Stop for a few seconds and think about what we call auxiliaries. Fact is, they are absolutely essential in every type of plastics processing. Does anyone mold or extrude plastics without a well-engineered materials feeder? Maybe, but not for very long. We need a better word than auxiliary.
The Latin root of auxiliary means helpful, or aid/help/support, which makes the equipment sound like add-ons—nice to have but not critical, which is just plain wrong. Thankfully there's another meaning of auxiliary: foreign troops in service of a nation at war. At NPE, there were many conveying, blending and feeding innovations that could help a processor win the day, or a tough shift.
Networking the stand-alones,
fine tuning the feed
Injection machines were the biggest things in the NPE stand of Wittmann Battenfeld Inc., Torrington, Conn., but the large number and variety of material handling and other auxiliary equipment on display made an equally powerful statement, and many of those units were new technology. That included several impressive pieces of material conveying and blending machinery.
With the buzz about Industry 4.0 gaining volume, even if you don't know much about it you can be sure that communications is at its heart, everything talking with everything else. A major innovation in Wittmann's new Feedmax S3 net single conveying system is the ease with which it can be joined with all neighboring equipment on the same network. Six of these systems were ordered during the show, as part of an order for three Wittmann turnkey injection molding work cells.
Until now, stopping or adjusting a single conveyor system had to be done manually, sometimes on a ladder. The Feedmax S3 takes the step of combining single conveying units with a centralized control system. Using a controller area network bus (CAN bus), several Feedmax S3 units can be linked together and controlled from a single console. Wittmann provides a high-resolution TFT 4.3-inch touch-screen interface to do just that, and it displays complete information on the status of each unit. The individual conveyor units each have an LED status display as standard issue, so operators can check the unit's status quickly, even at a distance.
During NPE, Wittmann also released its new Gravimax G56 gravimetric blender, which will mix as many as six different components and has a total blending volume of 176 ounces. Dosing is done by pneumatically operated, wear-resistant metering valves with cylinders outside the material flow to prevent material bridging. The design also makes cleaning much easier. The blender includes a real-time live scale (RTLS) weighing unit that determines how often and for how long every metering valve must be activated, which enables metering accuracy of plus or minus 0.1 percent.
The user interface of all new G Series blenders lets users work with or without formulations and automatically optimize the loading sequence of individual components. And its SmartRegrind function prevents the processing machine from stopping due to lack of resin—the Gravimax will supply the missing component automatically.
Two other Gravimax systems made their premiere at NPE: the Gravimax G14 with up to 176 pounds per hour of throughput and the Gravimax G34 with maximum throughput of 441 pounds per hour. Both are fitted with a modernized control system that delivers higher performance and higher precision in metering, even under adverse conditions. The stainless steel valves, suitable for virtually any materials (virgin, regrind, masterbatch, additives), are unchanged from the predecessor series, and they are both configured for RTLS operation. Continuous weighing ensures the highest precision in every batch of compound.
Pumping liquid color
20 percent more accurately
The PeriStep liquid color pump Maguire Products Inc., Aston, Pa., unveiled at NPE is a completely new design. The company says that, even though it meters color into a molding or extrusion process about 20 percent more accurately than existing equipment, simplifies startups and color changes and needs minimal maintenance, it costs about 35 percent less than other current choices.
Two patent-pending innovations are the keys to the PeriStep's lower cost and high accuracy. Rather than a standard motor, the drive system is a stepper motor, the shaft of which rotates in minute increments that make high precision not only possible but also repeatable. The motor drives a central sun roller that transfers its motion to the outer planetary rollers to create the compression/relaxation cycle of a peristaltic pump. There are four planetary rollers instead of the conventional six. A 5-to-1 speed reduction is provided without a gearbox as the sun roller drives the planetary rollers by friction contact.
Steve Maguire, president of Maguire Products, said the streamlined design of the PeriStep pump—there are no gears or bearings to wear out—minimizes maintenance. "If it does become necessary to disassemble the pump, access to the roller set involves simply removing three screws in the cover." Job setup takes just three intuitive digital inputs: shot weight for injection molding or extrusion rate, liquid color percentage and density of the liquid color. The pump includes a self-adjusting automatic speed control that maintains dosing consistency.
