The Wittmann Battenfeld Group, Vienna, displayed new injection molding machines at Fakuma in its SmartPower, EcoPower and MicroPower series.
The new SmartPower 350/2250 completes the line, which the company launched with a 120-ton model at Fakuma 2014. The line's sizes range from 25 to 350 tons.
The energy-efficient machines use a standard servo-hydraulic drive, and deceleration energy is reclaimed by a kinetic energy recovery system and used for barrel heating and other functions. Wittmann Battenfeld estimates overall power consumption has been reduced by up to 35 percent.
The distance between the tie bars is about 31 inches by about 28 inches, and the machine has a compact overall footprint. The machine uses a hydraulic clamping system with diagonal fast-stroke cylinders and a centrally mounted ejector. Injection units are mounted on linear guides and can be swiveled for servicing.
Three screw sizes, all with a 22-to-1 L:D ratio, are available.
As part of another Wittmann Battenfeld line, a new all-electric EcoPower 110/350 machine equipped for clean-room applications was on display for the first time.
The EcoPower "clean package" consists of a water-cooling system for the entire machine with a closed cooling circuit, nickel-plated clamping plates, food-grade lubricants and special paint that is resistant to detergent and disinfectant. The control unit can be operated remotely.
The machine also comes with a laminar airflow box, a reject separator and an encapsulated clean-room conveyor belt installed below the clamping unit. Outgoing air is evacuated through pneumatic valves and conduits outside the cleanroom area.
EcoPower series machines, available in sizes ranging from 55 tons to 300 tons of clamping force, feature the kinetic energy-recovery system, an efficient direct drive, compact clamping system and a mold space free of grease through linear guides and enclosed toggles.
For the first time, Wittmann Battenfeld also showed the EcoPower 180/350H/130V Insider.
The Insider system combines the molding machine and automatic parts removal and conveyor belt in a compact unit. Options include custom-built peripheral equipment, downstream finishing equipment and a second conveyor belt. The Insider package is available on machines with up to 300 tons clamping force.
Wittmann Battenfeld's new MicroPower 15/10 medical version comes with an optional full-fledged clean-room production cell with a rotary disc, parts-removal handling device and integrated parts inspection by image processing. The unit also includes a clean-room module that produces Class 6 clean air.
This means that parts can be injected, quality inspected and deposited inside the clean room.
Electric MicroPower series machines, available in 5-15 tons of clamping force, are cost-efficient due to shorter cycle times and lower material and energy costs. Cost savings between 30 percent and 50 percent are possible, compared with standard machines, according to the company.
Every axis of the standard clamping unit is driven by its own servo motor. Finished parts can drop out through the injection chute or be removed by a handling device.
A rotary disc module allows use of a second lower mold half. Parts ejection takes place parallel to injection.
All the new machines use Wittmann Battenfeld's Unilog B6P control system, which can also operate Wittmann Battenfeld robots.
Ron Shinn, editor
Contact:
Wittmann Battenfeld Inc., 860-496-9603, www.wittmann-group.com
Ron Shinn | Editor
Editor Ron Shinn is a co-founder of Plastics Machinery & Manufacturing and has been covering the plastics industry for more than 35 years. He leads the editorial team, directs coverage and sets the editorial calendar. He also writes features, including the Talking Points column and On the Factory Floor, and covers recycling and sustainability for PMM and Plastics Recycling.
Plastics Hall of Fame seeks nominees
Amcor, Berry Global will merge
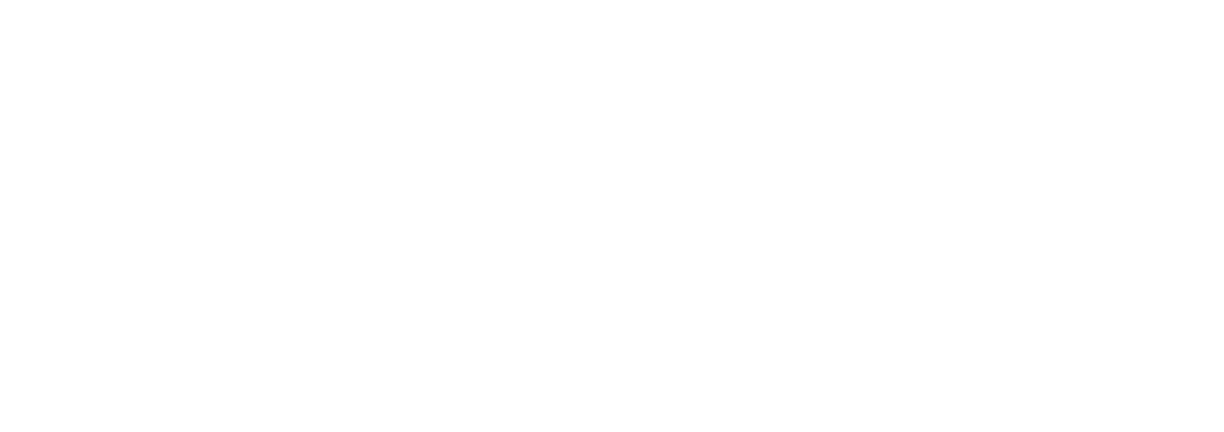