Special Report: Suppliers offer methods to identify potential trouble in production lines
Picture this: You're driving when you hear a funny sound coming from the engine. You say to your passenger, "We just got the oil changed. Don't worry about it." Minutes later, you're calling for a tow truck.
This is an unplanned downtime nightmare, and similar circumstances can be the scourge of any manufacturing plant. Doing preventive maintenance may not be enough. Fortunately, a number of predictive maintenance tools and techniques can diagnose problems before equipment fails, without any scheduled downtime. They can also identify signs of wear or potential failure that may not be covered by routine preventive maintenance. Here are three approaches plastics processors can take to prevent unexpected machine failure.
MACHINE-WEARABLE SENSORSON THE SHOP FLOOR
Last year at NPE, auxiliary equipment maker Novatec Inc., Baltimore, unveiled machine-wearable sensors for the early detection of operation anomalies that can lead to equipment failure. Novatec plans to make the technology standard on its products this month, and will make a retrofit package available by late summer for use with its older equipment as well as competitors' products.Novatec President Conrad Bessemer noted that it has made a "strategic investment" in Prophecy Sensorlytics, Columbia, Md., essentially giving Novatec a lock on the technology. The wearable sensors are marketed under the name Prophecy.
As of late March, Prophecy was undergoing beta testing with key Novatec customers. The sensors have been used on vacuum pumps, blowers, dryers and gearboxes.
The technology is a major advancement for the plastics industry, said Bessemer. Its advantages include affordability and ease of use. Bessemer noted that no special training is required to implement the technology, or to interpret the data coming from 24/7 monitoring of critical machine components.
Bessemer said that the technology will make predictive maintenance affordable for plastics manufacturing plants. He calls his system "prescriptive" maintenance, since it's based on machine usage rather than a maintenance schedule. He said it will eventually take the place of preventive maintenance programs.
The technology is fairly straightforward. Sensors mounted on machine components detect operating conditions and transmit the data via Wi-Fi to a data hub in the plant. The information is transmitted to cloud-based servers that use software to evaluate conditions. The data is fed back to maintenance personnel in a form that is easy to understand.
Prophecy Sensorlytics has designed sensors to monitor variables that include vibration, temperature, magnetic field, power factor and power quality. The sensors collect data at 10- to 20-second intervals. Bessemer noted that the security risk is very low: The sensors do not transmit process data, but are limited to monitoring raw machine data that would be meaningless to anyone outside the plant.
The sensors monitor two basic kinds of data: machine component performance, so that the risk of failure can be detected before it occurs, and power factor/power quality. For example, a vibration sensor on a vacuum pump can detect overfilling of oil, which increases pressure on diaphragms and bearings that can reduce their service life. Or sensors can measure if enough power is being delivered to critical machinery, Bessemer said.
Bessemer has long been interested in the idea of applying real-time sensing capability to machinery. "I think that getting the industry to a higher level of prescriptive maintenance is a good thing. A lot of the problems in our industry are more human error than they are machine error; people [often] run things to failure."
ADAPTING REAL-TIMEPROCESS MONITORING
Ed Potoczak, industry manager of IQMS, Paso Robles, Calif., said the company provides predictive maintenance tools to its customers by integrating its RealTime production monitoring system with the PLCs and sensors on the production equipment or in the manufacturing cell. He said IQMS integrates the system by accessing the data registers in the existing PLCs supplied by the OEM; it can also install its own PLCs. Similarly, the monitoring system pulls data from sensors original to the equipment, and can also link to sensors that have been added by the customer.
Potoczak said the system collects operating parameters from the processing equipment into its database. The collected information can be linked to a statistical process control module to track the quality of the process and the manufactured parts.
IQMS works closely with customers to determine what factors need to be monitored, such as temperature, pressure or voltage, and to view trends. He said that integrating sensors that collect process data with the IQMS RealTime monitoring system can reduce the frequency of preventive maintenance procedures in certain areas of the manufacturing line, and help identify potential problem areas well ahead of catastrophic failure.
RELYING ON HIGHLY TRAINED EXPERTS
Andrew Rodes is director of business development for Semeq Inc., Arlington, Texas, which provides predictive maintenance services. His company relies on a team of data takers who visit plants on a regular basis to monitor equipment. That data is transmitted to a central laboratory, where experts interpret it for potential red flags.
