Plastics machinery makers have been designing safety features into their products for, well, virtually forever. The industry doesn't necessarily hear much about them because machine makers tend to promote the technologies that will give a processor higher throughput, better quality, energy or other cost savings and a quick return on investment.
In a recent conversation with a leading extrusion systems supplier about the newest version of its control system, PMM learned that many features had been added, and that, overall, the human-machine interface (HMI) was more graphic and easier to use. What emerged in the final descriptions of all these new features was a common thread: Each new feature made the operator's job easier, making the operator more productive and speeding up operations.
There was a second common thread that ran parallel to the first.
Picture a cast film or blown film extrusion line. Now think of its footprint. It's not small and the line's components, from material feeding to finished roll removal, extend across the floor. In the old days, before computer controls emerged in the 1970s and 1980s, an operator, or more likely, operators, were moving around the line to adjust various components. But every new feature of this machinery maker's new control system relates to, and is accessed from, the control panel.
As computerized controls become more inclusive, the physical contact between the machine's operator and the mechanical aspects of the machine has been notably reduced — greatly reducing the possibility for accidents.
And that trend is continuing.
Control systems that boost safety
Chuck Flammer, VP of North American sales at blow molding systems maker Kautex Machines Inc., North Branch, N.J., says the controls on Kautex machines are definitely a safety feature.
"The control has screens that show where a gate is open or a switch is tripped," says Flammer, who works on a subcommittee of the Machinery Safety Standards Committee of the SPI.
Kautex has been replacing hydraulic and electric switches with dedicated safety PLCs, which are both more reliable and more difficult to defeat.
Injection molding machine maker Engel Machinery Inc., York, Pa., emphasizes ease of operation when describing the CC300, the latest generation of its control system.
"As production processes are becoming more complex from time to time, with a higher degree of automation and process integration, it is important to reduce the complexity of the control," said an Engel spokesperson.
The CC300 provides separate pages for specific functions like maintenance, mold changing and process optimization. The result, Engel says, is that feature prevents possible errors that could create the need for contact between human and machine.
The company recognizes that sometimes contact is necessary. For its large duo two-platen machines (up to 5,000 tons), Engel offers users a couple of safety-oriented options. First is a lifting platform to facilitate setup and maintenance in the mold area. The movable platform, which clamps to the machine frame, has a lifting mechanism and pneumatically operated extensions on two sides, and an easy-to-use hand control system.
The second duo option is a service platform with a variable, partially enclosed ladder that Engel says gives the best access to the injection unit and makes working in the material feeding area or changing a barrel convenient and safer.
Rob Neilley, senior correspondent
Contact:
Engel Machinery Inc.,
717-764-6818, www.engelglobal.com
Kautex Machines Inc.,
908-252-9350, www.kautex-group.com
Plastics Hall of Fame seeks nominees
Amcor, Berry Global will merge
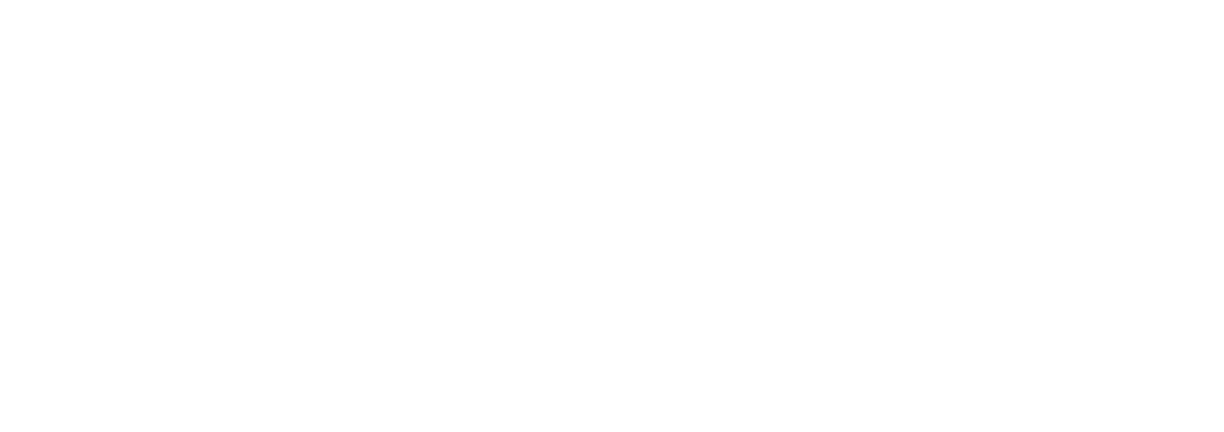