Flexible, high-performance
conveying and blending
The multifaceted ACS Group, Schaumburg, Ill., came to NPE with new branding, including for its material handling products. The company has recently streamlined its internal working processes. The efficient, lean approach has proved so successful internally that the company decided to take the same approach with its customers. Products and services are conceived and positioned to solve customer problems effectively, efficiently and simply.
The company's AEC brand of materials handling equipment that was on display showcased the efficiency-focused approach. The VP Series of vacuum pumps, which was making its NPE debut, provides a complete conveying system—controls, filter and blower—in a compact package. It gives processors flexibility and combines that with broad capabilities. Using different filter types, the VP system can convey pellets, pellets and regrind, or pellets/dusty regrind/granulate over short and medium distances in an open- or closed-loop operation. Single-station, four-station or nine-station controls are available and the unit is on casters, so it can be moved easily.
Also prominent in AEC's area of the booth was the BD Series of batch gravimetric blenders. The series joins advanced technologies with proven component designs to provide processors flexibility, as well as high accuracy. Heavy-duty, diamond-design metering gate assemblies provide 0.5 percent to 100 percent range accuracy for free-flowing materials. The modular construction is rugged for production environments, while the touch-screen control system combines power and ease of use, and offers three distinct methods of entering recipe data and operating instructions.
One-component feeding
that's accurate and economical
In the booth of Comet Plastic Equipment LLC, Riviera Beach, Fla., Tom Rajkovich, Comet's president, was staying busy detailing the benefits of Comet's new ColorSave Micro (CSM), a compact, single-component gravimetric feeder using a newly patented system to precisely feed small quantities, even single pellets, of color concentrate and other additives directly into the feed throat of injection, extrusion or blow molding machines.
The ColorSave Micro continuously monitors the load cells, which are protected in open hoppers with no gates to open and close, and accurately tracks the weight-loss rate from the feeder. Rajkovich says the feeder can be adjusted on the fly and can go from the lowest rate to the highest without changing any parts. While the feed is controlled by weight, the pellets are moved by vibration, so the rate can be adjusted by changing the vibration frequency.
Comet says that, on average, the CSM saves 33 percent on color concentrate compared with volumetric blenders mounted on a machine's feed throat. Weigh cells are not affected by vibrations from the processing machine, the company says, and the unit's function and accuracy also are not affected by external loads or forces. Rajkovich noted that setup and maintenance time has been minimized and that its $2,799 price makes the ColorSave Micro cost-effective.
Managing air speed to reduce
elbow wear and angel hair
High-speed vacuum conveying can result in issues such as wearing of the equipment and of course, angel hair, that perennial problem in materials conveying. Also known as streamers and snakeskins, these fine filaments can accumulate and eventually obstruct or even block passage of pellets through the lines of materials conveying systems.
Two companies introduced systems to address these problems. Conair Group, Cranberry Township, Pa., now has its patent-pending R-PRO (ResinProtect) conveying system that is comprised mainly of standard vacuum-conveying components. It can be retrofitted to existing
systems; more on the product is included on Page 9 of this issue.
Novatec, Baltimore, is focusing on controlling velocity. Officials there believe managing air speed can help and to that end they have introduced new air-speed management tools.
The company's patent-pending Air Flow Regulator, is a flow control valve that acts like a governor on the air speed inside the conveying system. When system resistance drops, air flow is limited to prevent air speed from increasing. When system resistance already is high, air passes through freely. This valve acts automatically to changing system conditions and no control interface is required.
It is a mechanical enhancement to a conveying system, officials said, and users will not need a variable-frequency driver (VFD).
Novatec also has its advanced FX2 conveying control that allows conveying speed selection for individual stations through optional pump motor VFD. Air speed can be reduced for abrasive and fragile materials or short distances. It can be increased for very heavy and other challenging materials or long distances. This FX2 can also vary speed during a fill cycle, the company says, starting at full speed to reliably start material movement, then slowing to the target transfer speed.
