Industry terminology usually defines granulators as machines that provide pellets of a size determined by the use of an internal screen. Shredders tend to produce strips, typically larger than what comes out of granulators. Shredders can handle film, sheet, and other products that are not as well suited to granulators.
However, at least three suppliers at NPE— Cumberland, Republic Machine and Vecoplan LLC—offered combo units, in which a shredder and granulator are combined to perform both operations. The units are sometimes literally bolted together, or can stand side by side.
The Combi-Shredder from Cumberland, New Berlin, Wis., has a shredder stacked onto the granulator so that shredded scrap is directly discharged to the granulator. This eliminates the need for separate conveying steps, saves time and can reduce energy consumption at throughputs of 1,100 to 1,540 pounds per hour. The combined shredder-granulator also uses less space compared to separate machines.
The Combi-Shredder has a cutter reversal mechanism designed to prevent structural overload, which can lead to machine damage. The rotor recirculates partially shredded material prior to granulation, ensuring scrap size suitable for granulation. To avoid damage, blade level sensors automatically shut the Combi-Shredder down when clogged. An anti-torsion shaft is designed to resist stress for longer life. Mechanical components can be readily accessed, removed and reinstalled to reduce downtime for maintenance. The controls use a color touch screen to show operating parameters and diagnostic information.
Republic Machine, Louisville, Ky., highlighted the RM shredder/granulator system, well suited for large bales, thick purgings and pipe. Its dump-and-run operation eliminates the need for pre-cutting and continuous feeding by a staff member. A 15:1 gear-reduced drive train minimizes energy requirements. The system is available stacked for minimal footprint and throughput of 3,000 pounds per hour, or separate, which increases throughput to 6,000 pounds per hour. The unit is operated with an Allen-Bradley PLC.
Vecoplan, Archdale, N.C., has engineered the VAZ 1100U Stack System, which adopts the principle of getting the best of both high-torque and low-torque units. By combining the shredder and granulator, one gets the advantage of both technologies. The shredder's discharge opening is bolted directly to the infeed opening of the granulator.
A single-shaft, rotary, low-speed, high-torque shredder reduces tough plastic scrap from approximately 1-inch-diameter scrap to the size needed for reprocessing, 3/8 inch or smaller, with a cutting rotor turning at high speeds but with low torque, which is done by a Rotogran granulator.
HYBRID FUNCTION
Herbold Meckesheim USA, Slatersville, R.I., has designed the HB Series granulator/shredder, which is constructed as one unit but is set up to combine the attributes of a shredder and a granulator, reducing bulky items down to particle sizes of 0.16 to 0.31 inches in diameter without any secondary size reduction.
The HB Series units have a rotor with double-cross cutting action, a heavy-duty hydraulic ram, and a large feed hopper than can handle whole bales, cut-open feed rolls, mingled packs of sprues and runners, thick-walled purgings, pipes and profiles, post-consumer bottles, and containers/crates without the need for dosed feeding or the risk of jams in the cutting chamber.
Once the hopper is filled, the unit can be left unattended. The ram runs intermittently, breaking pieces off the bottom of the load and pushing them into the cutting chamber.
RECOVERING AN INVESTMENT,
TARGETING A PROCESS
As David Miller of Rapid Granulator Inc., Cranberry Township, Pa., reports, as many as 70 percent of size-reduction machines are tailored in some way for a particular processor, even in what might seem like an off-the-shelf commodity machine market. Miller notes that return-on-investment analysis of recycling equipment can be very important in this price-sensitive market.
Rapid promoted its open-hearted concept, which allows opening the cutter housing completely for access to core machine parts, providing for full visual inspection. Easy access for service and maintenance allows, for example, quick knife changes. The granulators provide the Constant Cutting Circle, which is the ability to keep the cutting circle the same in a granulator even after knife sharpening, says Miller. Scissors action provides sharply cut regrind and minimizes energy consumption.
