Hot-runner systems with side, direct, sequential and multiple gates showed new routes to molding the perfect part at NPE.
The triennial show ushered in an abundance of hot-runner valve-gate systems targeting high-, mid- and low-cavitation injection molding tooling applications. Whether activated pneumatically, hydraulically or electrically, the products apply new design concepts in the creation of space- and energy-saving tooling.
With the goal of producing a better part with little to no gate vestige, the systems are designed to satisfy any of a number of needs. These can include operating at more uniform temperatures or working better in small spaces on smaller injection presses, or performing with a wider range of materials or parts or at higher production speeds.
'PIN' POINT CONTROL
Synventive Molding Solutions, Peabody, Mass., expanded its activeGate line of valve-gate technologies, designed to precisely control the position, acceleration, velocity and stroke of each valve pin to eliminate flow imbalance issues and aid in the production of parts with optimal dimensional stability and high surface quality in the gating area.
The new nuGate series provides independent valve-pin movement control for valve-gate systems actuated pneumatically in a hot-runner system. The patent-pending system relies on sensor technology employed within the hot runner to provide independent control of each valve pin at each individual gate, says Nancy Tarbox, North American marketing director.
Synventive also rolled out the hGate series, which delivers a similar level of control as the nuGate but is designed for hydraulically actuated valve-gate systems. The nuGate series, suited to select applications, and the hGate series, ideal for cascade or sequential molding, join the eGate electrically actuated valve-gate hot-runner system, which is designed for clean rooms and challenging molding tasks.
The two new styles yield optimum gate control that results in a high-quality molded part. The eGate system, which ensures open and closed positioning of the valve pin to within 0.01mm, is geared for applications that require more precision. Regardless of the power source, the activeGate products speed mold startup, increase production and reduce scrap.
Synventive also displayed SynFlow, a two-speed pin-control technology for use with parts made in single cavities with multiple valve gates. The system, unveiled in 2013 but commercially available for only about a year, provides a more uniform melt-flow velocity and pressure for sequentially valve-gated systems, and can minimize or eliminate pressure spikes, pressure transition marks or an accelerated melt-flow front, reducing potential part defects caused by non-uniform flow.
SynFlow initially reduces the opening speed and length of the valve pin to a defined stroke to prevent a pressure and velocity spike as the melt front passes. Controlling the valve pin opening keeps the flow front from accelerating, resulting in consistent flow-front velocity. In the second step, the valve pin opens at maximum speed for the remainder of its stroke to fill the part.
Users can precisely adjust the start time, speed and length parameters governing the initial opening step. The SynFlow system also provides real-time valve-pin position monitoring, which helps users improve process efficiency.
Parts with superior surface finish are made and defects arising from reduced adhesion of coatings, delamination, sink marks and flow front disturbances are prevented.
MOLD WITHOUT A BLEMISH
Husky Injection Molding Systems Ltd., Bolton, Ontario, introduced its new Ultra Helix series of valve-gate nozzles, designed for direct gating of parts with virtually no gate vestige or stringing. The design and construction of the nozzle follow what Husky calls a first-principles approach in understanding how a gate vestige is formed as well as the fundamentals of valve-gate dynamics, wear and gate quality.
Novel and advanced manufacturing technologies were incorporated into the Ultra Helix nozzle to create a valve gate that guarantees stem-to-gate orifice concentricity that virtually eliminates mechanical wear. The design results in a consistent thermal melt profile that offers a wide processing window for a range of materials, while simplifying the machining required for mold integration, which saves time and money for the mold maker and shortens tool validation times for the molder, says Dave Morton, VP Americas for hot runners and controllers.
Features include a new heater design that Husky says delivers the performance of an integrated heater with the maintenance ease of a removable heater. Heater performance decouples short-shot balance from nozzle heater performance, so that thermal balance of the system is not an issue when replacing a heater, says Norton. "How the heat is applied, retained and sensed, as well as the controlled interface between the heater and thermocouple results in a nozzle design where up to 85 percent of the challenging parts molded experienced no gate vestige," says Norton.
Husky says combining Ultra Helix with its UltraSync-E servo valve-stem actuation eliminates the use of compressed air for actuation, saving energy while making it possible to run the hot-runner system for more than 5 million cycles without having to replace any moving parts.
TARGETING TUBULAR PARTS
Männer USA Inc., Lawrenceville, Ga., developed a new generation of Edgeline valve-gate nozzles for side injection of parts with a tubular geometry like a syringe barrel, having long narrow cores with an opening on both sides.