This product can be used with the Air Flow Regulator, a patent-pending combination. When the two are combined, the system sets the maximum air speed to the target setting and automatically adjusts to changing system conditions to prevent the air speed from increasing. A bypass kit can be added to move at elevated speeds in the same system when needed. A patent is pending on that kit.
"We're trying to look at where damage really occurs and focus on that," says Jim Zinski, VP, system design.
Angel hair removal gets automated
Lorenz Conveying Products Corp., Cobourg, Ontario, had a sign in the main corridor of the West Hall directing people to the NPE debut of a product that indicates how deeply automation innovation is spreading throughout plastics processing. Its product addresses angel hair in material conveying.
Lorenz has been supplying a solution to that problem for some time — its in-line angel hair trap. The trap catches and collects angel hair moving through the line while letting the pellets pass through. The filaments then can be easily removed from the trap. But not easily enough to suit Lorenz, so at NPE the company launched its automated in-line angel hair trap.
The automated system incorporates a control system and two traps. One trap collects angel hair until a sensor signals that it's full. The control then switches the material flow to the second trap. The first trap is ready for emptying, which is when the big benefit of this design appears. There is no downtime required to empty the full trap because it is off-line.
Lorenz in-line angel hair traps are made for both vacuum lines and pressure conveying systems. Standard body sizes are 8, 10 and 18 inches with line outside diameter (OD) sizes from 1.5 to 6 inches. The body is 12-gauge stainless steel. Line connections are made with compression couplings. Lorenz makes all components in-house.
Rob Neilley, senior correspondent
Contact:
AEC, 847-273-7700, www.aecinternet.comComet Plastic Equipment LLC, 800-328-5088, www.cometpe.comConair Group, 724-584-5500, www.conairgroup.comLorenz Conveying Products Corp., 905-372-2240, www.lorenz.caMaguire Products Inc., 610-459-4300, www.maguire.comNovatec, 410-789-4811, www.novatec.comWittmann Battenfeld Inc., 860-496-9603, www.wittmann-group.com
Plastics Hall of Fame seeks nominees
Amcor, Berry Global will merge
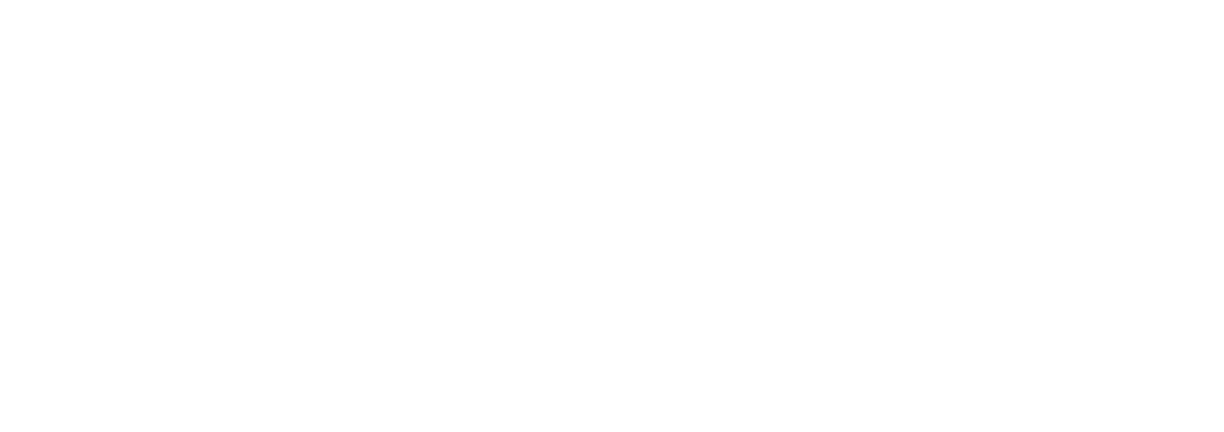