Extrusion of multilayer film and sheet structures that include groups of exceptionally thin layers is definitely on the rise, finding applications and markets even as much development is in process. It is a minor part of the overall film and sheet market now, but the opportunities it offers to both processors and end users point toward a bright future.
PMM asked two leading suppliers of the micro- or nano-feed block and die technology — Nordson Extrusion Dies Industries, Chippewa Falls, Wis., and Cloeren Inc., Orange, Texas, to talk about their respective technologies.
The science of slicing
to multiply layers
Nordson Extrusion Dies Industries began working on its technology with a license from Dow Chemical Co., Midland, Mich., about 12 years ago. Nordson has since designed and developed its proprietary Layer Multiplication Technology (LMT), and it has been in the market for about eight years. The technology has found applications around the world.
LMT is based on having a conventional co-extrusion stream delivered to layer multiplication elements, explains Sam Iuliano, the company's chief technologist.
"Each doubling element slices the co-ex stream down the middle, re-orients the two resulting streams and stacks them one on top of the other. Subsequent doubling elements in the path continue to double the number of layers," he says. "We carefully design the LMT doubling elements and are able to maintain continuous layers thanks to laminar flow, symmetry, and large aspect ratios (not square paths, but rectangular) to minimize co-extrusion interface distortion. We use 3-D FEM modeling to optimize the die, feed block and LMT geometry in a way that maintains uniform layers."
The latest developments in LMT technology include new flow path layouts that can include multiple planes of multiplication, allowing the processors to put un-multiplied bulk layers in between groups of micro-layers. In addition, LMT systems can be included in a package with feed blocks that have pivoting, combining planes. Iuliano says this allows for on-the-fly ratio changes, with LMT as part of a feed block system that has one selector spool used to set the layer sequence for all of the streams, permitting quick changes to the structure with minimal down time.
Nordson has installed LMT-enabled stretch film systems in Asia and Europe; LMT cast bubble film systems in the U.S. and Europe; LMT-enabled extrusion coating in Europe; and an LMT line is making barrier sheet for thermoformed cups in Asia, among other regions. The company currently is seeing the most interest from barrier sheet makers, followed by stretch film, extrusion coating and cast film other than stretch, plus interest is growing among biaxially oriented film makers.
The LMT elements are located in separate housings that fit between two feed blocks or are incorporated within a feed block. That choice means a processor with an existing feed block needs only an LMT housing, and if only a modest amount of multiplication is needed, Nordson EDI can easily incorporate it within a new feed block for an existing system.
"What our Layer Multiplication Technology does is create multiple layers using a very streamlined and compact system," says Iuliano. The LMT system has much shorter flow paths than other solutions on the market and is physically smaller. Benefits of that include lower back pressure, so production rates are not limited and leakage issues are avoided. Other benefits include less wetted area, better streamlining, shorter resin change time and, because the parts are smaller, easier changeover to another structure.
Nordson EDI has further leveraged the lower back pressure advantage through a very recent development. It now has developed an Equivalent Volume design for the doubling inserts, Iuliano says. These generate the same back pressure as would a wide open pass-through channel. The EV LMT elements help maintain full production capacity due to the minimal impact on system back pressure.
The ability to quickly change to a new structure is especially useful in R&D settings where different multiplication levels are being tried. For example, an extrusion coating line in the lab of a major resin producer in the U.S. that runs a conventional five-layer structure can install two LMT elements and run up to 14 layers. The whole feed block, including layer multiplication elements, is only about 30 inches top to bottom.
When it comes to very thin layers, one challenge is co-extrusion instability, Iuliano says. The system has to be designed to resist it. Very thin layers should not be close to the die walls, which is a high-stress area. If they are, line speed, viscosity ratios and the overall operating window has to be limited to maintain stable co-extrusion.
"Generally, you use outer layers of conventional thickness called protective boundary layers to keep the first micro-layer safely away from the die and channel walls," he says. "When we incorporate LMT into a feed block there are always final co-extrusion inserts after the LMT to add the protective boundary layers."
What layer multiplication
does, and why do it
Iuliano says one of the clearest examples of what layer multiplication can do is in thermoform sheet for barrier applications, largely food packaging. A conventional five- or seven-layer structure could have one EVOH (ethylene vinyl alcohol) barrier layer, tie layers, recycled layers, and some virgin layers. With thermoform sheet for food cups, Nordson found that, if instead of one EVOH layer the structure has four EVOH layers, each a quarter the thickness of the conventional single layer, the oxygen barrier in the thermoformed cup is better. The most likely reason for that is formability. EVOH is a quite brittle crystalline material, and often when a cup is formed, the EVOH near the corners becomes quite thin because it doesn't draw very easily. Make the EVOH layers thinner and they become more pliable, and form better in the corners. Lab results at the EDI technology center showed a significant reduction in the oxygen transmission rate for multiplied sheet versus conventional barrier sheet.
When it comes to films, Iuliano says the biggest improvement from layer multiplication is improved resistance to flexing and stressing. As with sheet, the thinner layers are more pliable. It may seem illogical that the thinner layers are more stress-resistant, but it is precisely because they are thinner. There are limits, though, to how thin the multiplied barrier layers can be. Nordson EDI testing showed that, for some film structures, when the single EVOH barrier layer was multiplied more than four times, the barrier function was reduced. Iuliano said that is why the advantage of layer multiplication is bigger in sheet than in film, where the already-thin barrier layer can become dangerously thin.