Also, in the highly competitive size-reduction business, it is increasingly common to see specific models of granulators or grinders targeted to specific processes, such as thermoforming or blow molding, in which the material to be handled has certain well-known characteristics. Blow molded bottles, for example, are bulky and frequently of a single material that can be identified in advance.
Conair Group, Cranberry Township, offers 36-, 48- and 60-inch infeed thermoforming scrap granulators for either single-sheet or continuous feed. The product is in flake form. A paddle-wheel feed is optional. The thermoforming scrap granulator was brand new at NPE.
Tria America Inc., Charlotte, N.C., offers to customize machines to meet processor needs. One capability it cites is the ability to grind 30,000 PET preforms per hour (2,000 pounds per hour) using a 20-horsepower machine. The TF Series, on the other hand, is designed for thermoformed scrap recovery, including "skeletal" scrap and sheets with cups up to 4 inches in height as well as lids. Six machines with different feed-opening lengths and rotor sizes have output ranges of 400 to 2,000 pounds per hour.
Foremost Machine Builders Inc., Fairfield, N.J., has added an air-relief elbow to the hopper design of its Futura grinder. The company has upgraded the Model QG-1814 Futura Series grinder by providing a double-walled hopper and sound-absorption cabinet. The grinder also has a right-angle cutting chamber that incorporates an offset rotor to accept bulky parts while minimizing fly back. Aimed at blow molded container applications, this feature allows the blowing of trim scrap and off-spec bottles directly into the grinder. Since noise is minimized, bottle manufacturers find it less necessary to locate this grinder in a separate grinding room.
Zerma America, Crystal Lake, Ill., has tailored its GST series of compact soundproofed granulators with tangential infeed and cutting chamber to the in-house recycling of blow molded parts and flash. The newly designed cutting chamber features a curved rear wall to ensure an aggressive intake while also avoiding blockages.
These new granulators are available in two rotor diameters, 250mm and 400mm, with widths ranging from 300mm to 1,000mm. While the smaller machines feature an open F-type rotor, the bigger machines rely on a heavier S rotor. Replaceable wear plates are standard. Knives are adjustable from outside the machine.
MORE DISCRETE UNITS
OFFER A WORLD OF CHOICES
Avian (USA) Machinery LLC, Naperville, Ill., featured the GN110/G80 heavy-duty granulator with a 130-200 kilowatt motor and a 32- by 48-inch cutting chamber. The cutting knives are 2 inches by 3, 5, 7 or 9 inches and the stationary knives are 2 inches by 2 or 3 inches. Screen holes are 1/16 inch to 2 inches.
The Sterling 6.5 Series beside-the-pressgranulator from Sterling, New Berlin, Wis., is well-suited for use with small injection or blow molded parts, small extruded tubes and profiles, sprues, runners and edge trims. A reversible, multi-feed hopper design allows for hand, conveyor or robot feed applications. A window allows inspection and a vacuum discharge integrates regrind into the material process flow. Heavy-duty, high carbon, high chromium D2 steel is used for the rotor and knives, while an enclosed, fan-cooled, 1,800 rpm motor delivers efficient, low-speed granulation. Cutting chamber sizes of 6.5 inches by 8 inches, 6.5 inches by 12 inches and 6.5 inches by 16 inches with a cutting circle diameter of 6.5 inches provide throughputs up to 100 pounds per hour.
For Shini USA, Willoughby, Ohio, the SG-14 and SG-24N screenless granulators use teeth cutter and cutter blades that are integrally fitted in one cutting chamber. Inclined teeth cutters reduce the possibility of stress concentration, enhance bearing capacity and convert force direction to prolong cutter lifespan. When motor blockage occurs, the machine will provide a visible alarm and enable the motor to reverse direction. Operation returns to normal automatically after the blockage is cleared. The feed hopper is of transparent polycarbonate. The screenless design minimizes dust generation.