The Edgeline nozzles feature pins that move at a right angle with respect to the opening and closing of the mold. They are designed to process sensitive and demanding resins such as cyclic olefin copolymer/cyclic olefin polymer, polymethyl methacrylate, polyamide, PC and TPE, as well as commodity grades, without imparting stress on the resins. The design of the valve gate lets the user enjoy the benefits of a hot-runner system with a cylindrical valve gate in applications requiring side injection.
Features include patent-pending heater elements for the nozzle body, tip and base, along with special heat-conducting materials, says Roman Koch, a technical consultant. These features optimize the temperature profile along the entire flow path. In addition, the series features an extended pin opening stroke that increases the open flow area, reducing the pressure through the nozzle, which is a benefit when processing highly viscous resins.
Männer offers Edgeline in two- and four-drop configurations. The two-drop arrangement has an axis spacing of 60mm, while the four-point style has axis spacing of 30mm by 60mm, says Koch.
Männer also improved the capabilities of its Slimline nozzle, created for high-speed, high-cavitation molding of small- and medium-sized technical parts made from engineered resins such as PA, polybutylene terephthalate, polyoxymethylene and liquid crystal polymer.
The new Slimline nozzle combines heating and temperature distribution in a temperature-control element that precisely distributes power over the entire nozzle length for optimal thermal balance. The integration of these elements eliminates the use of a heating coil and a heat-conducting shell. As a result, the nozzle can handle materials over a longer dimension, with a range from 39mm to 164mm.
Other features include a more robust, yet slender nozzle body that has a higher pressure resistance. This design allows for a screw-on nozzle tip that simplifies maintenance. The nozzle tip also houses a pre-centering device for the valve pin for flawless gate quality and high-precision pin movement within the nozzle. The valve pin is first centered by an angled guide area in the nozzle tip then guided into the gate orifice.
The Slimline was also updated with an integrated nozzle seating ring and insulation ring on the nozzle to insulate it thermally from the mold, ensuring a uniform temperature profile. An additional valve-pin guide ring under the nozzle tip guides the pin precisely to the gate as well. Slimline nozzles are now offered in nozzle lengths in increments of 25mm, from 79mm to 204mm.
MULTI-TIP DESIGNS MULTIPLY
Alba Enterprises LLC, Rancho Cucamonga, Calif., debuted the Thermoplay DN5/3 series multi-tip hot-runner nozzles for axial molding of small, precision tubular parts, such as pen barrels, from high-flow polymers such as ABS, PE, PP and PS.
The nozzles, manufactured by Thermoplay SpA, Pont-Saint-Martin, Italy, (represented in the U.S. by Alba) are configured with symmetrically arranged tips that can be positioned with center-to-center distances as small as 3.2mm, making them suited to multi-cavity molding where the distance between the axes is limited, or in small-mold systems with extremely limited areas.
The nozzles are designed to deliver balanced filling, which prevents the formation of flow lines while reducing the risk of core-pin bending caused by high injection pressures, says Richard McGranahan, senior product manager.
GATING ON THE SIDE
The Melt-Cube side gating nozzle tip system from Mold-Masters, Georgetown, Ontario, a division of Milacron LLC, takes aim at side gating small parts molded from crystalline or amorphous materials. Two to 16 cavities per cube can be simultaneously gated with the system, designed with a pitch density that is 20 percent higher versus circular side-gating systems.
Features include minimized gate-to-parting-line distance and the ability to easily remove the gate tips from the parting line. The tips can be positioned horizontally or angled at 15, 30, 45 or 60 degrees. The Melt-Link sliding expansion joint between the nozzle and the Melt-Cube keep the tip centered in the gate even with thermal expansion of the hot runner. The system provides precise cavity- to-cavity balance and excellent vestige control, which allows for easy startups and low injection molding pressures.
NOZZLES HANDLE RANGE OF RESINS
Polyshot Corp. Inc., West Henrietta, N.Y., rolled out a new compact pneumatic valve gate for direct gating of filled or unfilled engineering or commodity resins. The new single nozzle valve gate can be used in clean-room applications and handles materials with high processing temperatures in shot sizes from 10 to 500 grams.
The entire assembly, including the pneumatic actuating cylinder, is contained within the mold locating ring and the overall stack height is reduced. The valve gate uses fewer components, shunning cams or levers, reducing plate machining requirements. The air-powered piston system delivers a nozzle pin force of 400 pounds.
