Matching the pelletizer to the system — and the application — is key for processors hoping to make the most of their equipment. Several companies are introducing new systems or upgrades, while others have worked with their customers to help them better integrate pelletizers into their processes.
BAY PLASTICSCOMBATS CARRYOVER
Bay Plastics Machinery, Bay City, Mich., is testing new equipment. Using a vacuum process, it has created a way to combat carryover — the situation in which cut pellets follow the rotor back around in the cutting process and are recut, creating fines and lowering quality. The new process removes pellets from the cutting chamber. This increases the pelletizing yield and reduces the time that must be spent classifying right-sized pellets from ones that are too small. "There are some good applications for this new technology, and this has the potential to significantly increase material yields for companies struggling with carryover and fines," said Dick Fetter, VP of technical development.
James Forgash, VP of sales, said the company plans to incorporate the technology in a new application-specific Micro-Pelletizer, which will be able to control strands nearly as fine as a human hair. To make this possible, the unit will feature more than a 40 percent reduction in the distance between the feed roll nip point to the bed knife and cutter, as compared to standard pelletizers. It incorporates a patented rotor technology offering a greater number of cuts while reducing turbulence in the cutting chamber.
Bay Plastics' carryover-prevention process is undergoing beta testing and will be available for production use soon, the company said.
LEISTRITZ UPGRADES LHLG SERIES
Last month, Leistritz Extrusion, Somerville, N.J., announced it has upgraded its LHLG air-quench pelletizer series to make the machines better able to handle water-soluble, foamed or filled applications. A company spokesperson said the pelletizers have been upgraded with a self-aligning, concentric-cutting-head design. In addition, all contact parts are now made from stainless steel. Standard features include an electrically heated die, manually adjustable blades and a height-adjustable support cart on tracks. A blower facilitates initial cooling and transport to a secondary cooling and transport mechanism.
To handle sticky formulations, Leistritz now offers optional misting attachments for the LHLG pelletizers. "The misting options expand the range of cuttable materials," the spokesperson said. Leistritz says the pelletizers have applications in the medical, pharmaceutical and specialty plastics industries.
FILTEC TAILORS OPTIONS
Filtec, Badia Polesine, Italy, has also redesigned some of its offerings. Filtec's GRO pelletizers have been upgraded in multiple ways, the company and its U.S. supplier, ADG Solutions, Fairfield, Conn., said. The new pelletizers have a new, one-structure architecture that fully integrates the three-stage drying system with the horizontal cutting heads and closed-loop water-cooling system, which is designed to prevent contamination of the water used to cool the pellets. In addition, Filtec has recently upgraded its GRO pelletizers with devices for automatically adjusting the systems' blades, giving users even greater control and reducing the wear on blades and die plates.
A Filtec spokesperson said the "pelletizers represent the perfect balance between quality and economy." With models appropriate for a range of resins, including LDPE, PP, PC, ABS and PVC, the series is an appropriate choice for users seeking pelletizers that are compact and easy to use. The company said the GRO units are energy efficient and offer optimized melt flow and low operating pressure.
In addition to the GRO pelletizers, Filtec also makes fully automatic underwater pelletizers that have been built for polymers with high melt flow indices and can handle easily flowing products. The UW pelletizers feature closed-circuit water circulation die plates heated either electrically or by diathermic oil, and produce homogenous, spherical pellets, with few agglomerates.
Filtec, which has agents around the world, continues to grow. The company has its sights on further growth in North America — with plans in the works for spare parts warehouses "and operators able to meet the needs of a market of great potential and even greater expectations," the spokesperson said.
NORDSON SUPPLIES MASSIVE CHINESE PLANT
Nordson Corp., Westlake, Ohio, is intensifying its focus on pelletizing systems for Asia with a recent commitment to
Jiangyin Chengold Packaging Materials Co. Ltd., Jiangsu Province, China. In January, the company announced that it is supplying the PET compounding plant with 16 BKG-brand CrystallCut underwater pelletizing systems.
Ralf Simon, Nordson BKG managing director, said Nordson anticipates that the Chinese company, which is slated for startup this year, will realize huge energy savings with the CrystallCut systems, compared to conventional PET polymerization. Designed to produce free-flowing crystallized PET and polylactic acid pellets, the systems use the thermal energy of the molten polymer to combine pelletizing, crystallizing, drying and water filtering at temperatures of up to 356 degrees Fahrenheit. By contrast, conventional methods require a significant amount of energy for cooling and reheating of pellets and yield only amorphous material, said Adam Cowart, business development manager for the BKG brand. With the system, users can achieve up to 40 percent crystallinity.
In the new plant, the CrystallCut systems will deliver PET pellets to EcoSphere solid-state polycondensation systems built by Polymetrix AG, Oberbüren, Switzerland.