Virtus Equipment, Crystal Lake, Ill., showed its A-Series slow-speed granulator, which features a staggered rotor directly driven by a geared motor. The company started marketing it directly to the U.S. in March. The 150-rpm rotor speed reduces the noise level of the machine and creates less dust while grinding. The specially designed knives of the A Series can be sharpened easily and do not need adjustment afterwards. The material is fed via a sound-absorbing feed hopper that can be tailored to fit various applications and various feed directions.
New at NPE from Weima America Inc., Fort Mill, S.C., was the WLK 800-2000 Series single-shaft shredders in four models. The versatile shredder handles purgings, rejected crates and bins and film. Standard features include pipe-spacer hopper design for bulky materials, segmented floor for precise ram guidance, load-dependent, controlled feeding, reversible counter knives and PLC for ease of operation. The basket system is hydraulically driven, allowing easy access for rapid screen changes. The rotor design is well-suited for minimum wear of cutting tools. The drive is provided by Weima. Offset bearings offer ease of maintenance.
These hopper-fed shredders are designed for dump-and-run use, which means the machine can be unattended while the shredding is accomplished, and come equipped with a large custom hopper for easy loading by forklift, box or conveyor. Optionally, Weima can prepare the rotor for cooling or plate it with abrasion-resistant material.
Merle R. Snyder, senior correspondent
Contact:
Avian (USA) Machinery LLC,630-687-9876, www.aviangranulator.usConair Group, 724-584-5500, www.conairgroup.com Cumberland, 262-641-8600, www.cumberland-plastics.comForemost Machine Builders Inc., 973-227-0700, www.foremostmachine.comHerbold Meckesheim USA,401-597-5500, www.herboldusa.comRapid Granulator Inc., 724-584-5220, www.rapidgranulator.comRepublic Machine, 502-637-6778, www.republicmachine.comShini USA, 440-530-1000, www.shiniusa.comSterling, 262-641-8610, www.sterlco.comTria America Inc., 704-716-0060, www.triaamerica.comVecoplan LLC, 336-861-6070, www.vecoplanllc.comVirtus Equipment, 815-477-2100, www.virtus-equipment.comWeima America Inc., 803-802-7170, www.weima.com/usaZerma America, 815-477-2800, www.zerma.com
Plastics Hall of Fame seeks nominees
Amcor, Berry Global will merge
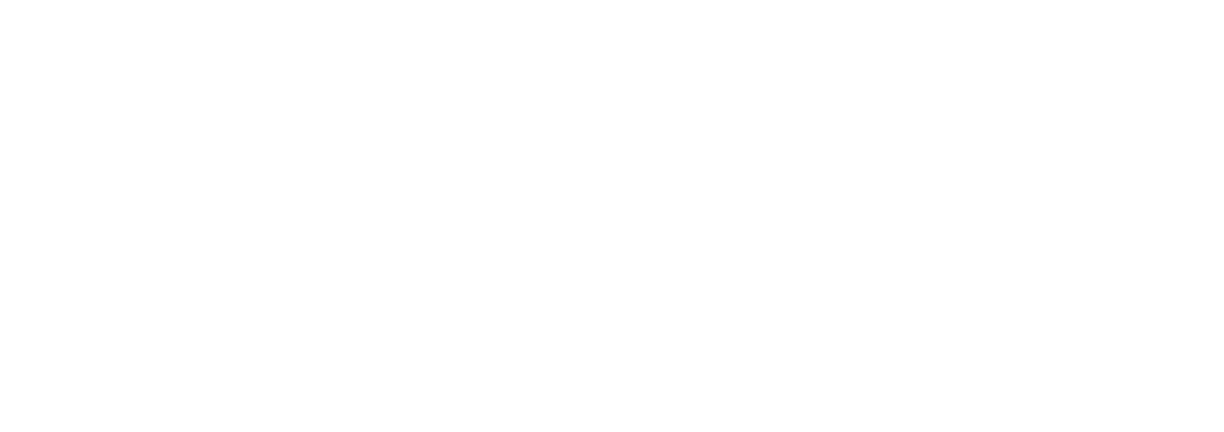