Special Report: Customers drive suppliers to integrate clean rooms
Process integration is on the rise across many industries, but particularly in clean-room applications.
"The level of automation is rising, and automation is becoming an increasingly integrative process component, which enables higher product quality, greater process reliability and completely new products and options," says Christoph Lhota, VP of Engel Austria GmbH, Schwertberg. By reducing or eliminating human contact, automation significantly increases hygiene.
Lhota cites the production of intravenous drip chambers as an example, explaining that the most current approach is a three-stage process requiring two to three injection molding machines, an assembly unit and a bonding station. This doesn't include the logistics for handling, transportation and storage. Engel streamlined the process with its system partner, Hack Formenbau GmbH, Kirchheim unter Teck, Germany. They integrated the injection molding steps into a single production cell. Now, in one working step, the two-chamber parts are manufactured, fitted and overmolded.
MAINTAINING CONSISTENCYAND VALIDATION
Integration offers advantages for clean-room operations. These advantages make the work cell smaller and reduce the risk of contamination, since no intermediate products have to be stored and transported. "Thanks to the highly integrated and automated method, a significant amount of time and money can be saved in the production of multicomponent hollow bodies with inlays," Lhota says.
With the need to maintain consistency among the vast array of machines and auxiliary equipment, establishing compatibility among various pieces of equipment and production steps is also beneficial in maintaining clean-room validation. "It takes weeks to validate the process," said Dale Bartholomew, product manager for machinery distributor Maruka USA Inc. in Lee's Summit, Mo. "And once you validate the machine and the process, it has to stay that way." Thus, the integration with related data communication is essential. In fact, Bartholomew says, "In medical molding, that's more critical than anything — that validation process."
Additionally, he says, "We work hand in hand with all major robotic manufacturers; that's another part of that integration. There are a lot of those projects going on right now."
Claude Bernard, marketing manager with Sepro Group, La Roche sur Yon, France, says the rise of automation within clean rooms parallels its growth elsewhere in the industry.
"Robots are definitely being used with increasing frequency in clean rooms, but mostly for the same reasons they are becoming more common across the industry: to improve efficiency and stabilize the process," Bernard says. In the medical industry, as in most other industries, plastic parts are becoming progressively more technical in design and application, and that increases the need for automation. "In medical molding and other controlled-environment applications, however, there is the added challenge that variability in process conditions cannot be tolerated. And human operators are the most common source of variability and also contamination," he says. "By making a human operator unnecessary, a robot eliminates most of the problems that humans can cause.
"Probably the biggest contribution robots can make to clean-room molding is in controlled part handling," he says. High-volume production usually requires multicavity tooling and in most commodity applications, parts molded in different cavities can be allowed to mingle on conveyors or in bins or boxes. In medical molding, however, every part must be traceable and data about how it was produced must be stored. That, in turn, means that parts must be removed from the mold and handled individually so they can be traced back to the cavity in which they were produced. "Even the best human operator cannot be trusted to be 100 percent accurate and consistent hour after hour and day after day. A robot can be trusted," Bernard says.
Another factor driving the increased use of robots in clean rooms is the fact that a growing number of medical devices, pharmaceutical packaging and drug delivery systems are made of plastics, Bernard says. That demand for the parts — and the labor to produce them — has contributed to growth in robotics. "This means that molders need to be more productive and more flexible, and robots help in that regard as well."
ONE POINT OF CALL
The growing demand for integration and automation contributed to a partnership of Toshiba Machine Co. America and TM Robotics, providing customers with a one-stop shop for robotics. Their union is, perhaps, the ultimate in integration, with the offices of the two housed together in Elk Grove Village, Ill., as a cohesive unit. Toshiba engineers and produces in-house the injection molding machines and robotics. TM Robotics is responsible for the sales, marketing and support for the SCARA, Cartesian and six-axis industrial robots. "The same people design the systems, so the compatibility is seamless. It's not an injection molding machine and robotics, it's a production cell," says Ryan Guthrie, executive VP with TM Robotics.
"More and more, the customer base wants to have a business solutions provider. They want to have a partner," adds Michael Werner, senior technical manager with Toshiba. Customers want to be able to complete the project, accomplish their objectives and maintain the clean room without having to track down multiple suppliers.
Toshiba and TM Robotics often come across clean cells where the equipment has been supplied by multiple players. In such cases, when one system goes down, the customer can end up spending half a day trying to figure out which piece it is, Guthrie says. TM Robotics is a wholly independent company, but he says, "Our sole responsibility is to be the face of Toshiba and sell robotics outside Asia."