ENTEK-GALA INTEGRATION
For an Entek/Gala customer, making machine systems work better together was an important goal. Entek's John Effmann said that integrating a pelletizer into a line is largely a matter of meshing controls. Effmann spoke to Plastics Machinery Magazine shortly before retiring as director of sales and marketing for Entek, Lebanon, Ore., at the end of last month. Effmann said the company recently had a customer that sought to integrate controls for a pelletizer from Gala Industries Inc., Eagle Rock, Va., with Entek's Smart controls for a co-rotating, twin-screw extruder. The Smart controls feature enhanced graphics, a recipe library and web-based connectivity for remote troubleshooting. Entek mimicked the Gala control screens to give processors one location from which to control their equipment. By bringing the controls together, users can operate a range of auxiliary equipment from one HMI.
"It is in one spot," Effmann said. "The HMI on the machine can control almost all the functionality on the pelletizer, and people like that because they don't have to run around, and go from one screen to the other, and so forth."
The interest in integration is nothing new, but demand for ever-increasing levels of sophistication continues to grow, Effmann said. In the case of the Entek/Gala integration, operators have access to five or six levels of screens — all dealing with pelletizing. That makes the process more precise, as well as more efficient. The integrated controls offer a variety of information and functions, including histories, a formulation/run program, a configuration screen, history/trending, password protection and alarms. All data can be stored and subsequently evaluated.
COPERION'S CONVEYOR MAKESPELLETIZING EASIER
Users of equipment from Coperion Pelletizing Technology GmbH, Offenbach, Germany, also have the option of integrating controls; the company's extruder and strand conveyance controls are compatible. Last year, the company developed an automatic strand conveyance system (ASC) for use with compounding systems performing pelletizing at very high throughput rates.
Compared to other processes, Coperion said strand pelletizing's lower pressures ensure gentle treatment of the product. Other advantages are the reduced complexity of the system and the low rate of wear. Combined with the relatively low operating costs of the process, these benefits make strand pelletizing a good choice for the compounder, according to Coperion.
The ASC is designed to work in conjunction with Coperion's two large strand pelletizers, the SP 500 HD and the SP 700 HD. It is available in two sizes, with throughputs ranging from up to 3.5 tons per hour to up to 5 tons per hour. They have working widths of 500mm and 700mm, respectively.
The conveyance system automatically guides the extruded strands via a cooling water chute and downstream conveyor belt into the feed mechanism of the pelletizer. An automatic mechanism facilitates the start-up operation. The system rethreads strands, preventing any possible machine malfunctions that could be caused by broken strands. The system, which can be used for a broad spectrum of materials, is vertically adjustable, permitting different points of strand placement on the water chute, depending on the material being processed. An integrated strand monitoring device helps to maintain high takeoff speeds in conjunction with a high number of strands and hence high throughput rates in fully automatic operation.
Merle R. Snyder, senior correspondent
Contact:
ADG Solutions,
203-255-9444, www.adgs.net
Bay Plastics Machinery,
989-671-9630, www.bayplasticsmachinery.com
Coperion K-Tron Pitman Inc.,
856-589-0500, www.coperion.com
Gala Industries Inc.,
540-884-2589, www.gala-industries.com
Entek,
541-259-1068, www.entek.com
Leistritz Extrusion,
908-685-2333, www.leistritzcorp.com
Nordson Corp.,
800-816-7711, www.nordsonpolymerprocessing.com
Plastics Hall of Fame seeks nominees
Amcor, Berry Global will merge
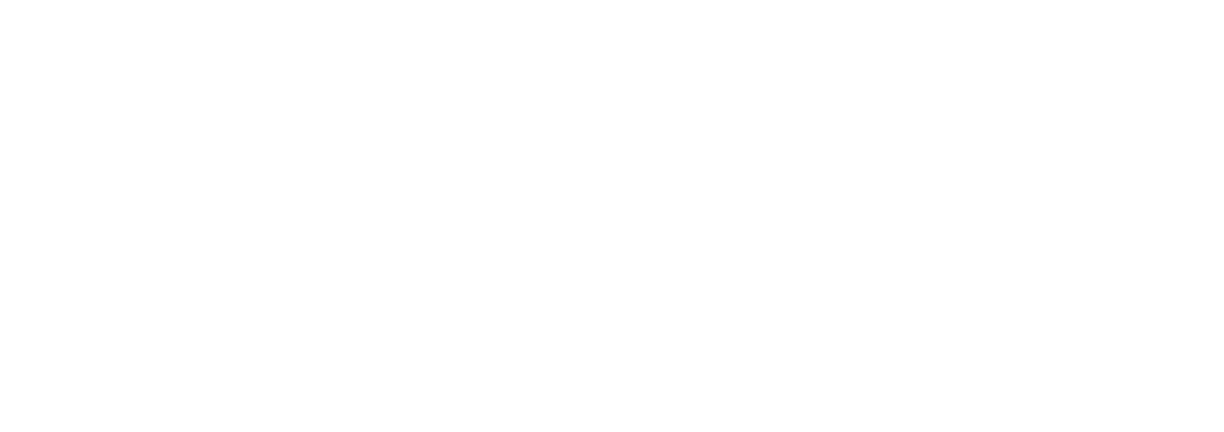