Rodes said that a predictive maintenance service using trained experts is a cost-effective way to avoid problems. He said it makes economic sense for small to mid-sized plants that don't have the workforce to perform predictive maintenance in house. Semeq also provides predictive maintenance services for large manufacturing companies, including a plastics processor that performs extrusion and compounding in about 60 plants worldwide.
Rodes said four areas of analysis are important for detecting potential problems that are not necessarily covered by preventive maintenance programs:
• Vibration analysis of rotating equipment detects premature faults, pits and cracks in bearings, rotors, stators, gears and pinions. Vibration analysis can detect microscopic defects months before failure, as well as dynamic issues such as alignment and balance problems. In a new service announced by Semeq a few weeks ago, data collected can now be streamed in real time to analysts in a Semeq lab.
• Acoustic emission testing is valuable in multiple applications. It detects acoustic signals at a very high frequency. In addition, acoustic emission testing can detect air leaks in compressors. Rodes said finding — and fixing — such leaks can save a plant tens of thousands of dollars in energy costs.
• Thermography can locate hot spots in electrical cabinets that indicate worn components or malfunctioning electrical circuits that can lead to breakdowns. It is an alternative to the standard preventive maintenance process of checking and tightening electrical contacts manually.
• Oil analysis determines if the oil has the right viscosity, or if the oil or additives are breaking down.
According to Rodes, the results from the techniques should be integrated to provide a comprehensive view of the maintenance that needs to be performed. He said experts recommend that predictive maintenance should account for 80 to 90 percent of a maintenance department's work orders.
FORECASTING FAILURE
To prevent unexpected machine failure, Senseye predicts it. The Southampton, England, company in January introduced a software system, Prognosys, to automatically forecast failure in extrusion, injection molding and compression machinery.
Senseye's cloud-based software can accept input from any sensor or database to monitor machines to provide forecasts for failures as much as months in advance, based on machine conditions, the company said.
Benefits of the Prognosys software include its ease of use and access. According to the company, Prognosys does not require complex setup, and users don't have to perform sophisticated data analysis to use it. Instead, it's targeted for use by plant managers, who can access the information via smartphone, tablet or PC.
John DeGaspari, senior correspondent
Contact:
IQMS, 805-227-1122, www.iqms.com
Novatec Inc., 410-789-4811, www.novatec.com
Prophecy Sensorlytics, 877-460-1920, www.prophecysensorlytics.com
Semeq, 877-480-9530, www.semeq.net
Senseye, 415-523-0447, www.senseye.io
Plastics Hall of Fame seeks nominees
Amcor, Berry Global will merge
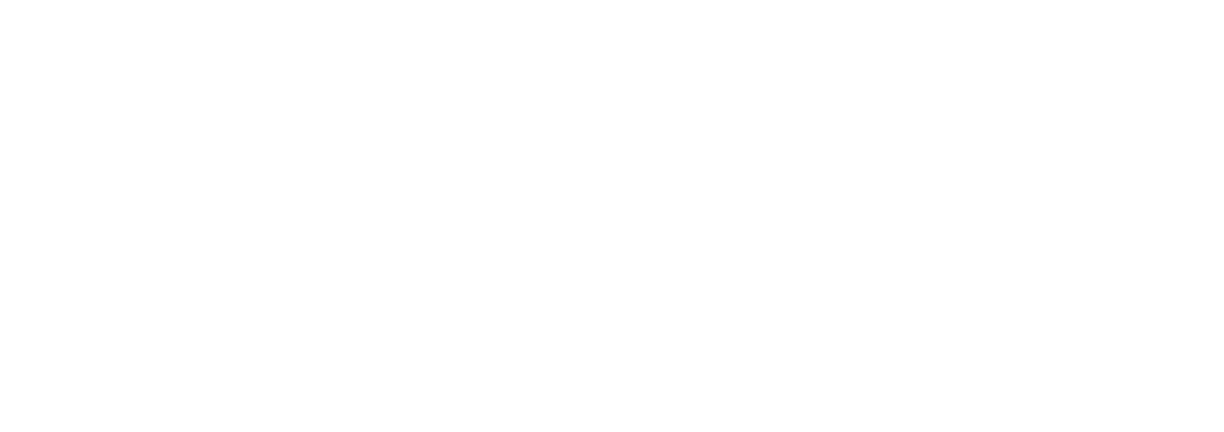