct the beam to the welding surface, he said. The higher wattage gives it the ability to weld faster, but still maintain low-heat input to the work piece. The ALFlak 900 F does not have a chiller, making it more mobile. It can be moved where it's needed, such as a milling station or even an injection press to perform a repair without removing the mold.
The ALFlak mobile fiber-laser machines are available with wattages between 300 and 900 watts; the 900-watt unit is new to the U.S. The ALFLak machines come in two versions: One model can be moved manually, while the other has a self-propelled catepillar track. The cost of the 900-watt ALFLak unit with tracks is about $220,000.
Alliance Laser Sales, a manufacturer of fiber-laser-welding machines and the U.S. representative of Vision Lasertechnik GmbH, Barsinghausen, Germany, is offering two new fiber-laser systems. At Amerimold, the company showed for the first time its ID1 fiber laser welder, a 300-watt fiber-laser-welding machine. Ryan Stapleton, technical manager at Alliance Laser Sales, described the ID1 as a flexible machine with a very stable platform. It is equipped with a heavy-duty base, and the welding mechanism hangs from an overhead gantry. "We made it as versatile as we could make it," he said.
The ID1's spot size is manually adjusted right at the head, which Stapleton said eliminates the chance of electrical and computer failures and allows the operator to make instantaneous adjustments.
Also new from Alliance Laser Sales is a fiber-laser welder manufactured by Vision Lasertechnik. The Ultra Flexx is a mobile, 300-watt fiber-laser welder that was previously available as a YAG laser welder. It has a 10-foot reach without the need for a crane, so it is able to repair molds while they are in the press, although it is somewhat less stable than the ID1 because of its long arm extension, according to Stapleton. He said the Ultra Flexx is well-suited for accessing hard-to-reach areas.
Both the ID1 and the Ultra Flexx are user-friendly, with touch-screen controls. The ID1 costs about $100,000 and the Ultra Flexx about $150,000.
LASER DELIVERS BETTER HEAT CONTROL, STRONGER WELDS
According to Learn, laser welding is a major step forward compared to conventional TIG welding. He said the main advantage of laser welding, whether using a YAG or fiber laser, is that it heats the work piece less than TIG welding. This results in less heat distortion, zero shrinkage and a much smaller heat-affected zone (HAZ), the portion of the base material that is altered, but not melted, by the welding process. "Heat is not your friend" in any welding process, he said. "By controlling the heat, [laser-welding systems] can minimize distortions in the HAZ, giving the toolmaker much more control."
Minimizing the amount of heat that is put into a work piece reduces the amount of rework required to fix distortions that might occur in the area around the weld, which happens often with TIG welding. "[Laser] is not changing the metallurgy nearly as much as you would by conventional welding," he said. "The heat-affected zone with conventional welding is very deep and changes the hardness drastically. Heat drives grain growth, which softens it, changing the Rockwell hardness by many points, whereas laser changes it by only a few points."
To demonstrate that, Phoenix ran an experiment in its lab comparing laser and TIG weld deposits on identical samples of H13 tool steel hardened to 50 Rockwell C. Both processes resulted in good fusion and zero visible defects, but the HAZ with the laser-welding sample was superior compared to the TIG sample. Laser welding resulted in a smaller HAZ (0.008 inch vs. 0.095 inch for TIG), with no significant softening in the HAZ (47 Rockwell C for laser vs. 31 for TIG). The laser weld also provided slightly improved hardness at the surface of the laser weld, which is important in areas that experience a lot of wear.
Both YAG and fiber-laser welding are pulsed-welding processes, which deliver far less heat into the part compared to conventional arc welding. Laser welding reduces pitting, distortion and shrinkage in the weld and potentially eliminates the need for time-consuming heat treatment that is required before and after conventional welding. In addition, laser welding is a highly accurate line-of-sight process, where the laser beam can be aimed to weld hard-to-reach areas of the mold.
The upshot is that laser welding — whether YAG or fiber laser — can mean faster turnaround for tasks such as repairing damaged gates or worn parting lines, yielding a new surface that will last virtually as long as the original surface.
FEWER PARTS TO WEAR OUT
While YAG and fiber-laser-welding machines deliver similar advantages in the welding process, they differ from each other when it comes to their internal components and how they generate the laser. Those differences have significant implications for maintenance and cooling requirements of the welding machines. Fiber-laser-welding machines use an LED to create the laser and optical fibers to direct the laser to the work piece. YAG welding machines use a lamp and a crystal to generate the laser.
Alliance Laser Sales' Stapleton said fiber-laser welders have fewer parts that can wear out. The YAG laser necessitates a lamp that occasionally needs to be replaced. "Depending on how aggressively you use it, at least once a year you have to replace the lamp," he said. The heat generated by the lamp also necessitates a water chiller.
Furthermore, as the lamp deteriorates with use, the power parameters — voltage, amperage or pulse width — must increase to compensate for the lamp's loss of energy to maintain power consistency.
Overall, the lamp, crystal and mirrors on each end of the resonating chamber on the YAG laser machine are all subject to wear. "There are a lot more optics and consumable parts on the YAG laser compared to the fiber laser; fiber lasers are air-cooled, and there is no lamp and no water-chilling system," he said. "You reduce the amount of optics by half."
According to Stapleton, fiber-laser welders are truly solid-state and robust. Fiber-laser welders are better than YAG welders at maintaining a consistent beam quality over its entire power output range, and can run at higher frequencies.
John DeGaspari, senior correspondent
Contact:
Alliance Laser Sales Inc., 847-487-1945, www.alliancelasersales.com
Phoenix Laser Solutions, 814-724-3666, www.phoenixlaser.com
Plastics Hall of Fame seeks nominees
Amcor, Berry Global will merge
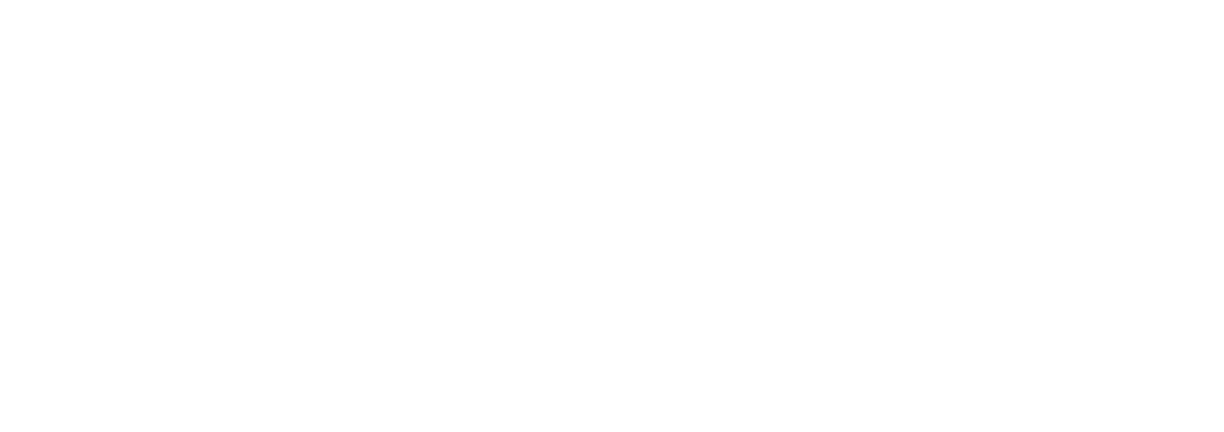