Cast film applications using layer multiplication technology have increased over recent years, mainly because of system flexibility and versatility. These LMT systems allow processors to experiment with a variety of materials in different configurations, including different layer ratios, with quick, on-the-fly changes and minimal line down time and maintenance. The primary objective in using this technology is to obtain better mechanical properties in the film, especially in the highly competitive stretch film market.
It's worth noting that multiplying layers, say from five-layer to 20-layer sheet or film, does not add thickness to the final product. If it was 12 mils coming out of the die using a conventional co-extrusion system, it is still 12 mils coming out of the die when using an LMT system. The multiplication is internal.
Is there a limit to how many layers can be made? According to Iuliano, with Nordson EDI's technology it depends on how many layer multiplication elements are used and, of course, on how many the processor wants. Structures of more than a thousand layers have been created in the Nordson EDI laboratory, but when the conversation is about hundreds, the objective is most likely manipulating light. Creating the desired prism effect may take thousands of layers.
Go with the NanoLayer flow
Cloeren has supplied more than two dozen of its NanoLayer systems to state-of-the-art stretch film processors all over the world, with the most recent system sold in the ASEAN region. Officials from Cloeren say that one of the most significant applications of NanoLayer coextrusion technology is in the area of stretch film.
Stretch film is indeed a cost-driven, commodity product, they said. However, it has a critical role of protecting and containing goods during shipping. Recent studies estimate the annual loss due to unsalable product because of damage during handling and transportation at $2.6 billion.
Cloeren's specific co-extrusion technology that is suited to high performance stretch film is its NanoLayer feed block. This feed block is particularly engineered for control of the individual nano-layer flow rate. Each nano-layer is created by a specific flow channel that is rheologically optimized. This, officials said, is critical to maintain the integrity of each layer even at production rates on wide dies. Another particularity of the feed block is its flexibility in the design of the coextruded structure. For example, functional nano-layer packages can be designed and located near the skin layers, which is optimal for puncture resistance.
As sustainability and downgauging become more of the norm, stretch films will benefit from the technology. The main idea with very thin alternating layers is that it opens the possibility in terms of material selection, officials said. LLDPE and metallocene polyethylene (mPE) are materials of choice due to their stretchability. Stiffer materials such as PP would add the benefit of maintaining properties at higher temperature (warmer climate) but with the potential drawback of affecting the stretchability when used as bulk layers. When used in thin alternating layers, however, it is possible to produce films with increased toughness and puncture resistance. The performance increase can also be seen as a new opportunity to downgauge and reduce the overall carbon footprint of goods.
Bonus for barrier
Cloeren officials say that industrial application of NanoLayer co-extrsion technology in barrier films is in its infancy. But barrier films are growing because of the increasing demands in food packaging. Consumers expect more performance out of food packaging. They want increased shelf life and single-serve portioning for food that's fresh and healthy yet also readily available.
Food packaging, however, is not the only market that requires the benefits of barrier. Others include medical and pharmaceutical, construction and agriculture.
Within the packaging industry, barrier films are pushing the envelope of complex extrusion systems, according to Cloeren officials. State-of-the-art producers of barrier films continue to optimize structures. The more common trends are increased width, more layers, and thinner films. Nine- to 13-layer systems are no longer the exception, but rather the norm in barrier films.
Improvements in the design of feed block and flat die systems have allowed producers to expand from simple five- to seven-layer structures to more complex 11-layer and asymmetric structures comprised of multiple functional layers for high barrier and modified atmosphere applications. Cloeren has provided more than 40 cast barrier film co-extrusion systems with nine or more layers (not including NanoLayer systems) to the global industry.
Rob Neilley, senior correspondent
Plastics Hall of Fame seeks nominees
Amcor, Berry Global will merge
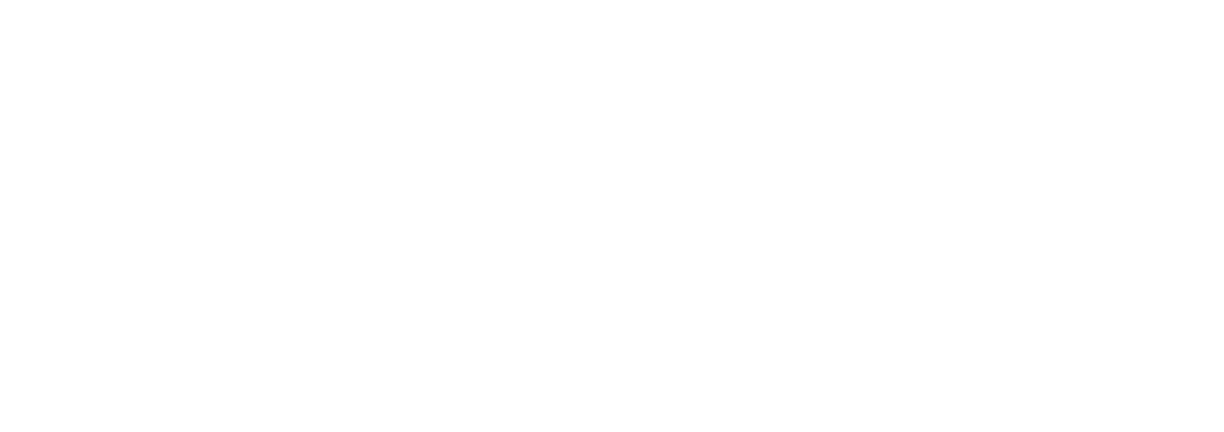