MINI HITS IT BIG
Gunther Hot Runner Systems Inc., Hoffman Estates, Ill., introduced its Oktaflow line of multi-tip hot-runner nozzles designed for direct side gating of small parts. As many as eight tips per nozzle can be configured on the nozzle in either a radial or linear design. They can be used in conjunction with a heated adapter or in combination with a manifold for multi-cavity injection molding.
The pins can be arranged in a pitch circle with a center-to-center distance of 45mm, or if in a linear arrangement, can be installed in a mini-manifold supported by floating bearings, which minimizes the effect of thermal expansion. Heating at the gate area optimizes the temperature profile for the direct injection of parts.
The tips can be replaced individually from the direction of the split line, an approach that does not require the mold to be completely disassembled.
Optional wear-resistance nozzle tips can be used for processing filled materials. Other features include easy-to-install, plug-in power and thermocouple connections.
CAN I BORE YOU
Mastip Inc., Slinger, Wis., expanded its TL line of threaded nozzles with its new TL35 design. The product line eliminates tool contact between the hot-runner nozzle and the mold—which is usually a requirement for traditional face-to-face sealing nozzles. Its design reduces heat loss, promotes a smooth thermal transition between manifold and nozzle and reduces overall energy consumption by the hot runner, says regional manager Tony Brodzeller.
Key features include a configurable nozzle offering flow bores from 14mm to 18mm and lengths from 150mm to 600mm with multiple heating zones that improve the thermal profile. Six nozzles in the line handle shot weights from 1 gram to 2,200 grams.
The nozzle can handle filling pressures up to 130 megapascals. Valve-gate options were added to the TL line in 2014 and joined existing thermal gate nozzle options.
The thermal profile of the TL35 nozzle is provided by coil heaters using premium heater technology, says Brodzeller. Closely integrated thermocouples control individual heating zones.
Mikell Knights, senior correspondent
Contact:
Alba Enterprises LLC, 909-941-0600, www.albaent.com
Gunther Hot Runner Systems Inc., 630-293-4650, www.guenther-hotrunner.com
Husky Injection Molding Systems Ltd., 905-951-5000, www.husky.co
Männer USA Inc., 770-449-1820, www.maenner-group.com
Mastip Inc., 262-644-9400, www.mastip.com
Mold-Masters, 800-387-2483, www.moldmasters.com
Polyshot Corp. Inc., 585-292-5010, www.polyshot.com
Synventive Molding Solutions, 978-750-8065, www.synventive.com
Plastics Hall of Fame seeks nominees
Amcor, Berry Global will merge
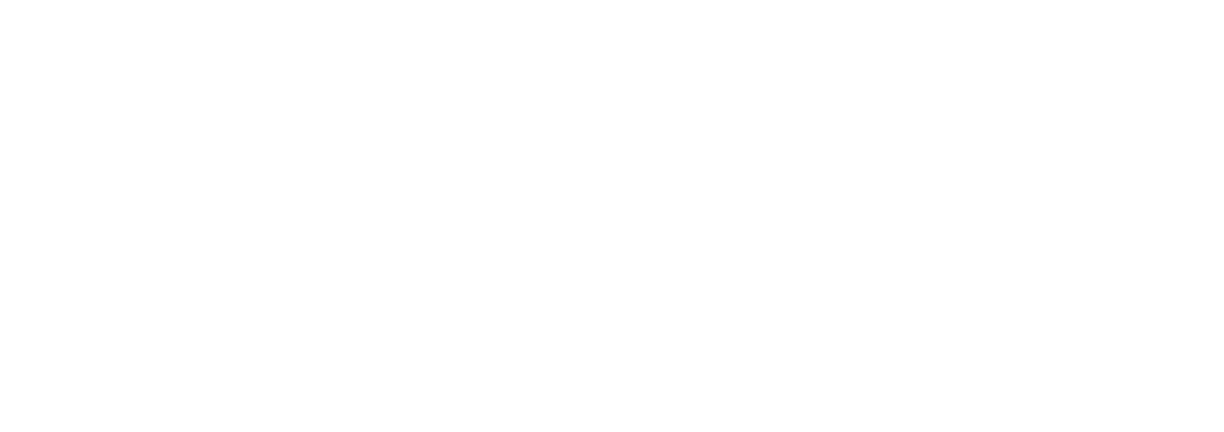