Jason Holbrook, sales manager with KrausMaffei Corp., Florence, Ky., comments similarly. "Customers used to buy molding machines, robots, etc., from different suppliers. But within the last five to 10 years, customers realized they don't have the knowledge, time or technical ability to do all this, so they required their suppliers to provide it." Because of this, he says, the entire system has shrunk and become consolidated into one completely integrated system.
With such integration comes equipment intelligence through integrated software, so if anything goes wrong with any component of the system, the molding machine identifies and rejects the parts; then if a specified number of parts is rejected, it stops the line and sets off an alarm.
Toshiba machines are all-electric, so they fit clean-room requirements because there is no hydraulic fluid, Guthrie says. Additionally, the machines have a reduced use of cooling fans, so particulates are not blown around the room. The Toshiba standard for its machines is Class 8 or better, he says, so they are clean-room-ready right out of the box. "If [customers] have more specifications, we do have other options," he said, such as stainless-steel guarding, nickel plating and HEPA filters.
WORKING TO CUSTOMERSPECIFICATIONS
It is the equipment customer, and the customer's customer, who provide specifications for a clean-room environment, including the cleanliness rating needed for a particular product.
That is exactly the case with contract manufacturer Bright Plastics Inc., Greensboro, N.C., which assembles medical products, such as pharmaceutical vial vent filters and oxy-packs for premature infants, within a clean-room environment. "Our clean room is ISO 8," says Joe Vest, VP of engineering. "We could certify it higher, but our customers don't require that."
In fact, he says, because Bright Plastics doesn't need the extra specifications of machinery manufactured for higher classes of clean rooms, the company skips the extra cost of those, simply using all-electric equipment.
"The biggest change we've made is putting sprue pickers on all the machines in the clean room," Vest says, so what used to take three people operating three machines now takes only one. The automation has helped the company reduce labor, Tichy says. "Less labor in the room means less coming in and out."
Considerations about every piece of machinery in the clean room — and how it all fits together — are driving innovation, manufacturers, such as KraussMaffei's Holbrook, say.
"The clean room is no longer stand-alone," says Holbrook. "The greatest innovation we see is the integration of the systems and minimization of the footprint. And with integration, you get tighter control, tighter reporting and better parts for less money."
Lisa Jo Lupo, correspondent
Contact:
Bright Plastics Inc., 336-668-3636, www.brightplastics.com
Engel Machinery Inc., 717-764-6818, www.engelglobal.com
KraussMaffei Corp., 859-283-0200, www.kraussmaffeigroup.us/en/
Maruka USA Inc., 816-524-1811, www.marukausa.com
Sepro America, 412-459-0450, www.sepro-america.com
TM Robotics (Americas) Inc., 847-709-7308, http://tmrobotics.com
Toshiba Machine Co. America, 847-709-7000, www.toshiba-machine.com
Plastics Hall of Fame seeks nominees
Amcor, Berry Global will merge
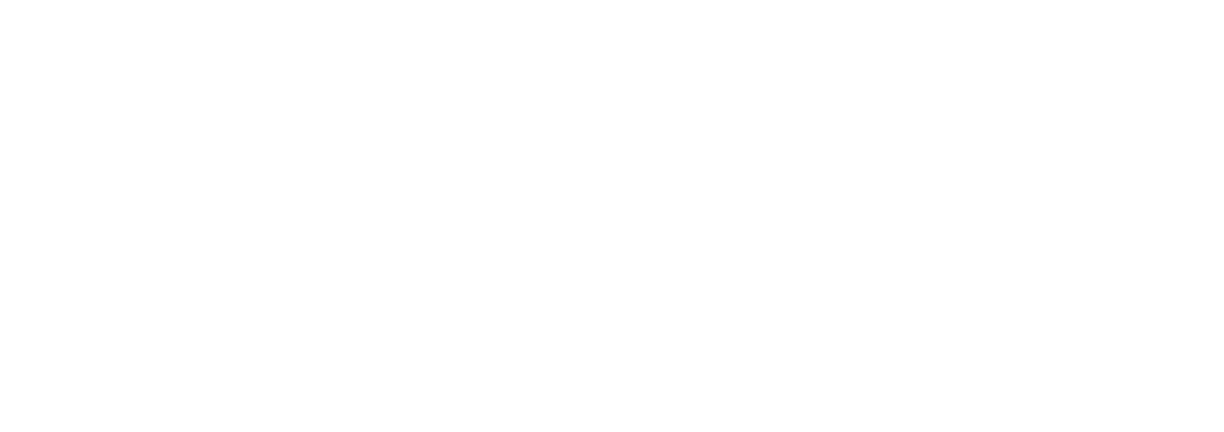